Comparing PVDF and Nitrocellulose: Key Insights
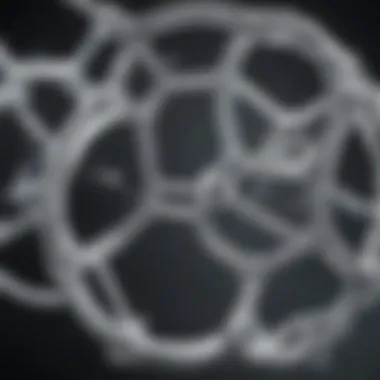
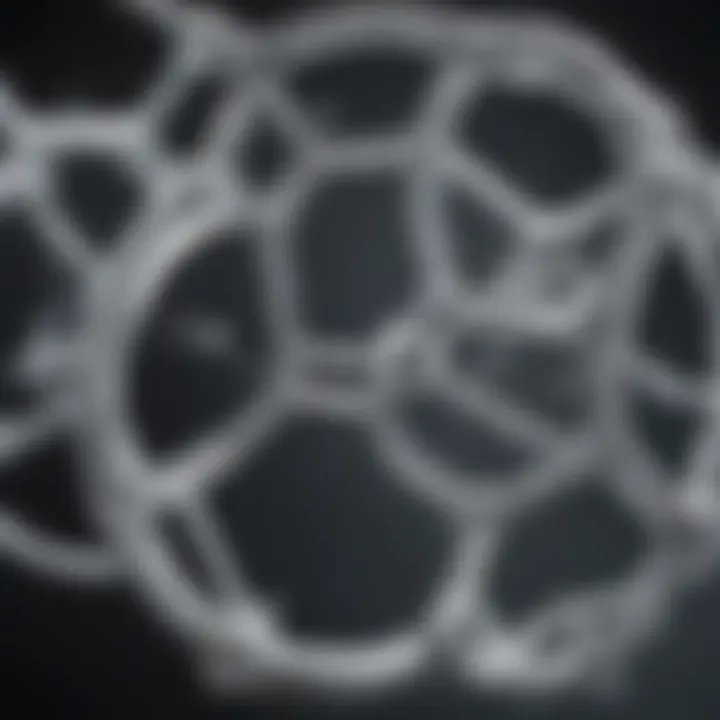
Intro
In the vast field of material science, the choice of materials plays a crucial role in determining the efficacy and performance of a product or application. Two prominent materials in this domain are PVDF (Polyvinylidene Fluoride) and nitrocellulose. These two polymers exhibit strikingly different properties and applications, each bringing unique advantages and considerations to the table. Understanding these differences is essential for students, researchers, and industry professionals to make informed decisions tailored to their specific needs.
Selecting the right material is not as cut-and-dried as it might seem at first glance. Both PVDF and nitrocellulose are valuable in their respective areas, yet their performance varies significantly depending on the context of application. This article endeavors to provide a thorough examination of these materials, highlighting the key characteristics that define each one and how they perform under various conditions. By comparing their properties and applications, we aim to shed light on the optimal scenarios for employing each polymer, guiding our readers through this complex landscape.
Research Background
Overview of the scientific problem addressed
The debate around material selection often springs from the need for functionality and durability in applications ranging from coatings to membranes. PVDF is renowned for its chemical resistance and stability, making it a preferred choice in the chemical processing industry, whereas nitrocellulose boasts superior film-forming capabilities and is often utilized in coatings and lacquers. Understanding the intrinsic properties of these materials is crucial for their successful application. Thus, this comparative study aims to dissect the characteristics and practical applications of both PVDF and nitrocellulose to inform choices that enhance performance and efficiency across various industrial sectors.
Historical context and previous studies
Over the years, significant research has been conducted to better understand polymeric materials. Established in the 1930s, nitrocellulose gained traction for its versatile applications in coatings and inks. Its mechanical properties and processing ease made it a staple in numerous industries. Conversely, PVDF emerged in the 1950s and has undergone various enhancements, evolving into a sophisticated material beloved for its outstanding resistance to harsh chemicals and temperature fluctuations. Prior studies generally focus on specific properties rather than a comprehensive analysis comparing the two, highlighting the necessity of consolidating this knowledge for better practical application.
Both materials have been the subject of numerous investigations. Understanding these backgrounds helps frame the discussion on their relative strengths and weaknesses today. It also sets the stage for an informed dialogue about their future in the ever-evolving landscape of material science.
Prelims to PVDF and Nitrocellulose
In an era where material science is evolving rapidly, understanding the nuances between different types of polymers becomes increasingly crucial. Polyvinylidene Fluoride (PVDF) and nitrocellulose stand out as two significant materials for their diverse applications and distinct properties. PVDF, known for its high chemical resistance and durability, finds its way into various sectors, including electronics and the chemical industry. Meanwhile, nitrocellulose, a traditional yet versatile polymer, plays pivotal roles in coatings, inks, and explosives due to its explosive characteristics and film-forming abilities.
The importance of delving into these materials lies not just in their individual strengths and weaknesses but rather in their respective positions within technological advancements. As we peel back the layers on PVDF and nitrocellulose, it becomes evident how much they influence material selection in real applications. Understanding their distinct properties enhances decision-making processes for engineers, scientists, and entrepreneurs. Furthermore, insights gleaned from a comparative analysis provide clarity when choosing the appropriate material based on specific requirements.
"Knowledge of materials and their properties is fundamental for innovation in engineering, manufacturing, and production."
As the demand for specialized materials increases, comprehending PVDF’s and nitrocellulose’s roles becomes paramount. With advancements in research and development forging paths for new uses and markets, grasping both the historical context and current standings of these polymers will be essential. This section will set the stage for an in-depth exploration into the definitions, intricacies, and evolution of PVDF and nitrocellulose.
Definition of PVDF
PVDF, or Polyvinylidene Fluoride, is a high-performance plastic that has carved a niche for itself due to its outstanding chemical resistance and mechanical strength. It is a thermoplastic fluoropolymer made from the polymerization of vinylidene fluoride. The molecule comprises a sequence of -C-CF2- units, giving rise to its unique properties. PVDF is notable for its ability to withstand harsh environmental conditions, making it particularly valuable in industries like aerospace, chemical processing, and energy production.
Throughout its usage, PVDF showcases remarkable thermal stability along with excellent electrical properties, allowing for its application in various electronic devices. The material also exhibits impressive resistance to ultraviolet (UV) light, ensuring longevity in outdoor installations.
Definition of Nitrocellulose
Nitrocellulose, often referred to as gun cotton, is a highly flammable compound derived from the nitration of cellulose. This nitration process replaces hydroxyl groups in cellulose with nitro groups, yielding a substance that is drastically different from its base material. Nitrocellulose has been a crucial player in various industries due to its film-forming properties and strong adhesive qualities.
Once known primarily for its use in munitions, nitrocellulose has found favor in paints, varnishes, and inks. Its ability to create a smooth, glossy finish makes it a preferred choice in coatings and artistic applications. The compound’s functionality is further enhanced when mixed with plasticizers, creating a more flexible and durable result, broadening its usability even further.
Historical Context and Development
The story of PVDF and nitrocellulose is a testament to the interplay between innovation and practicality in material science. PVDF was developed in the late 20th century, emerging as a sophisticated polymer that provided solutions to rising industry challenges. Its development was rooted in the need for materials that could withstand extreme conditions without degrading. From its inception, PVDF has made significant strides, continually expanding its applications as technology advanced.
On the other hand, nitrocellulose traces its origins back to the 19th century when it was first synthesized by Frederick Augustus Abel. Its explosive properties were aviation a groundbreaking discovery, significantly impacting military applications. Over the years, nitrocellulose has evolved beyond its explosive origins. Research has unveiled its potential in various coatings and adhesive technologies, solidifying its role in both historical and modern contexts.
Chemical Properties Comparison
The chemical properties comparison between PVDF and Nitrocellulose serves as a pivotal component of this analysis, influencing their respective applications and effectiveness in various contexts. Understanding these properties can guide professionals in selecting the most appropriate material for specific projects. For researchers and practitioners, this comparison not only illuminates fundamental differences but also enhances decision-making processes in material selection. Key elements such as molecular structure, chemical stability, and solubility serve as the backbone of this discussion.
Molecular Structure of PVDF
PVDF, known formally as Polyvinylidene Fluoride, has a unique molecular structure characterized by a repeating unit that comprises a carbon backbone attached to fluorine atoms. This configuration results in a semi-crystalline thermoplastic that boasts a plethora of desirable properties. When considering its structure, one sees a strong C-F bond, which is chiefly responsible for PVDF’s chemical inertness and resistance to a wide range of solvents and chemicals. Consequently, its low reactivity renders it ideal for applications in aggressive chemical environments, such as in the manufacture of pipes and fittings for the chemical process industry.
Molecular Structure of Nitrocellulose
Nitrocellulose, in contrast, is a modified cellulose made through the nitration of cellulose fibers. Its molecular architecture is somewhat complex, as it involves the substitution of hydroxyl groups in cellulose with nitrate groups. This substitution enhances certain physical properties but also introduces flammability to the material. The fine balance in its molecular composition leads to a product that can be tailored for specific applications, particularly in coatings and propellants. It’s important to acknowledge, though, that this modification comes with trade-offs in terms of thermal and chemical stability, requiring careful handling and storage to mitigate risks.
Chemical Stability
When assessing chemical stability, PVDF often stands tall due to its outstanding resistance to solvents, strong acids, and bases. This can be a game changer for processes that demand reliability over extended durations. Unlike Nitrocellulose, which can degrade if exposed to harsh chemicals or prolonged heat, PVDF maintains integrity under similar conditions. Here’s where the innate resilience of PVDF showcases its advantage in applications requiring stability and longevity, especially in the chemical and food processing industries.
Solubility and Interaction with Solvents
PVDF is often regarded as having limited solubility in organic solvents, making it a suitable choice in settings where solvent exposure is a concern. Its properties allow for minimal interaction with many solvents, which reduces the risk of leaching and contamination in sensitive applications. Nitrocellulose, however, possesses a different profile; it dissolves readily in organic solvents like ethyl acetate and acetone. This makes Nitrocellulose advantageous in applications such as coatings and adhesives, where uniform distribution and flow of the material are pivotal. However, this same characteristic necessitates caution in its use, given its higher vulnerability to environmental factors.
In summary, understanding the chemical properties of both PVDF and Nitrocellulose reveals critical insights into their respective performance and suitability in various applications. Selecting the right material hinges on thorough knowledge of these facets.
Mechanical Properties Overview
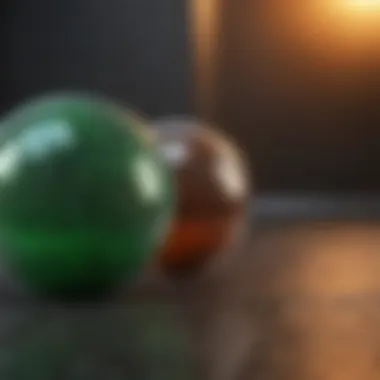
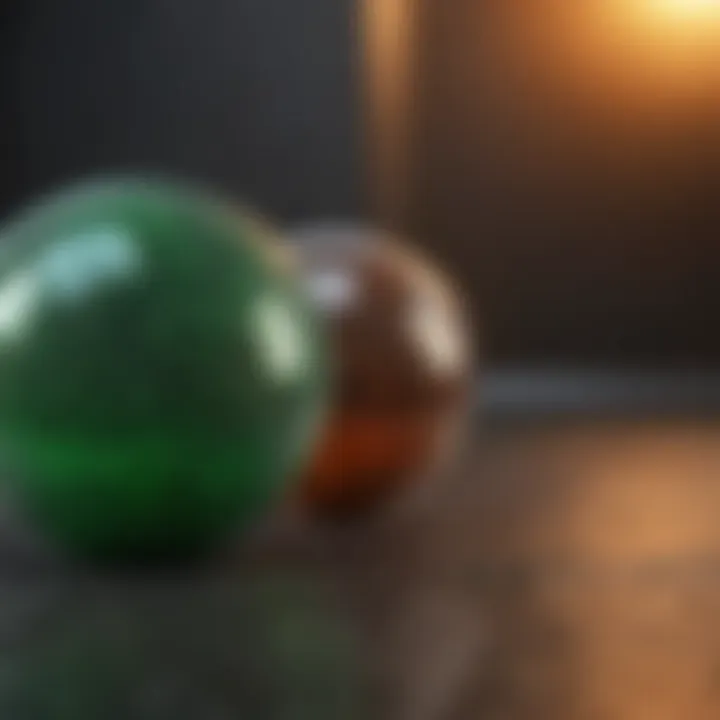
Mechanical properties are vital for understanding how materials respond to forces and stresses in real-world applications. For PVDF and nitrocellulose, these properties determine their suitability for various industrial uses, from coatings to electronic components. By analyzing mechanical properties, one can gain insights into the resilience, flexibility, and durability of each material. This knowledge is critical for engineers and designers who seek reliable and efficient materials for their projects.
Key aspects to consider include:
- Tensile Strength: Indicates how much tension a material can endure before failing.
- Flexural Properties: Relate to how materials bend and their capacity to withstand bending forces without breaking.
- Impact Resistance: Reflects the material’s ability to absorb energy upon sudden loading or shock.
A clear understanding of these mechanical characteristics enables informed decisions that can significantly impact performance and safety in applications. Let’s dive into each detailed analysis starting with tensile strength.
Tensile Strength Analysis
Tensile strength is often regarded as one of the most critical metrics when evaluating materials. It represents the maximum amount of tension that a material can withstand before failure occurs. For PVDF, this property is notable; its tensile strength varies, typically around 35 MPa to 60 MPa, depending on how it's processed. This makes it robust enough for many applications, especially in environments that involve harsh chemicals or fluctuating temperatures.
In contrast, nitrocellulose exhibits a range of tensile strengths as well, but it can generally be lower than that of PVDF. This difference is crucial; while nitrocellulose is often utilized in coatings and inks due to its fast-drying properties, the lower tensile strength can limit its use in applications that demand high endurance against stretching or pulling.
Flexural Properties
Flexural properties shed light on a material's performance under bending loads, which can occur frequently in environmental applications. PVDF showcases impressive flexural strength and rigidity, often making it a go-to choice for structural applications where durability is essential. It can maintain integrity in various temperatures, making it suitable for outdoor installations or other demanding settings.
On the other hand, nitrocellulose tends to be less effective in terms of flexural strength. While it's chosen for applications like lacquers and photographic films, the inherent flexibility leads to a trade-off: it may warp or crack under excessive bending. Thus, understanding these flexural properties allows engineers to select the appropriate material for the job, balancing desired outcomes with potential risks.
Impact Resistance
Impact resistance refers to the capacity of a material to withstand sudden forces or shocks without fracturing. This property is especially important in applications involving transportation or other high-impact environments. PVDF generally exhibits good impact resistance thanks to its ductility and robustness, allowing it to absorb energy without significant deformation. This makes it suitable for components in the chemical and aerospace industries, where reliability is paramount.
Conversely, nitrocellulose can be more brittle under certain conditions. While it performs well in applications requiring light weight and flexibility, its vulnerability to impact means that precautions should be taken to prevent damage in environments prone to sudden stress. Understanding impact resistance is therefore crucial for safety and performance in material selection, guiding decisions based on specific application needs.
"Choosing the right material isn't just about what works best; it's about understanding how it will perform under real-world stresses and strains."
Thermal Properties and Behavior
Understanding the thermal properties and behavior of materials like PVDF and nitrocellulose is crucial for many scientific and industrial applications. These properties influence how these substances will perform under varying temperatures, which can be particularly critical in fields such as electronics, chemical processing, and materials engineering. The importance stems not just from the need for specific performance metrics, but also from safety implications and long-term durability of products made from these materials.
Thermal characteristics provide insights into how these materials behave when subjected to heat. Temperature affects everything from mechanical strength to chemical stability. Therefore, assessing thermal properties helps professionals decide which material best aligns with their project requirements. Let’s delve deeper into the specific thermal properties of each material.
Thermal Conductivity of PVDF
PVDF exhibits a relatively low thermal conductivity when compared to many metals or even some other polymers. This can be advantageous in applications requiring thermal insulation, such as in wiring or components that must mitigate heat transfer. Generally, PVDF's thermal conductivity hovers around 0.19–0.2 W/m·K, with variation depending on specific formulations and additives.
Besides, its low thermal conductivity also signifies that it holds heat somewhat effectively, which can help maintain operational temperatures crucial for sensitive electronic devices. In many cases, engineers prefer PVDF for maintaining temperature stability, particularly in environments where thermal shocks occur frequently.
"The effectiveness of PVDF in insulating properties makes it an ideal choice for applications requiring minimal thermal transfer and maximum reliability."
In applications involving fluids, such as piping and valving where temperature fluctuations can be significant, this property allows for better control over substances being processed, improving efficiency overall.
Thermal Properties of Nitrocellulose
Nitrocellulose, on the other hand, portrays an interesting contrast in its thermal behavior. Its thermal conductivity is higher than PVDF, typically lying around 0.4 W/m·K. This makes it less of an insulator but can be beneficial when a faster heat dissipation is necessary. This quality finds desirable use in coatings and inks where rapid drying is required due to heating effects during production.
It's important to note that nitrocellulose's thermal properties also influence its flammability. While it can withstand a certain temperature range, it is prone to decomposition when exposed to high heat. Thus, safety precautions must always be in place when working with materials containing nitrocellulose in environments where heat is a factor.
Decomposition Temperature
The decomposition temperature is another critical factor differentiating these two materials. For PVDF, the decomposition generally occurs above 250°C, making it a robust choice for high-temperature applications. In contrast, nitrocellulose decomposes at a significantly lower temperature, usually around 170°C to 220°C, depending on its formulation.
This lack of thermal stability can pose risks in processes that exceed this temperature threshold, underscoring the importance of careful handling and application selection. Knowing these limits can mean the difference between success and failure in product longevity and safety. In summary, comparing the thermal properties of PVDF and nitrocellulose reveals vital considerations for their respective uses. It is crucial to weigh these factors in context, aligning project needs with material capabilities.
Electrical Properties Analysis
Understanding the electrical properties of materials like PVDF and nitrocellulose is crucial for a variety of applications, especially in fields such as electronics, protective coatings, and advanced manufacturing processes. The efficiency of electrical insulation relies heavily on the dielectric properties of these substances. Analyzing how PVDF and nitrocellulose behave in electrical roles can unveil unique possibilities for innovations, particularly in conductive and insulative materials. This section explores key elements such as dielectric constants and conductivity, crucial for engineers and researchers deciding between material choices for specific applications.
Dielectric Constant of PVDF
Polyvinylidene fluoride (PVDF) has attracted attention due to its significant dielectric properties, with a dielectric constant often reported between 6 and 12 depending on various factors such as temperature and frequency. This specific characteristic allows PVDF to be an effective insulator in electronic devices.
The dielectric constant is a measure of a material's ability to store electrical energy in an electric field. A higher constant typically indicates a material can store more energy, which is invaluable in applications like capacitors.
PVDF's high resistance to breakdown ensures it can be used in high-voltage applications where reliability is non-negotiable. Moreover, its low loss tangent signifies minimal energy dissipation in electric fields, making it ideal for components geared towards efficiency.
- Applications in Electronics: Widely employed in piezoelectric sensors and actuators, PVDF's prominent properties make it a go-to option for engineers looking to expand functionality without compromising on stability.
- Thermal Stability: Even at elevated temperatures, PVDF’s dielectric properties remain largely unaffected, ensuring consistent performance over a range of conditions.
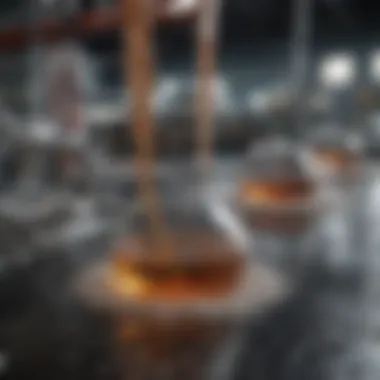
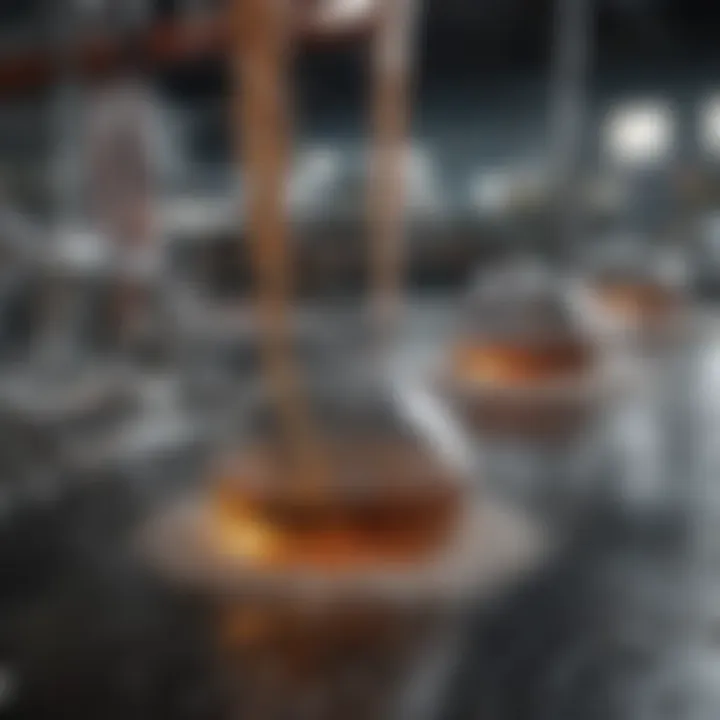
Conductivity in Nitrocellulose
Nitrocellulose, known for its explosive properties, also exhibits intriguing conductive traits, albeit in a different context than PVDF. Depending on the nitrocellulose formulation and the presence of additives, its conductivity can vary widely, which affects its usability in coatings and inks.
In practical terms, when nitrocellulose is blended with other materials, it can enhance the conductive pathways for electrons, enabling functionalities in various applications:
- Conductive Coatings: When combined with conductive fillers, nitrocellulose formulations can provide efficient pathways for electricity, suitable for applications where printability and low processing temperatures are critical.
- Explosive Applications: In its purest form, as a propellant or explosive, nitrocellulose needs controlled conductivity to ensure predictable performance. Too high conductivity could lead to unpredictable behaviors that could compromise safety.
While it isn't the first choice for high-performance electronics, nitrocellulose serves well in certain niches, particularly when performance needs are balanced with considerations of cost and manufacturer safety protocols.
In this analysis, electrical properties are pivotal in understanding how each material fits into specific industrial needs, potentially steering future designs in materials science.
Applications in Various Industries
The application of materials in diverse industries not only showcases their versatility but also underscores their importance in modern technology and everyday life. PVDF and nitrocellulose, each with their distinctive properties, cater to specific needs across multiple sectors. Understanding their applications is crucial for making informed decisions in material selection, whether it be for sustainability, cost, or performance. Let’s explore how these two materials hold their ground in various industries.
Usage of PVDF in the Chemical Industry
Polyvinylidene fluoride (PVDF) finds its footing in the chemical industry primarily due to its chemical resistance and durability. Its inertness makes it ideal for use in environments where corrosive substances are handled. For example, chemical processing plants often employ PVDF in the manufacturing of components such as pipes, tanks, and valves.
Key Benefits of PVDF in the Chemical Sector:
- Chemical Resistance: Has an ability to withstand harsh chemicals like acids and bases.
- Temperature Tolerance: Remains stable at higher temperatures, facilitating safe operation in extreme conditions.
- Low Permeability: Minimizes the risk of leakage, ensuring system integrity.
Another practical application of PVDF is in membranes for filtration processes, particularly in the pharmaceutical industry, where purity standards are of utmost importance. The membranes allow selective passage of fluids while filtering particulates out, which is vital for maintaining product quality.
Role of Nitrocellulose in Coatings and Inks
Nitrocellulose’s prominence in the coatings and inks industry can be attributed to its rapid drying properties and excellent film-forming abilities. This material is a prized ingredient in high-performance coatings, providing a smooth finish and high gloss. It's also mixed with various pigments to formulate inks that adhere well to a variety of surfaces, including plastics and metals.
Features of Nitrocellulose in this Domain:
- Fast Drying Time: Increases efficiency in production lines and application processes.
- Versatile Use: Can be incorporated into different formulations for both artistic and industrial applications.
- High Gloss Finish: Offers a visually appealing aesthetic that enhances product appearance.
Its usage spans from automotive finishes to wood coatings, illustrating its adaptability. Artists and manufacturers alike rely on nitrocellulose for its ability to produce vibrant, durable products.
Applications in the Electronics Sector
When it comes to electronics, the demand for materials that can provide electrical insulation and durability is ever-growing. PVDF shines in this field due to its high dielectric properties, making it suitable for wires and cables that require minimal electrical loss. It's also utilized in printed circuit boards (PCBs) where heat and chemical stability are pivotal.
Applications of PVDF in Electronics:
- Insulation Material: Protects conductors and components from environmental factors.
- Flexible Circuitry: Facilitates innovative designs that are lightweight and reliable.
- Sensor Components: Used in piezoelectric sensors that convert mechanical energy into electrical signals.
Nitrocellulose, while less common in high-performance electronics, still finds a niche. Certain formulations of nitrocellulose are employed in the production of adhesives and coatings that seal electronic devices against moisture and contaminants.
In summary, the distinct applications of PVDF and nitrocellulose across various industries point to their fundamental roles in innovation, efficiency, and safety. Understanding where these materials excel can significantly affect project outcomes and material selection.
Environmental and Safety Considerations
The importance of environmental and safety considerations in the context of materials such as PVDF and nitrocellulose cannot be overstated. As industries continue to innovate and expand, the impact of materials on the environment and human health emerges as a critical factor in material selection. Recognizing how these substances behave environmentally and understanding their safety protocols will significantly inform decisions in both research and application.
Environmental responsibility revolves around several key elements:
- Biodegradability: The ability of a material to decompose naturally in the environment.
- Toxicity: Assessing the harmfulness of a material to both human health and ecosystems.
- Regulatory Compliance: Ensuring adherence to safety regulations to minimize risk.
When evaluating these factors, a clear understanding helps researchers and professionals align their choices with sustainable practices, mitigating potential risks associated with material use.
Biodegradability of PVDF
PVDF, while known for its excellent mechanical and chemical stability, presents challenges in terms of biodegradability. This polymer is generally considered non-biodegradable. Its resistance to environmental degradation means that, once discarded, it can persist in landfills for years, raising concerns about environmental accumulation.
Moreover, the production of PVDF involves processes that can be energy-intensive and may release harmful substances into the environment if not managed properly. However, some recent advances in material science are exploring bio-based alternatives to enhance the environmental profile of PVDF, though these solutions are still in early stages.
Consequently, while PVDF serves many industrial needs efficiently, its sustainability profile sparks considerable discussion about reducing environmental footprints through recycling and innovation in alternatives.
Safety Regulations for Nitrocellulose Use
When it comes to nitrocellulose, safety considerations take center stage due to its flammability and potential hazards. Nitrocellulose is widely utilized in coatings, inks, and explosives, making it subject to stringent regulatory frameworks to ensure safe handling and usage.
Key regulations revolve around a few critical areas:
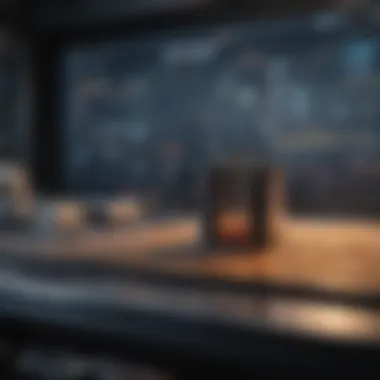
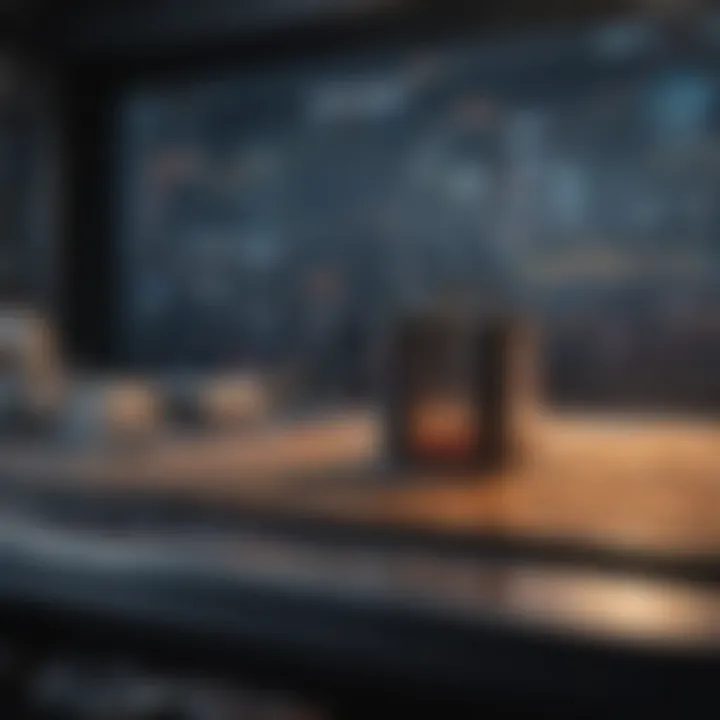
- Storage: Nitrocellulose must be stored away from heat sources and in cool, dry environments to prevent accidental combustion.
- Handling: Guidelines often stress the importance of using personal protective equipment (PPE) when working with nitrocellulose to avoid skin contact and inhalation of fumes.
- Disposal: Special protocols are necessary for disposing of nitrocellulose, considering its hazardous nature, to prevent environmental contamination.
"Nitrocellulose's explosive potential makes safety regulations not just advisable, but essential."
In comprehension of these regulations, industries that utilize nitrocellulose must maintain rigorous protocols to protect workers and the environment alike, often relying on Material Safety Data Sheets (MSDS) and industry best practices to inform their operational standards.
Overall, examining the environmental impact and safety regulations associated with PVDF and nitrocellulose equips stakeholders with the knowledge required to make informed, responsible decisions, prioritizing both innovation and safety.
Cost-effectiveness and Economic Factors
In the realm of materials science, the economic landscape significantly influences decision-making processes. Understanding the cost-effectiveness of materials such as PVDF and nitrocellulose can dictate their adoption in various applications ranging from industrial manufacturing to scientific research. A close examination reveals that several elements underpin this cost-effectiveness, such as production costs, market demand, and the longevity of the materials under practical use. Evaluating these factors can aid researchers and professionals in making informed choices aligned with budgetary constraints while meeting project requirements.
Production Costs of PVDF
PVDF, or Polyvinylidene Fluoride, is appreciated for its rich attributes, but the costs associated with its production warrant attention. The manufacturing process generally involves polymerization techniques which can be quite complex. These intricacies often lead to elevated production costs.
- Raw Materials: The starting materials are designed to be high-purity resins, which increases initial costs. Not all suppliers can offer the required purity, leading to variability in pricing.
- Manufacturing Scale: Large-scale production can help to reduce per-unit costs. However, setting up large production facilities requires substantial investment.
- Processing Techniques: Techniques used to manipulate the polymer into specific forms can be costly and labor-intensive, particularly when specialized machinery is involved.
Despite these costs, the long-term performance of PVDF—resistance to chemicals, temperature fluctuations, and its durability—offers an economic payoff in applications where these properties are essential. Consequently, while the upfront costs may seem daunting, those who measure the total cost of ownership over the lifespan of the product might find PVDF to be a worthwhile investment.
Economic Advantages of Nitrocellulose
Conversely, nitrocellulose presents its own set of economic benefits, mainly attributed to its lower production costs compared to PVDF. With a relatively simpler production process, this material appeals to a broad range of industries.
- Cost-efficient Manufacturing: The process for synthesizing nitrocellulose is generally less intricate, leading to lower raw material costs. Its production often utilizes readily available plant materials, substantially decreasing input expenses.
- Versatile Applications: Nitrocellulose’s compatibility with a variety of solvents and its use in diverse end-products such as paints, inks, and coatings ensures steady demand. This consistent application leads to economies of scale, positively impacting market pricing.
- Short-term utility: For many applications, especially where high-performance attributes are not as critical, nitrocellulose can be ideal due to its cost-effectiveness, often making it the material of choice for manufacturers looking to minimize expenses.
Overall, while PVDF showcases a high-performance profile, nitrocellulose often leads in terms of cost-efficiency in applicable scenarios. Understanding these dynamics can provide a balanced perspective for professionals aiming to make economically sound decisions in material procurement.
Summary of Key Differences
Understanding the differences between PVDF and nitrocellulose is crucial for those making material selections in various fields such as electronics, chemical engineering, and materials science. By pinpointing their distinct characteristics, we not only gain clarity but also ensure informed decisions that amplify efficiencies and minimize risks. Key differences encompass their performance metrics and suitability for specific applications. These elements guide users in choosing the right material that aligns with project requirements, budget constraints, and performance expectations.
Performance Metrics
When we delve into performance metrics, it becomes apparent how these two materials diverge significantly. PVDF typically showcases superior mechanical strength, proving valuable in environments that demand resilience under stress. Its tensile strength can often reach levels above 60 MPa, making it suitable for applications where durability is key. In contrast, nitrocellulose, while more flexible, may lack the same level of strength but excels in applications where rapid drying and composition versatility matter, like inks and coatings.
- Tensile Strength: PVDF holds a prominent edge in this aspect.
- Flexibility: Nitrocellulose can outperform PVDF in terms of ease of formulation and adaptability in coatings.
- Impact Resistance: PVDF generally shines here too, often rated higher across various tests.
It’s essential that when assessing these metrics, one must consider the specific environmental conditions and required durability. Engineers and project managers should keep abreast of these traits to ensure they select a material that meets or exceeds the performance requirements of their project.
Material Suitability for Specific Use Cases
Selecting PVDF or nitrocellulose isn't merely about performance ratings; it’s about understanding their compatibility with specific applications.
PVDF is reliably used in
- Chemical piping systems due to its excellent resistance to harsh chemicals and temperatures.
- Solar energy systems where it serves as an effective binding agent and insulator.
Conversely, nitrocellulose finds its niche in
- Printing inks and coatings, where its ability to dry quickly is appreciated.
- Explosives and propellants due to its energy release characteristics.
Each material presents clear advantages and drawbacks depending on the intended use. An informed choice necessitates not just a look at statistical data but also a deep understanding of the operational context and regulatory standards in play, ensuring that the material aligns with both functionality and compliance.
"Selecting the right material can spell the difference between project success and unexpected challenges."
Future Perspectives
In the ever-evolving landscape of materials science, the future of PVDF and nitrocellulose is poised to be shaped by numerous factors. As industries continue to prioritize eco-friendly production practices, both of these materials present unique opportunities as well as challenges. The relevance of examining future perspectives cannot be overstated; understanding anticipated trends and applications equips researchers and professionals to make informed choices that align with both technological advancements and environmental considerations.
The ongoing demand for high-performance materials in sectors like electronics, automotive, and medical applications underscores the importance of this dialogue. This exploration not only sheds light on potential advancements but also highlights the need for adjustments in manufacturing processes, sustainability, and regulation compliance. Such considerations foster a more profound comprehension of the materials at hand, their limitations, and their potential trajectories.
Trends in Material Development
As the industry shifts focus toward sustainability and performance, we can expect several trends to emerge regarding PVDF and nitrocellulose. For example, scientists are rigorously investigating bio-based alternatives that blend these materials with more sustainable components. This could enhance their biodegradability while keeping the intrinsic performance qualities intact.
- Hybrid materials: Combining PVDF and nitrocellulose with biopolymers can reduce environmental impact while maintaining desirable properties. This method could lead to the development of products that are not only effective but also ecologically responsible.
- Advanced processing methods: Techniques such as 3D printing and electrospinning are becoming increasingly relevant. These methods facilitate more complex geometries and textures, fully utilizing the unique mechanical properties of both materials.
- Customization and specialized properties: The ability to tailor these materials for specific applications is key. For instance, modifying interface characteristics or introducing nanomaterials to enhance electrical or thermal conductivity could open new avenues for innovation.
Innovative Applications on the Horizon
Looking forward, innovative applications for PVDF and nitrocellulose are likely to reshape how industries approach these materials. Their lightweight nature combined with strong performance opens doors in sectors that require energy-efficient yet robust solutions. Future perspectives paint a picture where these materials are integral to groundbreaking technologies.
- Renewable energy: PVDF is increasingly being examined for use in solar panels, particularly in the development of its membranes that can enhance the efficiency of photovoltaic cells. The sustainability angle of using such active materials is compelling, particularly as the globe pivots toward renewable sources.
- Smart textiles: The integration of PVDF in fabric technology could lead to textiles that monitor health conditions or even adapt to environmental changes. Such innovations hint at a future with not just smarter clothing but also a more connected lifestyle.
- Biodegradable coatings: Nitrocellulose could see a resurgence in the form of biodegradable coatings in various consumer products, offering manufacturers an avenue to reduce their ecological footprint. Understanding how to optimize its performance in such applications can consolidate its place in environmentally-conscious manufacturing practices.
"As we move forward, the blend of sustainability with high performance will not just be desirable; it will be essential for the advancement of industries that depend on materials like PVDF and nitrocellulose."
In summary, the future of PVDF and nitrocellulose is concerning critical shifts toward more sustainable practices and innovative applications. By staying informed on these trends, the scientific community, professionals, and students alike can effectively contribute to and benefit from the continued evolution of these significant materials.