Copper Molybdenum: Properties and Industrial Uses
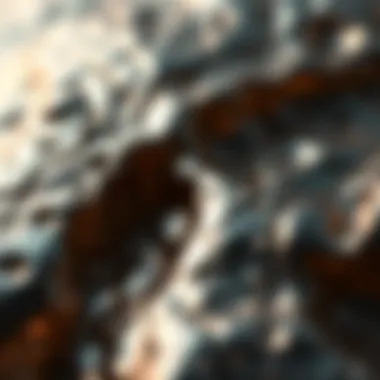
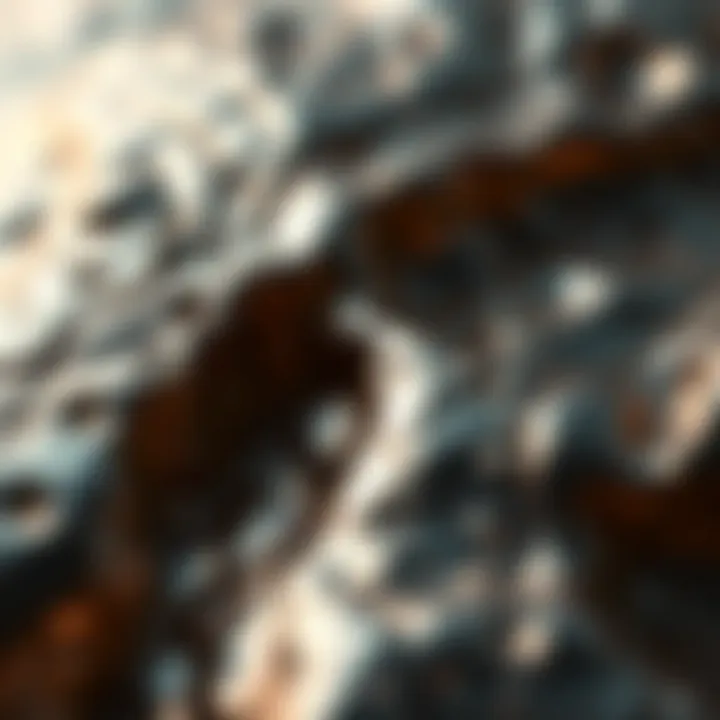
Intro
Copper molybdenum is a prominent alloy that has found its way into a myriad of industrial applications due to its remarkable properties. In today's competitive landscape, understanding the chemistry and mechanics behind this unique combination is crucial for researchers and industry professionals alike. This alloy, which harmoniously combines the excellent conductivity of copper with the impressive strength of molybdenum, presents itself as a solution to various challenges faced in sectors such as electronics and aerospace.
With the pace of technological advancement, the relevance of copper molybdenum becomes even more pronounced. Its advantages not only lie in physical properties but extend to economic viability for manufacturers seeking durability in their materials. Engaging with this topic reveals an intricate web of scientific explorations and innovations that have shaped the use of copper molybdenum.
This section will lay the groundwork for a deeper investigation into the properties and applications of this alloy, while also focusing on the scientific problem it addresses in various sectors. Parents of this alloy have worked tirelessly in previous studies to delineate the significance of its attributes—understanding which can help propel future research and technological applications.
In the subsequent sections, we will delve into the specifics of manufacturing processes, resonating benefits, and future prospects, thus enriching the understanding of copper molybdenum in the scholarly and industrial communities.
Intro to Copper Molybdenum
Copper molybdenum is not just a mere combination of two elements; it symbolizes a leap forward in material science, dramatically influencing multiple industries. Understanding its properties and applications enables researchers and professionals to leverage its capabilities to improve efficiency and performance in various applications. The alloy targets critical areas, showcasing resilience under demanding environments while maintaining vital attributes like electrical and thermal conductivity.
Historical Context
The journey of copper molybdenum began as early as the mid-20th century, a period marked by technological advancements that demanded reliable materials. Post-World War II, the aerospace and electronics industries sought materials capable of enduring extreme conditions. Molybdenum, known for its high melting point and great strength, proved a fitting candidate, while copper's electrical conductivity added to the alloy's allure. Early experiments laid the groundwork for the eventual widespread adoption of copper molybdenum in applications such as integrated circuits and connectors, paving the way for innovation in technology. As these realms grew, so did the significance of copper molybdenum in manufacturing processes. Its importance has evolved, establishing a prominent role in modern material science, with its most fruitful applications often lying at the intersection of innovation and necessity.
Significance in Materials Science
Copper molybdenum plays a dual role in enhancing material performance. This alloy not only brings forth the best features of its components but also presents unique characteristics essential for tackling contemporary engineering challenges. Its importance can be summarized in various key aspects:
- Versatility: The flexibility of copper molybdenum allows it to be tailored for numerous applications, from electronics to aerospace.
- Efficient Thermal Management: With superior thermal conductivity, it helps manage heat in crucial applications, minimizing risks of overheating.
- Electrical Performance: The alloy exhibits excellent electrical properties, making it a preferred choice for components that require efficient conductivity.
- Strength and Durability: Molybdenum contributes significantly to the mechanical strength of the alloy, making it resilient under pressure.
In light of these aspects, the relevance of copper molybdenum emerges clear. Its synthesis is not merely a result of combining two elements; instead, it is about harnessing nature’s gifts to create something that meets the demands of our advancing society.
"Copper molybdenum: where tradition meets innovation, reinforcing our strides in technology and engineering."
Reflecting on the historical groundwork and pressing needs within materials science, it is evident that copper molybdenum continues to pave clear pathways for future advancements. It beckons a deeper exploration into its intrinsic properties and applications, shedding light on how it shapes various sectors today.
Fundamental Properties of Copper
Understanding the fundamental properties of copper is crucial for anyone working with copper molybdenum alloys. Copper serves not only as a key component in the alloy but also brings unique benefits that enhance its overall performance. This metal is known for its excellent electrical and thermal conductivity, making it indispensable in various applications that require efficient heat and current transfer.
Physical Characteristics
Copper is a reddish-orange metal that is typically malleable and ductile. These properties allow it to be shaped into wires and sheets without breaking. One of its standout characteristics is its relatively low density, which contributes to its lightweight nature. This quality is especially favorable in aerospace applications, where minimizing weight is critical.
Furthermore, copper exhibits a good degree of corrosion resistance due to the formation of a protective patina (copper carbonate) when exposed to the atmosphere. This is essential for components in harsh environments, as it prolongs their lifespan and reduces the frequency of replacement. Additionally, copper has a melting point of about 1,984°F (1,085°C), which is relatively high, enabling it to maintain its structural integrity under significant heat without degrading swiftly.
As for its appearance, the lustrous finish of polished copper adds aesthetic value to products, making it a preferred choice for decorative applications. Copper's high reflectivity also comes into play in technologies that utilize light, such as certain types of solar heating equipment.
Chemical Properties
The chemical properties of copper significantly enhance its viability as a material. Copper is known for its excellent electrical conductivity, surpassing many metals, making it a top contender for wiring in electrical appliances and infrastructure. Its ability to conduct electricity is largely due to the metallic bonding in its structure, facilitating the free movement of electrons.
When it comes to reactivity, copper is relatively non-reactive compared to more reactive metals such as magnesium or aluminum. It does not react with water, making it suitable for plumbing applications. However, it can corrode when in contact with certain substances, so understanding its interactions with various chemicals is vital. For instance, when exposed to sulfuric acid, copper can dissolve, which is crucial to consider in chemical processing environments.
The characteristic that sets copper apart is its ability to form various alloys, including brass and bronze, which can be tailored for specific properties. This versatility is beneficial when developing copper molybdenum alloys since the presence of molybdenum can further enhance thermal stability and strength under high temperatures.
"Copper's unique properties not only make it an essential component in many industries, but they also allow for innovative applications, blending performance with functionality."
In summary, the fundamental properties of copper – both physical and chemical – play a vital role in establishing a robust framework for the performance of copper molybdenum alloys. As industries continue to evolve, understanding these properties will be pivotal for engineers and researchers alike.
Fundamental Properties of Molybdenum
Understanding the fundamental properties of molybdenum is crucial in grasping the overall effectiveness of copper molybdenum alloy. Molybdenum, a transition metal known for its high melting point and its ability to withstand extreme conditions, plays a pivotal role in enhancing the performance attributes of the alloy. Its contributions range from improving electrical conductivity to bolstering strength and resistance to temperature variations. The combination of copper and molybdenum results in an alloy that stands out in various demanding applications.
Physical Characteristics
The physical characteristics of molybdenum significantly influence its utility in various industries. Notably, its melting point, which is around 2,623 degrees Celsius, is among the highest of metals. This characteristic allows molybdenum to maintain its integrity under intense heat, making it indispensable in sectors like aerospace and energy.
Additionally, molybdenum exhibits a boiling point of 4,639 degrees Celsius, indicating its capacity to withstand extreme thermal conditions without transitioning into a gaseous state. Its density stands at 10.28 grams per cubic centimeter, which gives it weighty presence in any alloy, thus enhancing the overall density properties of copper molybdenum. Molybdenum is also characterized by its ductility and toughness. These traits enable it to be drawn into thin wires or shaped into various configurations without breaking, which is particularly useful in manufacturing detailed components for electronic devices.
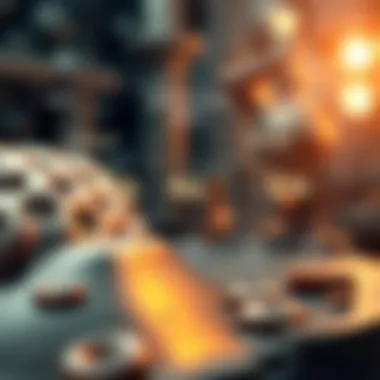
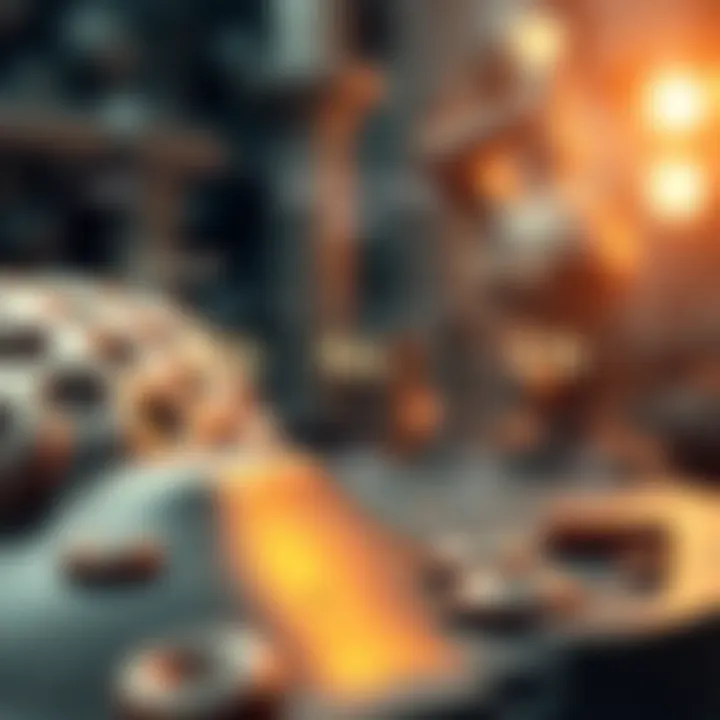
Moreover, molybdenum possesses a metallic luster and manages to maintain a silvery appearance even under oxidizing conditions, adding aesthetic value to the materials incorporating it. The electrical conductivity of molybdenum also plays a key role. Compared to other metals, its ability to conduct electricity is substantial, hence, making it suitable for high-performance electronic applications.
Chemical Properties
The chemical properties of molybdenum further define its effectiveness in copper molybdenum alloys. Molybdenum is recognized for its resistance to corrosion, particularly in high-stress environments that involve oxidizing agents. This resistance ensures that components made from the alloy are more durable and reliable, especially in aircraft or energy facilities where failure can have catastrophic consequences.
Moreover, molybdenum has a relatively low coefficient of thermal expansion. This means it doesn't expand or contract significantly with temperature changes, which is beneficial in applications that face wide temperature ranges. This property allows components to maintain precise fits even when subjected to drastic temperature fluctuations.
In terms of reactivity, molybdenum does not easily form compounds with other elements. Its high resistance to heat and chemical corrosion makes it a stable choice for applications involving reactive materials, further cementing its reputation as a versatile and reliable alloying element.
Molybdenum's unique set of properties makes it indispensable in high-performance environments, pushing the boundaries of what alloys can achieve.
The union of these physical and chemical properties enables molybdenum not only to enhance the functionality of copper but also to create a composite material that meets the rigorous demands of modern technology. By fully understanding and appreciating the innate characteristics of molybdenum, professionals and researchers can exploit its benefits, thereby advancing the practical applications of copper molybdenum alloys.
Formation of Copper Molybdenum Alloy
The formation of the copper molybdenum alloy represents a significant advancement in material science, blending the strengths of both copper and molybdenum to yield a material that showcases remarkable capabilities. This section explores the nuances of alloy composition and processing techniques, illuminating how these elements come together to create a versatile and high-performance alloy.
Alloy Composition
The composition of copper molybdenum alloy is paramount for its performance across various applications. Typically, the alloy consists of approximately 90% copper and 10% molybdenum, although variations exist. The high copper content affords excellent electrical and thermal conductivities, essential in the electronics industry, while the molybdenum enhances strength and heat resistance.
Focusing on the microstructural characteristics, the alloy achieves a fine dispersion of molybdenum within the copper matrix, which plays a vital role in its mechanical properties. This balance creates a structure that can withstand high thermal and electrical loads, making it suitable for applications that demand durability without compromising conductivity.
Some benefits of precise alloy composition include:
- Enhanced strength-to-weight ratio: Ideal for aerospace applications where weight reduction is essential without sacrificing strength.
- Improved thermal stability: Critical for environments exposed to rapid temperature changes.
- Reduced thermal expansion: This minimizes stress in composite materials, keeping components dimensional stable.
Processing Techniques
The processing techniques used in fabricating copper molybdenum alloys are critical in defining their final properties. Among the most common methods are powder metallurgy and casting.
Powder Metallurgy
Powder metallurgy serves as a cornerstone in the production of copper molybdenum alloys. This technique involves the blending of finely powdered metals, which are then compacted and sintered to form solid components. One key characteristic of powder metallurgy is its ability to achieve precise control over the alloy's composition and microstructure.
The benefits of using powder metallurgy in this context include:
- Tailored properties: This method allows for the customization of mechanical and thermal properties to meet specific application needs.
- Reduced waste: As the metals are processed in powder form, there is less material waste compared to traditional manufacturing methods.
Nevertheless, powder metallurgy also presents challenges. For instance, achieving full density in the final product can sometimes be difficult, and the process can be more time-consuming than other techniques.
Cast Molybdenum Copper
On the other hand, the casting of molybdenum copper involves melting the metals and pouring them into molds, allowing for the ease of forming complex shapes. A notable characteristic of this method is its capability to produce larger parts without compromising structural integrity.
Among the benefits of cast molybdenum copper are:
- Simplicity in fabrication: The casting process is generally straightforward, which can lower costs and production time.
- Versatility in shape: This allows for innovative designs that can address particular engineering challenges.
However, casting does come with its own set of drawbacks. The final product may have microstructural inconsistencies and potential defects, like porosity, which need to be accounted for during the design phase.
Overall, both powder metallurgy and casting are essential for conjoining copper and molybdenum, and each brings unique strengths and weaknesses to the table. Understanding these processes helps to appreciate the value and potential of copper molybdenum alloys in various sectors.
Mechanical Properties of Copper Molybdenum
The mechanical properties of copper molybdenum play a crucial role in determining the usability of this alloy across various applications. Understanding these properties is essential for engineers and material scientists, as they highlight the strengths and limitations of copper molybdenum in practical implementations. This section will elaborate on three significant mechanical properties: tensile strength, thermal conductivity, and electrical conductivity. Each of these properties contributes uniquely to the performance of the alloy.
Tensile Strength
Tensile strength refers to the maximum stress that a material can withstand while being stretched or pulled before breaking. Copper molybdenum boasts a notably high tensile strength, making it an attractive choice for applications where durability and stability are a must. The blend of copper and molybdenum results in an alloy that not only resists deformation under load but also retains its structural integrity even in high-temperature conditions.
The importance of tensile strength in copper molybdenum cannot be understated. In aerospace and engineering contexts, components made of this alloy can withstand high stresses without succumbing to failure. For example, in manufacturing components like turbine blades, high tensile strength ensures they remain operational within the critical environment experienced during flight.
"Utilizing alloys with high tensile strength significantly reduces the risk of catastrophic failure in structural applications."
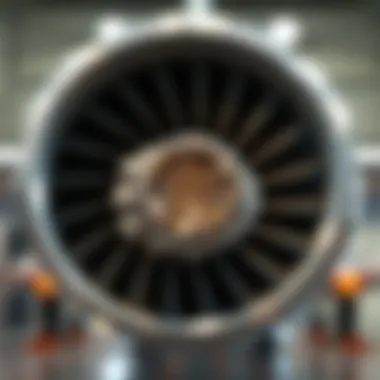
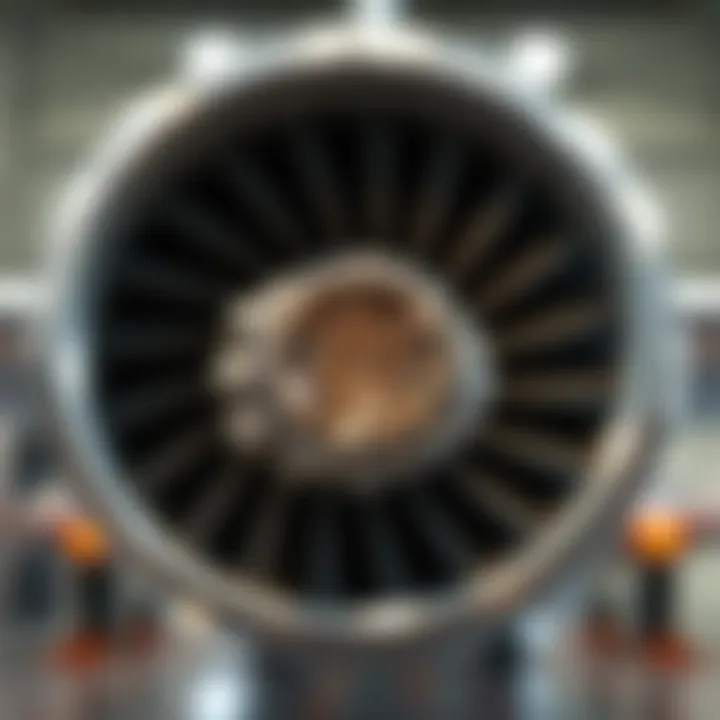
Thermal Conductivity
Another vital aspect of copper molybdenum is its thermal conductivity, meaning how well it can conduct heat. Copper, well-known for its excellent thermal conductivity, imparts a significant advantage when alloyed with molybdenum, which further enhances this property under certain conditions. This characteristic makes copper molybdenum particularly valuable in industries requiring efficient heat dissipation, such as the electronics sector.
Specifically, you will find copper molybdenum used in heat sinks and substrate applications, where effective thermal management is crucial. Ineffective heat dissipation can lead to overheating of components, potentially causing failures. Therefore, the ability of copper molybdenum to conduct heat efficiently can prolong the lifespan of electronic devices and improve their overall performance.
Electrical Conductivity
Electrical conductivity is another critical mechanical property of copper molybdenum, stemming primarily from its copper content. This alloy exhibits impressive electrical conductivity, enabling it to serve in applications where efficient electric current flow is essential. In modern electronics, where the demand for miniaturization and efficiency is increasingly paramount, the incorporation of copper molybdenum provides a practical solution.
Applications in electronics often involve components such as chip substrates and connectors, where the ability to conduct electricity with minimal resistance can make a significant difference in efficiency and performance. Copper molybdenum enhances not just the power efficiency but also contributes to heat management due to its thermal conductivity, creating a synergistic effect that promotes reliability in performance.
In summary, the mechanical properties of copper molybdenum, particularly its tensile strength, thermal conductivity, and electrical conductivity, underline its versatility and usefulness in various industrial contexts. These properties combine to produce an alloy that excels in demanding environments and applications.
Applications of Copper Molybdenum
Copper molybdenum combines essential properties of both metals into a composite that serves a variety of industrial applications. The diverse capabilities of copper molybdenum make it particularly valuable in high-performance sectors. Understanding how this alloy is utilized sheds light on its significance in modern technology.
Electronics Industry
Heat Sinks
Heat sinks are crucial in managing heat produced by electronic components. The unique ability of copper molybdenum to efficiently conduct heat makes it a prime choice for these applications. With its excellent thermal conductivity, it facilitates quick dissipation of heat, which is vital for enhancing device performance and longevity.
One of the key characteristics providing an edge to copper molybdenum heat sinks is their robustness against deformation under varying temperature conditions. Heat sinks made from this material do not just sit statically; they engage actively in maintaining optimal operating temperatures for devices like CPUs and GPUs. This quality highlights the benefits of adopting copper molybdenum in heat sink design over other materials, where performance can suffer under thermal stress.
The unique feature of copper molybdenum heat sinks lies in their lightweight nature without compromising strength. This results in less bulk, making them more desirable for compact electronic designs. However, it is important to note that these heat sinks can be more expensive to manufacture compared to conventional alternatives, which could be a disadvantage for some applications.
Chip Substrates
Chip substrates act as a foundation for microelectronic components, aiding signal transmission and providing structural support. Copper molybdenum offers significant advantages for this role as it has high thermal and electrical conductivity, essential for ensuring reliable operation in sensitive electronic devices.
One key characteristic that sets copper molybdenum chip substrates apart is their low thermal expansion coefficient. This property minimizes the risk of stress and damage that can occur from temperature changes—a beneficial factor in maintaining performance in high-speed applications.
The unique feature of these substrates is how they can sustainably handle the thermal loads generated by densely packed circuits. However, fabrication can sometimes be complex, which could be considered a disadvantage for manufacturers.
Aerospace and Defense
In sectors where reliability is non-negotiable, such as aerospace and defense, copper molybdenum finds important applications. The alloy’s inherent strength and resistance to extreme temperatures and corrosion is exceptional. These characteristics ensure that components can function flawlessly even in demanding environments, making it crucial for safety and efficiency.
Moreover, the alloy's lightweight nature contributes to overall vehicle performance, an aspect highly sought after in aerospace engineering. With weight reduction being a priority, copper molybdenum serves as an ideal candidate for manufacturing parts ranging from engine components to structural elements.
Energy Sector
Renewable Energy Technologies
The advent of renewable energy technologies has opened new avenues for copper molybdenum. With its high thermal conductivity, it plays a critical role in enhancing the efficiency of solar panels. The material’s stability and ability to withstand operational stresses make it a favored option for components within renewable energy systems.
One key characteristic worth noting is its ability to deter oxidation, essential for long-term application in outdoor scenarios, enhancing component longevity. These features make it a popular choice, as system reliability is paramount in energy generation contexts.
The unique feature of using copper molybdenum in renewable energy technologies is its potential for recyclability, aligning with sustainability goals in energy use. However, the initial costs for incorporating this material may restrict its wider adoption in some instances.
Nuclear Applications
In nuclear applications, copper molybdenum is valued for its performance under extreme conditions. The material's resistance to radiation and heat provides a safe and efficient solution for components used in reactors. High levels of thermal and electrical conductivity allow proper management of heat produced within reactors, helping to maintain safety standards.
The key characteristic of copper molybdenum in this field is its suitability for fabricating fuel rod cladding and other critical structural components. The unique feature here is how the alloy can help mitigate risks associated with thermal runaway scenarios, where unchecked heat could lead to catastrophic failures.
However, it is essential to consider that the complexities involved in the effective processing of copper molybdenum could escalate costs, which might limit its application in certain aspects of nuclear technology.
In summary, the applications of copper molybdenum across various industries underline its invaluable contributions—from enhancing thermal management in electronics to ensuring safety in aerospace and nuclear sectors. The alloy’s exceptional thermal and electrical properties make it a versatile and compelling choice in modern applications.
Challenges in Working with Copper Molybdenum
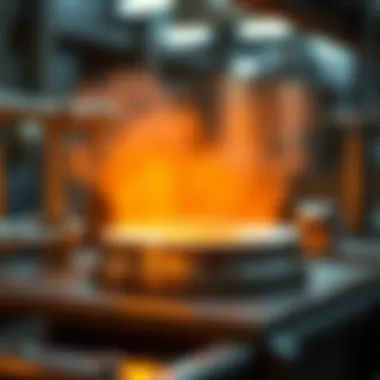
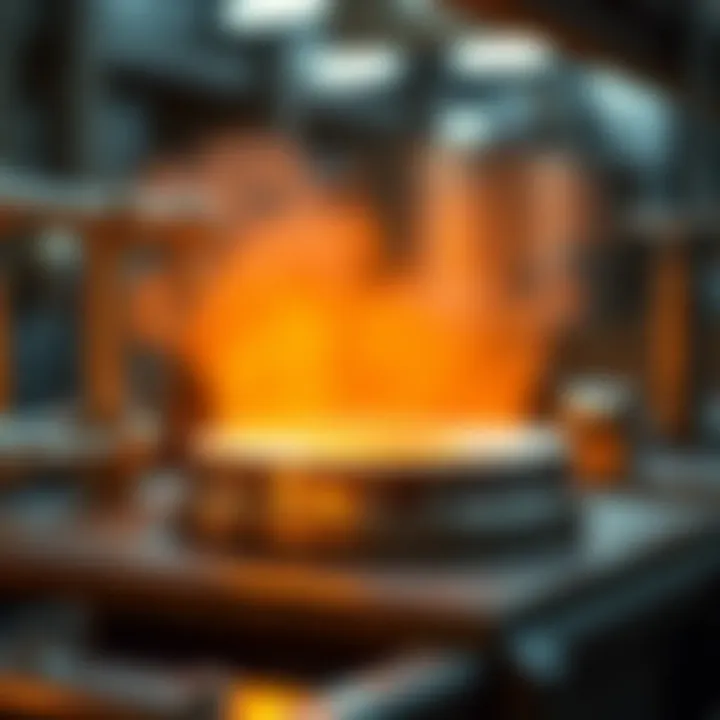
Working with copper molybdenum is not all sunshine and rainbows. While this alloy boasts several essential properties and applications, it comes with its share of challenges that professionals need to grapple with. Understanding these challenges is crucial for optimizing the alloy's performance and ensuring its successful application across various industries. The conversation around these hurdles ultimately highlights the importance of skilled handling and innovative solutions in transforming copper molybdenum into a reliable material for advanced engineering needs.
Alloy Corrosion Resistance
Corrosion resistance is often paramount in many industrial applications. When we talk about copper molybdenum, we encounter a bit of a paradox. On one hand, copper is generally known for its good resistance to corrosion, especially in dry environments. Yet, when alloyed with molybdenum, the dynamics change a bit. Although the presence of molybdenum can enhance certain mechanical properties, it can also make the alloy more susceptible to particular types of corrosion, notably crevice corrosion and pitting, especially in chloride environments.
This sensitivity to corrosion depends on the environment where the alloy is used. For instance:
- In marine environments, where saline conditions prevail, the risk of pitting increases.
- In chemical processing industries, where aggressive media are present, corrosion can turn from an inconvenience to a full-blown disaster, affecting both the lifespan and reliability of components.
Key Considerations:
- Regular inspections become necessary to catch early signs of corrosion.
- Protective coatings or surface treatments might be advisable to enhance the alloy's overall durability.
- The design of components should minimize crevices and allow for adequate drainage to decrease corrosion risk.
"Managing corrosion in copper molybdenum applications requires a nuanced approach, balancing its benefits with proactive protective measures."
Machinability Issues
Another area that raises eyebrows with copper molybdenum is its machinability. Though copper is typically seen as a machinist's best friend due to its softness, when it ’s alloyed with molybdenum, the game changes. The alloy tends to be tougher and harder to work with, which can lead to several machinability challenges. Manufacturers often find themselves at a crossroads when deciding on cutting tools and machining parameters, as using the wrong settings can cause both tool wear and subpar finishes.
A few key machinability issues to highlight include:
- Tool Wear: Machining copper molybdenum can lead to accelerated wear on cutting tools. This happens mainly because of the alloy’s hardness and toughness.
- Heat Generation: The alloy may generate significant heat during machining, which can impact dimensional accuracy. Efficient cooling techniques need to be implemented to manage this heat.
- Surface Finish: Achieving a high-quality surface finish can be tricky. Without proper tools and techniques, components may end up with rough or uneven surfaces, requiring additional processing steps.
Finale on Challenges
These challenges – from corrosion resistance to machinability issues – underscore the necessity for careful planning and execution when working with copper molybdenum. Addressing these obstacles is not merely an option; it is a requirement for achieving the desired performance and longevity of components made from this alloy. Smart engineering solutions and informed choices during processing can turn these challenges into manageable tasks, allowing for efficient utilization of copper molybdenum’s unique properties.
Future Prospects of Copper Molybdenum
Copper molybdenum alloys hold promise for the future, especially as industrial demands evolve. With new technologies emerging at a breakneck pace, these materials are showing their adaptability in various sectors. As industries seek lighter and more efficient materials, copper molybdenum's unique properties might just offer the solutions needed in this rapidly changing landscape. Understanding these prospects is vital as they could define future innovations.
Emerging Technologies
Rapid advancements in technology create a fertile ground for copper molybdenum alloys. Here are some of the areas where they are particularly promising:
- Microelectronics: As devices become smaller and more complex, the demand for materials that can conduct heat and electricity effectively grows. Copper molybdenum's thermal and electrical properties make it an excellent candidate for components like microchips, where performance and reliability are critical.
- Advanced Manufacturing: Techniques like additive manufacturing are gaining traction. The ability to work with copper molybdenum in 3D printing can allow designers more freedom and precision, resulting in components that were previously deemed impossible to manufacture.
- Medical Technologies: The medical field is no stranger to innovation. As procedures demand more precision and durability, copper molybdenum could see uptake in surgical instruments or implants, offering biocompatibility and performance under stress.
One must also consider that the growth of areas such as the Internet of Things (IoT) requires miniaturization and efficiency, both of which copper molybdenum can enhance. It's sure to be an intriguing ride ahead.
"The future belongs to those who believe in the beauty of their dreams." - Eleanor Roosevelt
With each dream, we bring innovation. Copper molybdenum could be at the core of many operations as we push into new realms.
Sustainability Considerations
As environmental concerns continue to rise, the sustainability of materials becomes a central topic. Copper molybdenum, with proper sourcing and recycling processes, offers several advantages:
- Recycling Potential: Both copper and molybdenum are highly recyclable materials. This means that once products reach the end of their lifecycle, they can be repurposed, reducing material waste and conserving resources.
- Energy Efficiency: The high thermal and electrical conductivity of copper molybdenum contributes to energy savings in applications. This is especially important in electric vehicles and renewable energy systems where efficiency translates to lower energy costs.
- Reduced Emissions: With industries moving towards greener alternatives, using copper molybdenum in machinery can help reduce emissions. Improved efficiency and lower material consumption lead to a smaller carbon footprint.
The balance between progress and environmental responsibility is delicate. The ongoing research into the impacts of extraction and processing methods will further bolster copper molybdenum’s standing in sustainable practices. As stakeholders increasingly prioritize sustainability, materials that demonstrate a clear commitment will gain a competitive edge in diverse applications. Understanding these aspects lays the groundwork for future advancements in copper molybdenum technology.
Closure
The investigation into copper molybdenum yields rich insights into an alloy revered for its resilience and multifaceted applications. This alloy isn’t just a mixture of two metals; it embodies a synergy that enhances both thermal and electrical properties, supporting critical advancements across numerous sectors. By synthesizing the distinct characteristics of copper and molybdenum, the alloy emerges as a powerhouse in industries such as electronics, aerospace, and energy.
When thinking about the potential of copper molybdenum, it is crucial to reflect on the following specific elements:
- Durability in Extreme Conditions: The alloy’s excellent corrosion resistance ensures longevity in harsh environments, making it a reliable choice in critical applications where failure can spell disaster.
- Thermal Efficiency: With copper's renowned thermal conductivity, this material optimizes cooling systems in electronics and reduces energy consumption in various applications, aligning with the global push toward efficiency.
- Electrical Conductivity: The combination significantly enhances electrical performance, allowing for advancements in high-tech manufacturing processes.
- Sustainability: As industries strive to meet sustainable development goals, copper molybdenum offers a more eco-friendly alternative compared to other materials due to its recyclability and durability.
"Copper molybdenum stands as a testament to how the right combination of elements can pave the way for innovation and progress in modern technology."
In summary, the benefits of copper molybdenum are many and its application potential is substantial. Understanding its properties and working with this alloy not only paves the path to technological advancement but also aligns with the necessity for sustainable practices in manufacturing.
Summary of Key Points
- Properties: The alloy combines thermal and electrical conductivity, which are critical in electronic applications.
- Industry Application: Utilized across various sectors, including electronics and aerospace, highlighting its versatility.
- Challenges: While its advantages are notable, awareness of machinability issues and corrosion resistance is necessary for optimal usage.
- Future Directions: With emerging technologies and a focus on sustainability, copper molybdenum has the potential for increased applications, particularly in renewable energy solutions.
Relevance to Modern Science
The partnership of copper and molybdenum in alloy formation responds adeptly to the demands of contemporary scientific inquiry and industrial application. In a world where technology is rapidly evolving, the need for materials that exhibit superior performance is critical. Copper molybdenum is at the frontline, not just as a component of devices but as a facilitator of environmental responsibility through its enduring nature.
In the realm of research and application, copper molybdenum’s potential to address the challenges posed by climate change—such as energy efficiency and resource sustainability—makes it particularly pertinent. The material's evolving applications signal how metallurgical innovations can play an essential role in modern science, knitting together traditional metallurgy with cutting-edge advancements, thereby fostering growth in various industrial sectors.