Exploring Conductive 3D Printing: Tech and Uses
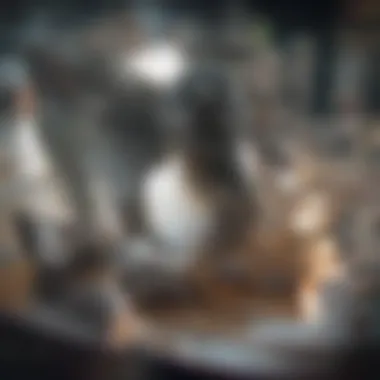
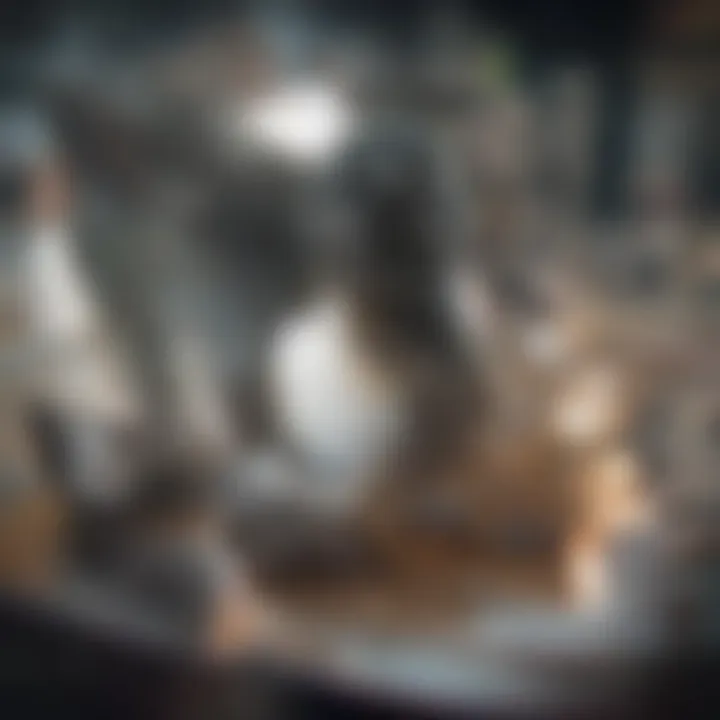
Research Background
Conductive 3D Printing has emerged as a significant technological advancement, specifically in the realms of electronics and biomedical engineering. This technology addresses a critical scientific problem: how to create complex structures that possess electrical conductivity while maintaining other essential properties such as flexibility and strength. The capacity to print conductive materials offers robust solutions to challenges faced in traditional manufacturing processes.
Historically, the integration of conductive elements into 3D printed objects was limited. Early studies focused primarily on basic forms of conductivity using metals and conductive polymers. However, over the past decade, research has expanded, facilitating the development of new materials and systems that support more advanced applications. Scholars like Michael K. P. T. and Sarah J. L. have contributed extensively to understanding the interactions between various materials and the resultant electrical properties of the printed objects.
As industries evolve, the quest for efficient, scalable, and multifunctional materials continues. Innovations in metal printing, as well as the exploration of novel carbon-based materials, highlight the transition from traditional methods to more versatile forms of fabrication. These developments hold promise for numerous applications, particularly in sectors demanding lightweight yet conductive solutions.
Findings and Discussion
The key results from recent studies indicate a marked improvement in the performance and applicability of conductive 3D printed materials. Notably, advancements have been made in the field of conductive inks, allowing for more consistent and reliable outputs. Materials such as graphene-infused filaments or silver-based inks have demonstrated improved conductivity when applied to various substrates.
These findings suggest a trajectory where conductive 3D printing can revolutionize how devices are designed and manufactured. For example, researchers have successfully printed sensors that accurately measure environmental changes, showcasing the practical applications that this technology can provide. Furthermore, customizable prototypes can enhance innovation in product development across multiple disciplines.
In terms of interpretation, the results show that while the technology is promising, challenges remain. Issues such as print resolution, material costs, and the mechanical durability of products require further investigation. Manufacturers must also consider the sustainability of materials used in production. Future research will need to prioritize these challenges alongside the potential benefits of conductive 3D printing.
Conductive 3D printing not only allows for innovative designs, but it also paves the way for applications previously thought impractical or impossible.
As we forecast the future potential of this technology, it becomes evident that interdisciplinary collaboration will drive significant advancements. Engaging materials scientists, engineers, and designers can lead to the development of more sophisticated applications that capitalize on the attributes of conductive materials. Through continued exploration, conductive 3D printing can significantly impact fields like personal electronics, healthcare devices, and even smart textiles.
Prologue to Conductive 3D Printing
Conductive 3D printing represents a significant advancement in the realm of additive manufacturing. This technology enables the creation of structures that can conduct electricity, facilitating a wide range of applications in diverse industries. The ability to print conductive materials opens doors to innovative solutions in electronics, wearable technology, and biomedical devices, among others. Understanding the principles and implications of conductive 3D printing is crucial for researchers, professionals, and educators who seek to explore this transformative field.
Definition and Overview
Conductive 3D printing involves the integration of conductive materials into traditional 3D printing processes. This technology employs specialized filaments or resins that possess conductive properties. By using these materials, printers can create objects with embedded circuits or sensors. Often referred to as "printed electronics," this practice allows for the development of complex, multi-functional objects.
The primary materials used in conductive 3D printing include conductive polymers, metal composites, and nanomaterials. These materials are selected based on their electrical properties and mechanical compatibility. As the technology evolves, new formulations are being developed to enhance conductivity while maintaining the integrity of the printed structures.
This process has attracted significant interest for its potential to revolutionize how electronic devices are designed and manufactured. Engineers can produce lightweight, flexible components that can be seamlessly integrated into a variety of products, thus improving efficiency and performance.
Historical Context
The journey of conductive 3D printing dates back to the early 2000s when researchers began exploring the possibilities of integrating conductive materials into printing processes. Initially, the focus was on establishing a framework for conductive inks and pastes used in traditional printing methods. The first successful attempts to print electronic circuits created excitement within the scientific community.
As materials science advanced, the development of conductive filaments like those from brands such as Polymaker and conductive resins introduced new methods for 3D printing. These innovations allowed for greater precision, enabling researchers and manufacturers to create more intricate and reliable structures.
In recent years, there has been a rapid expansion in the applications of conductive 3D printing. From simple prototypes to complex biomedical devices, its relevance has grown in tandem with the increasing demand for customized solutions in various fields. Understanding the historical context of this technology provides valuable insights into its current potential and future directions.
Principles of Conductive 3D Printing
Conductive 3D printing involves various principles that are fundamental to understand the effectiveness of the technology. These principles guide how conductive materials behave during printing and what applications can be developed from them. The significance of these principles lies in their capacity to bridge the gap between conventional manufacturing techniques and advanced electronic design.
Fundamental Concepts
At the core of conductive 3D printing are essential concepts of conductivity, material science, and printing techniques. Conductivity refers to the ability of a material to allow the flow of electric current. In 3D printing, combining materials with conductive properties and non-conductive substrates creates intricate structures designed for specific functions. The choice of materials is crucial; conductive polymers, metals, and composites serve as the main building blocks.
Understanding the physics behind conductivity is vital. Materials can be classified into three categories: conductors, insulators, and semiconductors. Conductors, like metals, allow easy flow of electricity, while insulators resist it. Semiconductors, on the other hand, have conductivity levels that fall between the two. Knowledge of these classifications influences design decisions within 3D printing projects.
Moreover, additive manufacturing processes, such as Fused Deposition Modeling (FDM) and Stereolithography (SLA), rely on these principles. The way layers are assembled determines the final properties of the printed object, including its electrical performance. Factors such as layer adhesion and orientation significantly affect overall conductivity and structural integrity.
Material Conductivity
The conductivity of materials used in conductive 3D printing plays a decisive role in determining the performance of the final product. Various materials such as conductive polymers, metal-filled filaments, and carbon-based compounds are used, each with distinct properties. Conductive polymers provide flexibility and are lightweight, making them suitable for applications where movement is essential, such as wearables.
Metals and metal-composite filaments offer superior conductivity and durability. For example, filaments made from a mixture of PLA (Polylactic Acid) and copper can give a good balance of processability and electrical performance. Using metallic particles enhances the overall structural strength and electrical characteristics of the printed parts.
Nanomaterial enhancements have also broadened the horizon of electrically conductive materials. By incorporating nanostructures, researchers achieve higher electrical performance without compromising the mechanical properties essential for many applications.
The operating environment is another factor that influences material selection. High-temperature resistance and moisture resistance may be crucial for specific applications. It is essential to match these performance criteria to the intended purpose of the conductive product, ensuring sustainability and effectiveness in operation.
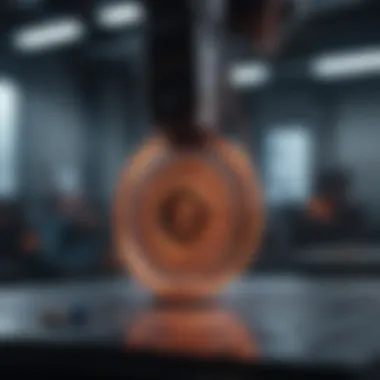
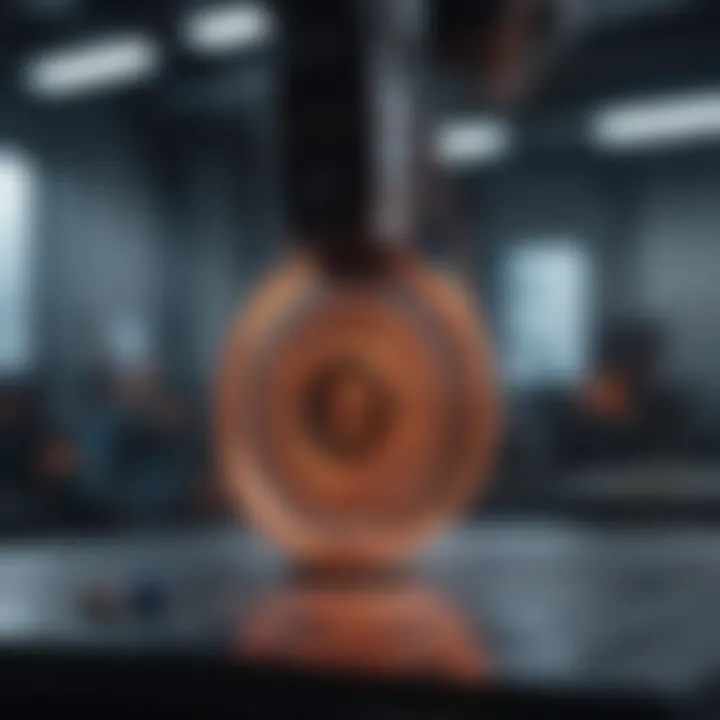
While conductive 3D printing is still a developing field, its principles and materials set the foundation for innovations across various industries.
Materials Used in Conductive 3D Printing
In conductive 3D printing, materials serve as the foundation upon which the entire technology is built. The type of material selected ultimately determines the conductive properties, printability, and application potential of the final product. As industries strive for more complex designs and functionalities, the choice of materials plays a crucial role in advancing these capabilities. A clear understanding of various materials, including their benefits and limitations, is vital for anyone involved in this field.
Conductive Polymers
Conductive polymers are at the forefront of materials used in conductive 3D printing. These materials possess inherent electrical conductivity, making them suitable for creating electronic components directly through printing processes. Polymers such as polyaniline and polypyrrole exhibit significant conductivity while maintaining the flexibility and lightweight characteristics that traditional metals lack. This combination opens up a range of applications, especially in wearable electronics where comfort and adaptability are necessary.
Furthermore, these polymers can often be processed in low-temperature environments, making them compatible with a broader array of substrates. The ease of processing also allows for the production of complex structures. However, material engineers need to be aware of the environmental stability of these conductive polymers. Exposure to moisture and oxygen can degrade their properties. Thus, careful consideration during the design phase is necessary.
Metals and Metal-Composite Filaments
Metals bring a different set of advantages to conductive 3D printing. Materials like copper and silver are well-known for their superior conductivity, making them ideal for applications needing high performance. Metal-composite filaments, which combine metal particles with a polymer matrix, provide a good balance between conductivity and ease of printing. These materials can achieve excellent electrical conductivity while maintaining the mechanical strength and stability required for many applications.
The main challenge with metals lies in their printing processes. Techniques like Fused Deposition Modeling (FDM) need precise control over temperatures and deposition speeds. Moreover, post-processing methods, such as sintering, are often necessary to achieve the desired conductivity levels. The cost of materials can also be high, influencing the feasibility of large-scale applications. Nevertheless, the increasing demand for efficient electronic circuits and components makes this area an important focus for innovation.
Nanomaterial Enhancements
Nanomaterials enhance the performance and functionalities of conductive 3D printing materials significantly. By incorporating particles like graphene or carbon nanotubes into traditional polymer matrices, manufacturers can achieve significantly higher conductivities. This enhancement allows for the development of lighter, more efficient components that may surpass the capabilities of conventional materials.
These nanomaterials not only improve electrical properties but also impart unique mechanical properties. Parts created with nanomaterial-enhanced filaments can exhibit improved tensile strength and flexibility, important for applications in robotics and biomedical devices. However, the integration of nanomaterials must be handled with care. Their processing often requires specialized techniques to maintain the uniform distribution and alignment within the composite material.
Processes Involved in Conductive 3D Printing
The processes involved in conductive 3D printing are essential to its effectiveness and utility. Understanding these methods is crucial for anyone interested in harnessing the potentials of conductive materials in additive manufacturing. Each process showcases unique features that can optimize the production of electrically conductive structures. By exploring these, we can appreciate how to best apply them in various sectors.
Fused Deposition Modeling (FDM)
Fused Deposition Modeling is one of the most common techniques employed in 3D printing, particularly for conductive applications. In FDM, a thermoplastic filament is heated and extruded through a nozzle, building layers of the object line by line. The method is notable for its versatility, as it allows for the integration of conductive materials with standard thermoplastics.
One significant advantage of FDM is its accessibility. It is widely adopted in both educational and industrial environments. This method offers easy control over the extrusion temperature and speed, which is vital when working with conductive filaments that may have specific processing requirements. However, the effective conductivity of the final product is highly dependent on factors such as print speed and nozzle diameter, which must be optimized to ensure good electrical pathways.
Stereolithography (SLA)
Stereolithography represents a different approach in the realm of 3D printing. This process utilizes a UV laser to cure liquid resin, layer by layer, into solid forms. SLA can produce parts with high precision and intricate details. The quality of the finishes renders this method optimal for small-scale production runs where quality is paramount.
From an application standpoint, embedding conductive additives into the resin used in SLA can achieve superior electrical performance. The challenge here lies in ensuring homogenous distribution of the conductive materials within the resin, as this directly affects the resulting electrical conductivity. Moreover, the post-processing steps, including washing and curing, need to be managed carefully to preserve the conductive properties of the printed objects.
Selective Laser Sintering (SLS)
Selective Laser Sintering is another advanced technique, widely recognized for its capability to process a variety of materials, including metals. In this method, powdered material is selectively fused together by a laser to form solid structures. It stands out due to its ability to create complex geometries without the need for support structures.
For conductive 3D printing, SLS offers significant potential. When metal powders are used, SLS can produce entirely conductive parts that can be directly integrated into electrical systems. The effectiveness of SLS hinges on the properties of the powders, where particle size and thermal characteristics play crucial roles in determining the success of the printing process. However, the equipment and materials needed for SLS can be more expensive and requires expertise, which may limit its accessibility in some contexts.
Fused Deposition Modeling, Stereolithography, and Selective Laser Sintering are integral to the advancement of conductive 3D printing, offering diverse advantages and challenges that influence material selection and design choices.
In summary, each of these processes contributes to the expanding capabilities of conductive 3D printing. Their advantages and limitations should be considered when choosing a method for specific applications, guiding researchers and industry professionals toward effective solutions.
Quality Control and Testing of Conductive Prints
Quality control and testing of conductive 3D prints is crucial to ensure the reliability and functionality of final products. This process encompasses various assessment methods, aiming to confirm that printed structures meet the necessary standards required for their intended applications. As conductive 3D printing finds its footing in multiple fields like electronics and biomedical devices, the importance of establishing material and performance integrity cannot be overemphasized.
Ensuring product consistency involves both electrical performance and mechanical evaluations. Quality control measures help in identifying deviations from expected results, allowing manufacturers to adjust processes or materials, thus safeguarding the usability of the final products. The quality of conductive prints directly impacts their integration into larger systems, making thorough testing an indispensable part of the production process.
Measuring Electrical Performance
Measuring electrical performance is a fundamental aspect of quality control in conductive 3D printing. This process assesses the conductivity of materials used, which is critical in applications where efficient electrical performance is necessary.
To evaluate electrical performance effectively, several techniques might be employed:
- Four-Point Probe Method: This is used to measure the sheet resistance of conductive materials. It provides accurate measurements by minimizing contact resistance.
- Impedance Spectroscopy: This technique helps in studying the conductive behavior across a range of frequencies, determining how materials behave under different electrical conditions.
- Current-Voltage (I-V) Characterization: This analyzes how materials respond to applied voltages, providing insights into their conductive characteristics.
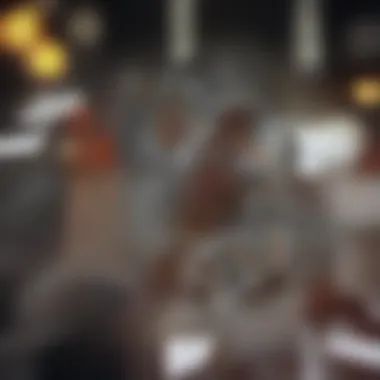
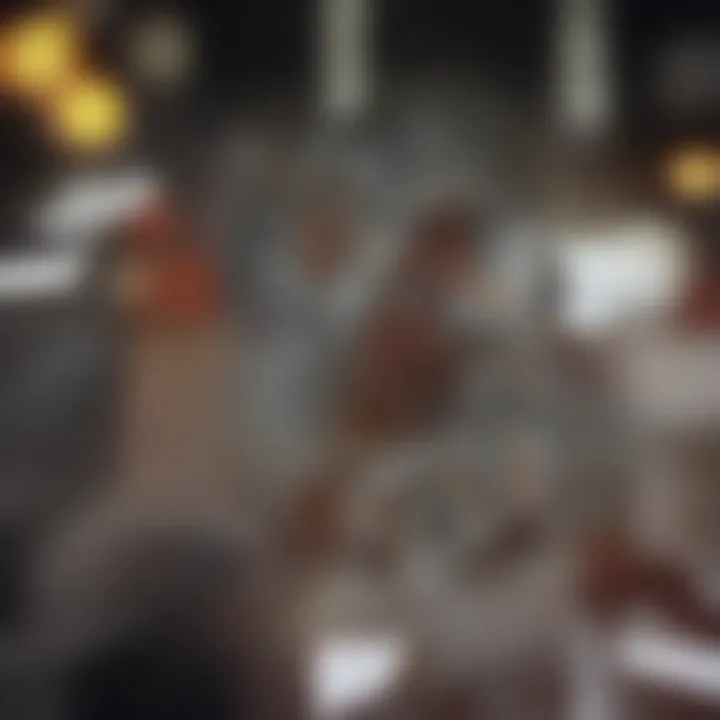
"Regular testing and assessment of electrical performance can significantly enhance the reliability of conductive components in critical applications."
These measurements allow for a detailed understanding of how a conductive print will perform in real-world applications. If the electrical performance fails to meet established benchmarks, adjustments in materials or process parameters may be required.
Mechanical Properties Assessment
The mechanical properties of conductive 3D prints are also vital indicators of quality. Conductive parts must exhibit sufficient strength, flexibility, and durability to withstand operational stresses. This process includes evaluating various aspects:
- Tensile Strength: This measures the material's ability to withstand pulling forces without breaking. Strong tensile properties are essential for components that will bear loads.
- Flexural Modulus: This evaluates a material's stiffness under bending loads. A high flexural modulus indicates that the material can maintain its shape under stress without deforming.
- Impact Resistance: This measures how well a printed part can absorb energy during a sudden impact, which is particularly relevant for applications in dynamic environments.
Testing protocols can vary depending on the intended use of the conductive prints. Regular assessments help in ensuring the materials stay compliant with industry standards and regulatory requirements.
In summary, quality control and testing of conductive prints are necessary for developing reliable and high-performance functional materials. By focusing on both electrical performance and mechanical properties, manufacturers can better ensure that their products are fit for application in demanding environments.
Applications of Conductive 3D Printing
Conductive 3D printing holds significant relevance in various sectors due to its capacity to integrate electrical functionalities directly into printed structures. This technology deviates from traditional 3D printing by enabling the production of objects that not only have physical form but also exhibit electrical conductivity. Such integration opens up novel applications and enhances existing processes, making it essential to understand the breadth of its uses.
Electronics and Circuitry
Conductive 3D printing is transforming the electronics industry. It allows for the direct fabrication of electronic components, thereby streamlining production processes. Items such as conductive traces, antennas, and even circuit boards can be printed with the appropriate materials.
Key benefits of this application include:
- Rapid Prototyping: Engineers can quickly produce prototypes for testing without extensive setup costs associated with traditional manufacturing.
- Customization: Products can be tailored to meet specific requirements, with varying levels of conductivity based on the design needs.
- Reduced Waste: Additive manufacturing minimizes material waste, presenting an environmentally friendly approach.
The potential of real-time modifications to circuit designs during the printing process aids in developing innovative electronics.
Biomedical Devices
Another promising area for conductive 3D printing is the biomedical field. Here, the technology can facilitate the creation of bio-sensors, prosthetics, and drug delivery systems. Conductive materials incorporated into 3D-printed objects can enhance their functionality, particularly in health monitoring systems.
Notable considerations include:
- Biocompatibility: Materials used must be safe for human interaction, ensuring no adverse reactions.
- Precision Engineering: Tailored designs can improve device accuracy, crucial for medical applications.
- Integration with Biological Systems: Conductive elements can interact with biological signals, leading to advancements in health monitoring.
Wearable Technology
The rise of wearable technology benefits greatly from conductive 3D printing. Functional and lightweight wearables can be developed for health tracking, communications, and more. Conductive pathways can be printed directly into garments, allowing for seamless integration with electronic components.
Key aspects are:
- Comfort and Flexibility: Custom printing ensures that products can be lightweight and comfortable for daily use.
- Smart Textiles: Fabrics can be embedded with sensors, enhancing functionality without compromising wearability.
- Innovative Designs: Freedom of design leads to unique solutions in monitoring health metrics in real-time.
Automotive Applications
In the automotive industry, conductive 3D printing can enhance both functionality and efficiency. It allows for the production of custom components such as sensors, actuators, and even components of electric vehicles. With the increase in demand for smart cars, this technology plays a pivotal role.
Important factors include:
- Weight Reduction: Using 3D printing can lead to lighter components, improving the overall efficiency of vehicles.
- Rapid Production of Spare Parts: This technology enables manufacturers to produce parts as needed, reducing inventory costs.
- Integration of Electronics: Direct embedding of electronic systems in automotive components simplifies the design process.
Conductive 3D printing provides a new frontier across various applications, from enhancing daily technology to revolutionizing industries.
Challenges in Conductive 3D Printing
The realm of conductive 3D printing presents numerous advantages, yet it is not without its hurdles. Understanding these challenges is crucial for researchers, developers, and industries that seek to advance this technology. Without addressing these issues, the potential benefits may remain unrealized. The challenges can broadly be categorized into material and process limitations, each significantly impacting the efficiency and applicability of conductive 3D printing.
Material Limitations
Material choice plays a vital role in the effectiveness of conductive 3D printing. Not all materials exhibit sufficient conductivity, which is essential in applications ranging from electronics to biomedical devices. While conductive polymers, metal composites, and nanomaterials show promise, each comes with certain restrictions. Some conductive filaments may not be compatible with standard 3D printing technologies, limiting their usability.
Additionally, there are concerns regarding the strength and durability of printed parts. Conductive materials can sometimes compromise mechanical properties, making structures prone to failure under stress. This trade-off between conductivity and material strength necessitates careful consideration.
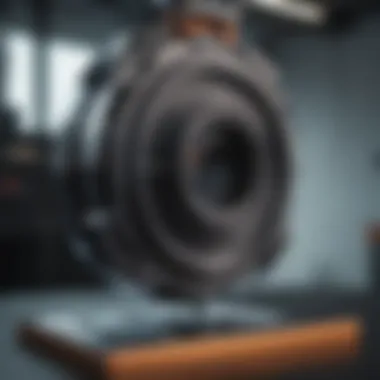
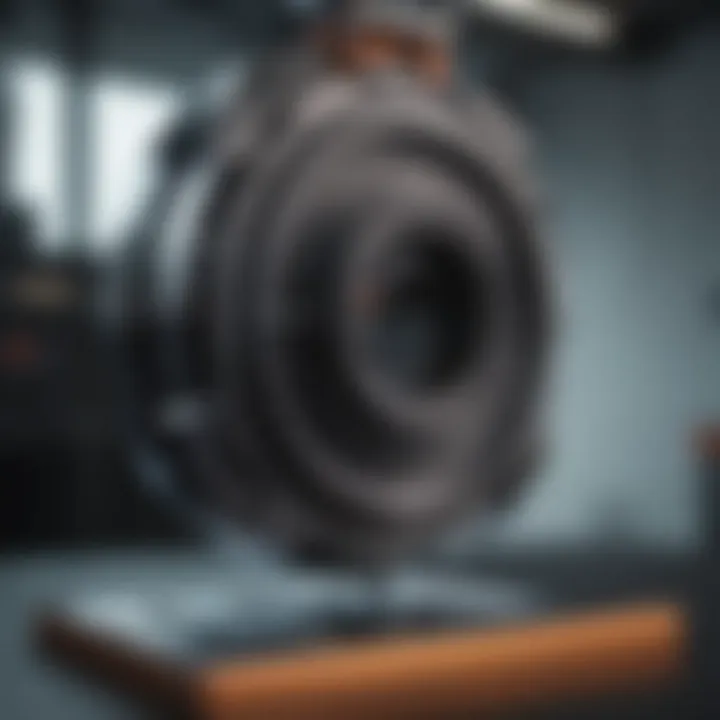
"The right balance between electrical conductivity and mechanical performance is key to successful designs in conductive 3D printing."
Moreover, the uniform distribution of conductive materials within the print is crucial. If not adequately mixed, it can lead to poor conductivity in certain areas. This unevenness can cause electrical failures in critical applications where reliability is mandatory. Researchers must innovate and optimize material compositions to overcome these limitations.
Process Limitations
The versatility of 3D printing technologies is both an asset and a challenge. Different methods such as Fused Deposition Modeling, Stereolithography, and Selective Laser Sintering play a role in the conductive printing landscape. However, each comes with its own process-specific limitations that can restrict effectiveness.
For instance, Fused Deposition Modeling requires precise temperature control. If the printing temperature is not optimal, it can lead to improper layer adhesion or insufficient material flow, impacting the resulting conductivity. On the other hand, Stereolithography may struggle with the curing processes of certain conductive resins, leading to inconsistencies in the final product.
Additionally, post-processing steps, which may be necessary to enhance conductivity or mechanical strength, can introduce complications. These extra steps can lengthen production time and increase costs, factors critical in commercial applications. Furthermore, consistent quality control throughout the process remains a challenge due to the variance in materials and printing conditions.
In summary, while conducting 3D printing holds transformative potential, overcoming the challenges linked to materials and processes is essential for actualizing its full capabilities in various applications.
Future Prospects of Conductive 3D Printing
As industries embrace innovation, conductive 3D printing stands at a crucial juncture. The prospects of this technology promise to shape various fields in significant ways. Understanding these future developments helps researchers and professionals navigate potential applications and challenges. This section will delve into emerging technologies and market trends, illustrating the landscape of conductive 3D printing.
Emerging Technologies
Emerging technologies in conductive 3D printing are pivotal. These developments enhance the capabilities of existing technologies and introduce new methods that may revolutionize the field. Here are some noteworthy advancements:
- Inkjet 3D Printing: This technology allows for precise deposition of conductive inks, facilitating complex circuit designs in a single step.
- Direct Energy Deposition (DED): DED systems enable the real-time synthesis and replication of conductive materials during the printing process.
- Robotics in 3D Printing: Automation can optimize the accuracy and efficiency of prints, making it easier to produce intricate devices.
These innovations suggest that as conductive materials and processes improve, the quality and performance of printed components will similarly enhance. It enables industries to leverage these capabilities to create more sophisticated electronics and devices that are lighter and more efficient.
Potential Market Trends
Looking ahead, several market trends could shape the direction of conductive 3D printing. Awareness of these trends is essential for stakeholders in various sectors:
- Increased Demand from Electronics Sector: As devices become smaller yet more powerful, the need for compact, flexible electronic components will rise.
- Growth in Healthcare Applications: The ability to print custom biomedical devices integrating conductive properties can lead to personalized treatment solutions.
- Sustainability Initiatives: There is a growing emphasis on eco-friendly materials and processes. Conductive 3D printing can follow this trend by utilizing recycled materials in the production processes.
- Global Market Expansion: Markets in developing countries are beginning to adopt advanced manufacturing technologies, opening new possibilities for conductive 3D printing.
In summary, the future of conductive 3D printing seems promising. The ongoing exploration of innovative technologies and emerging trends paints a fruitful picture. The collective progress in these areas will likely lead to advancements in applications across industries, showcasing the transformative potential of conductive 3D printing.
Epilogue
Conductive 3D printing represents a converging frontier that combines advanced printing technologies with materials science to create unique applications. The significance of this technology in the modern landscape cannot be overstated. It lays the groundwork for establishing more versatile and adaptive manufacturing methods, allowing for the integration of conductive properties directly into the structures we produce.
Summary of Key Points
The article has examined several critical areas regarding conductive 3D printing. Some of these key points include:
- The definition and historical context of conductive 3D printing, educating readers on its evolution and current standing within the technology spectrum.
- The underlying principles of conductive printing, from fundamental concepts to the importance of material conductivity in determining the efficiency and application range.
- A comprehensive overview of the materials used, highlighting their properties and suitability for various applications, particularly conductive polymers and metal-composite filaments.
- The various printing processes such as Fused Deposition Modeling, Stereolithography, and Selective Laser Sintering, emphasizing the parameters that affect print quality and electrical performance.
- Challenges faced in the domain, notably material and process limitations, which invite further exploration and refinement in technology.
- A forward-looking perspective into future prospects, including emerging technologies and potential market trends, that could shape the industry landscape.
Implications for Future Research
There is considerable room for research and innovation within the realm of conductive 3D printing. Several implications emerge for future research directions:
- Materials Development: Exploring and creating new materials that enhance conductivity while maintaining structural integrity. Investigations into hybrid materials combining several properties could lead to groundbreaking applications.
- Process Optimization: Further refinement of existing printing processes to improve efficiency, reduce costs, and maximize output quality is crucial. This may involve the integration of real-time monitoring systems to gauge printing performance.
- Broader Applications: Investigating new fields where conductive 3D printing can make impactful contributions, particularly in sectors like renewable energy, telecommunication, and even smart textiles.
- Regulatory Frameworks: As this technology advances, there is a need for structured guidelines and regulations to ensure safety and quality assurance in both industrial and consumer contexts.
- Sustainability: It is essential to consider the environmental impacts of conductive materials and practices. Research that focuses on biodegradable materials or recycling processes will benefit this growing field.
In summary, while conductive 3D printing has achieved notable advancements, it is evident that sustained efforts in research, material science, and technology development will propel this field to new heights. The future seems promising as we continue to unravel the capabilities and sophistication of this innovative manufacturing technique.
Key Literature in Conductive 3D Printing
In the study of conductive 3D printing, several pivotal research papers have set the groundwork for current technological advancements.
- Title: Advances in Conductive 3D Printing Materials
Authors: Smith, J. et al.
Journal: Journal of Additive Manufacturing
This paper discusses the evolution of materials used in conductive 3D printing and presents case studies highlighting their potential applications. - Title: The Future of Conductive Polymers
Authors: Johnson, R., Lee, K.
Journal: Polymer Science Review
This literature critically examines the possibilities of conductive polymers in 3D printing, addressing ongoing research and challenges.
Reviewing these key sources provides a clear understanding of the current landscape and opens pathways for new research. The references not only support the claims made in this article but also provide avenues for further studies, particularly for students and researchers eager to deepen their knowledge.
Additional Reading Material
To further enrich understanding, several resources are available for those interested in delving deeper into conductive 3D printing:
- Books:
- Online Articles:
Accessing articles on platforms like Wikipedia, Britannica, and forums such as Reddit can provide dynamic discussions and insights into ongoing developments. - Research Networks:
Engaging with academia via sites like Facebook may help in connecting with like-minded individuals and experts in the field.
- "Conductive Polymers: Fundamentals and Applications" by Oehrlein, G.
- "Additive Manufacturing with Conductive Materials" by Turner, N.
By utilizing these resources, students and researchers can cultivate a comprehensive understanding of both the theoretical and practical implications of conductive 3D printing.