Exploring the Murad Lathe: An In-Depth Analysis
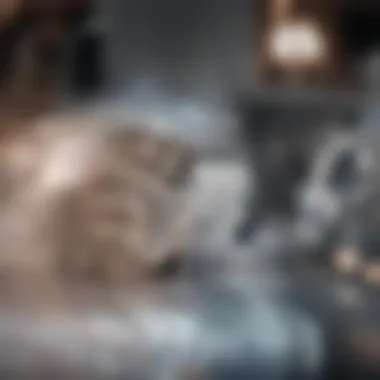
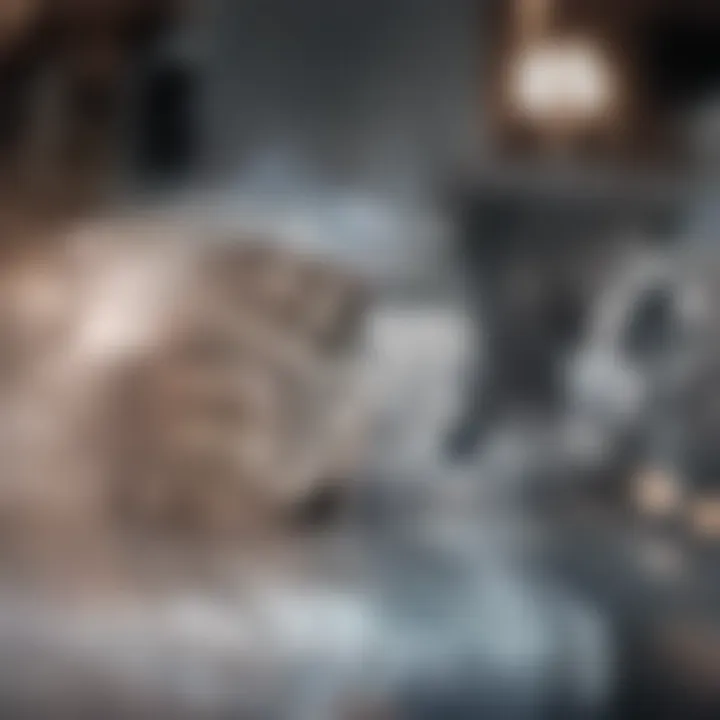
Intro
The Murad lathe represents a pivotal tool in the realm of machining, with a rich history and a wide array of applications. Understanding this tool requires not only a close examination of its design and functionality but also an appreciation of its evolution over time. This insight is essential for students, researchers, and professionals who aim to deepen their knowledge in manufacturing processes and engineering applications.
The subsequent sections of this article will delve into the history of the Murad lathe, dissect its design features, and explore its contemporary relevance within the industry. Furthermore, insights into its operational mechanisms will be presented, along with an evaluation of its advantages and challenges in practical use.
By exploring these facets, readers will gain a comprehensive understanding of not just the Murad lathe itself, but also the broader context in which it operates, offering valuable knowledge for future endeavors in machining.
Prelims to the Murad Lathe
The Murad lathe occupies a vital position in the domain of machining, blending tradition with modern technology. Understanding this tool extends beyond merely recognizing its operational capabilities. It encompasses an appreciation for its historical evolution, structural integrity, and operational efficiency. This lathe is not just a machine; it is an integral part of the manufacturing process that impacts many industries. Whether for academic research, professional use, or personal projects, a deep understanding of the Murad lathe enhances the effectiveness of those who utilize it.
The significance of the Murad lathe lies in its versatility and precision. These qualities provide not just functionality, but also promote innovation within engineering practices. As one section in the comprehensive overview of the Murad lathe, it sets the stage for exploring its rich history and technical attributes, which will be invaluable to users at all levels.
Historical Background
The roots of the Murad lathe can be traced back to the early days of machining when lathes were foundational tools in manufacturing. Originally developed to simplify the turning of materials, the lathe has transformed considerably over the decades. Early versions of this equipment often required immense manual effort, but gradual advancements in technology brought automation into the picture. The Murad lathe emerged as a response to the rising demands for more precise machining and efficiency in production.
Throughout history, various adaptations of lathes have been vital in shaping the manufacturing industry. The evolution of the Murad lathe reflects the ongoing search for improved machining capabilities. From its conception, the lathe has been characterized by improvements in design features, which have allowed for increasingly complex components to be crafted.
Significance in Machining
In the realm of machining, the Murad lathe is celebrated for its ability to produce high precision components. It can handle numerous materials, including metals and plastics, making it invaluable across various sectors like automotive, aerospace, and even medical engineering. This adaptability encourages a broad range of applications, from creating prototypes to mass production runs.
The benefits of utilizing a Murad lathe include enhanced control during cutting processes and the ability to maintain tight tolerances. This combination leads to minimized waste, which is crucial in producing cost-effective solutions—a significant consideration in today’s competitive market.
"The Murad lathe represents a convergence of history, technology, and economic efficiency, underscoring its importance in modern machining practices."
Furthermore, learning about the Murad lathe reaffirms the role it plays in professional development for operators. The mastery of using this tool not only enhances individual skillsets but also contributes positively to overall production efficiency within organizations. By positioning itself at the intersection of historical significance and modern applications, the Murad lathe remains a cornerstone of machining technology.
Design Features of the Murad Lathe
Understanding the design features of the Murad lathe is essential for comprehending its operational capabilities and overall value in machining. The design is a combination of various structural components and operational mechanisms that contribute to the efficiency and effectiveness of the lathe in various applications. Each feature serves a distinct purpose, working together to enhance precision and reliability in production.
Structural Components
Bed
The bed of the Murad lathe is a critical structural component. It serves as the foundation of the lathe, providing stability during operation. The bed is generally made from cast iron, known for its rigidity and capacity to absorb vibrations, which can otherwise impact precision. A significant characteristic of the bed is its length; longer beds can support larger workpieces, which is an advantage in various industrial applications. However, the weight of the bed can be a disadvantage during setup or relocation, as it requires a heavy-duty support system.
Headstock
The headstock is another integral component of the Murad lathe. It houses the spindle and the motor that drives the lathe. A key aspect of the headstock is its ability to accommodate various spindle speeds. This flexibility allows operators to select appropriate speeds for different materials and workpiece sizes. One unique feature of the headstock is the use of gear-driven mechanisms, which enhance torque output. Nevertheless, the complexity of the headstock can lead to maintenance challenges, requiring skilled operators to ensure optimum performance.
Tailstock
The tailstock adds critical support for workpieces, especially during longer machining operations. It is designed to hold tools and can easily be adjusted along the bed. The significant characteristic of the tailstock is its ability to be locked in different positions, which can enhance the versatility of the lathe. A unique advantage of the tailstock is its built-in quill, enabling precise depth adjustments. However, frequent adjustments may be needed, which can slow down production if not managed properly.
Carriage
The carriage is essential for the movement of the cutting tool across the workpiece. It allows both longitudinal and cross movements, which are vital for achieving the desired shape and finish on the material. A prominent characteristic of the carriage is its smooth sliding mechanism, often utilizing high-quality bearings to reduce friction. This design leads to finer finishes and increased accuracy during machining. A potential disadvantage is that inadequate lubrication can lead to increased wear on the carriage components, impacting longevity.
Mechanism of Operation
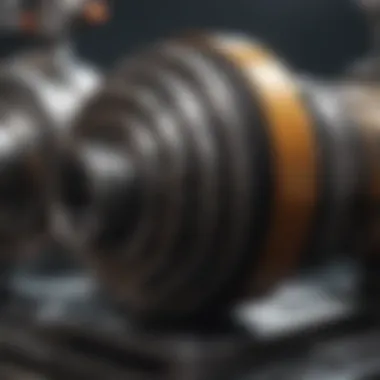
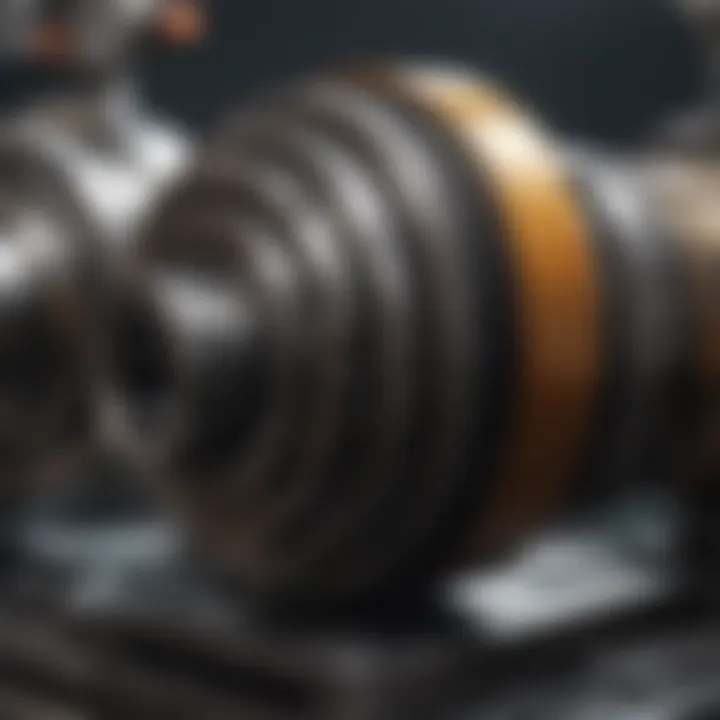
Spindle Functionality
The spindle functionality is crucial for the lathing process. The spindle's primary role is to hold and rotate the workpiece securely. Its design often involves a belt-driven system that permits variable speed control. One key characteristic is its precision bearings, which minimize runout and enhance finish quality. An important aspect is the adaptability of the spindle to accommodate different sizes of workpieces and tooling. However, high-speed operations can generate significant heat, necessitating effective cooling mechanisms.
Cutting Tools and Attachments
The cutting tools used with the Murad lathe significantly influence machining outcomes. These tools can be easily attached or replaced, allowing for a wide range in machining capabilities. A prominent feature of cutting tools is their material composition, commonly made from high-speed steel or carbide for durability. The flexibility in using various tools makes the Murad lathe a popular choice in many workshops, but the cost of replacement tools can add to the operational expenses over time.
Feed Mechanisms
Feed mechanisms are vital for advancing the tool into the workpiece at a controlled rate. This process is crucial for achieving the desired depth and finish. A key characteristic of feed mechanisms is the option for both automatic and manual feeding, depending on the operator's preference. The unique advantage of incorporating automated feed systems is improved efficiency during prolonged operations. Nonetheless, improper calibration can lead to uneven cuts or tool damage, underscoring the need for careful adjustment and monitoring.
Types of Murad Lathes
The classification of lathes, specifically Murad lathes, provides a framework for understanding their diverse functions and applications. Each type has specific characteristics that make it suited for certain tasks. This knowledge is essential for professionals selecting the right equipment for specific machining processes. Below are the main types of Murad Lathes, each with its own unique advantages and operational considerations.
Engine Lathes
Engine lathes are often considered the backbone of traditional machining. They are versatile machines capable of performing a range of operations including turning, facing, and threading. One significant benefit of engine lathes is their ability to handle various materials such as metal, wood, and plastics. Their design typically emphasizes a fixed headstock and a moving carriage, which allows for precision in crafting cylindrical parts.
Operators appreciate this type of lathe for its robustness and ease of use. The simplicity of the mechanism allows for relatively quick setup and adjustments. However, operators must have a solid understanding of manual machining techniques to maximize efficiency. This type of lathe is indispensable in small workshops and educational settings.
CNC Lathes
CNC (Computer Numerical Control) lathes represent a significant technological advancement in machining. Unlike traditional lathes, CNC lathes use computerized controls to automate the machining process. This automation leads to higher efficiency and accuracy in production tasks.
The key advantage of CNC lathes is the ability to produce highly complex geometries with minimal human intervention. This has made them essential in fields requiring precise tolerances, such as aerospace and automotive manufacturing. The programming of CNC lathes often requires specialized knowledge of CAD/CAM software, which can be a limitation for some operators. Nonetheless, the reduction in labor hours and the increase in production capabilities make CNC lathes invaluable for large-scale manufacturing operations.
Turret Lathes
Turret lathes stand out with their unique design that incorporates a rotating turret head, allowing for multiple tools to be mounted simultaneously. This enables quick changes between different operations, which improves productivity. Turret lathes are particularly effective in production environments where repetitive machining is required. The time saved during tool changes can be substantial, making this lathe type ideal for batch production.
Furthermore, turret lathes provide excellent accuracy and can be programmed for automation, similar to CNC lathes. The ability to produce a range of parts without extensive reconfiguration adds to their appeal. However, turret lathes may have a steeper learning curve, particularly for new operators who need to understand the tool-changing mechanisms fully.
The choice between engine, CNC, and turret lathes fundamentally hinges upon the specific needs of the machining tasks at hand, highlighting the importance of understanding the capabilities and limitations of each type.
Applications of the Murad Lathe
The Murad Lathe plays a crucial role in various industries. Its diverse applications highlight its significance in modern machining. The lathe combines precision and versatility, making it suitable for numerous tasks. Understanding these applications helps to appreciate its importance in precision engineering, prototype development, and production manufacturing.
Precision Engineering
Precision engineering demands accuracy and attention to detail. The Murad Lathe stands out in this area due to its ability to produce intricate components. Parts can be made with very tight tolerances, which is essential in applications like aerospace and medical devices.
- High-quality finishing achieved through careful cutting techniques.
- Flexibility to accommodate various materials, such as metals and plastics.
- Capability to adjust tool settings for different projects.
This adaptability enables engineers to meet the precise specifications required for high-stakes projects. In summary, the Murad Lathe supports precision engineering by allowing the creation of high-quality components.
Prototype Development
Creating prototypes requires rapid iteration and design adaptability. The Murad Lathe aids in this process significantly. Engineers can design, test, and refine new products efficiently.
Some advantages include:
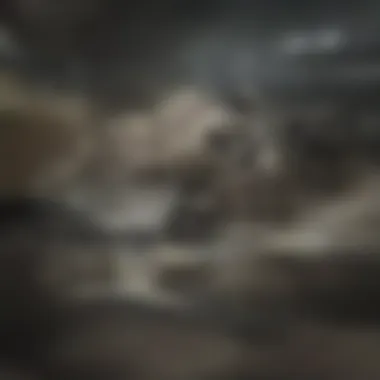
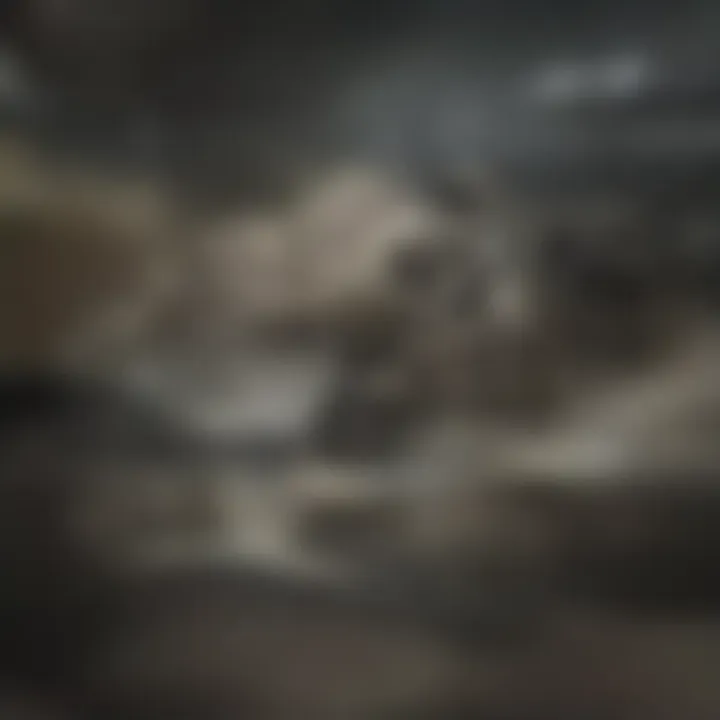
- Fast production rates reduce time to market for new products.
- Customization options allow for adjustments on the fly, enhancing design flexibility.
- Cost-effectiveness when compared to other manufacturing methods.
Prototyping with the Murad Lathe not only streamlines development but also improves overall design cycles. Therefore, it plays a vital role in advancing manufacturing technology.
Production Manufacturing
Finally, the Murad Lathe is invaluable in mass production settings. It enhances efficiency while maintaining consistent quality across products. Its design allows for multiple setups, adapting to various production requirements.
Features that support production include:
- Automation options available for continuous operations.
- Ease of maintenance helps reduce downtime.
- Robust construction ensures durability in high-volume production.
In production manufacturing, the Murad Lathe proves itself by delivering efficiency and consistency.
Manufacturers using this lathe can achieve higher output without compromising quality. Overall, the Murad Lathe is a must-have in any serious machining operation.
Advantages of Using the Murad Lathe
The Murad lathe stands out in the machining industry for several reasons. Its versatility, precision, and efficiency are among the key advantages that make it a favored tool in various applications. Understanding these benefits is essential for anyone involved in manufacturing and machining processes, especially for students and professionals seeking reliable machinery.
Versatility in Operations
One of the most remarkable features of the Murad lathe is its versatility. It can handle a wide range of tasks, including turning, drilling, and threading. Operators have the flexibility to work with different materials, such as metals, plastics, and composites. This adaptability allows users to configure the lathe for specific operations with relative ease. Moreover, the availability of a variety of attachments enhances this adaptability, enabling users to execute complex designs that fit diverse project requirements.
Key advantages include:
- Wide range of materials: Users can work with various types, suitable for different industries.
- Multiple functions: Beyond basic turning, the lathe can perform drilling and threading tasks.
- Adaptable setups: Quick and efficient reconfiguration aids in multitasking.
This versatility not only increases productivity but also reduces the need for multiple machines, saving space and investment on the workshop floor.
High Precision and Accuracy
Precision is crucial in machining, and the Murad lathe excels in this area due to its robust design and advanced components. The lathe's construction minimizes vibrations and ensures a steadier cutting action, leading to superior dimensional accuracy. This capability is vital for producing components that meet stringent specifications commonly found in aerospace, automotive, and medical industries.
Several aspects contribute to its precision:
- Quality components: High-grade materials in the construction improve performance durability.
- Fine-tuning options: Operators can make minute adjustments to achieve the desired measurements.
- Advanced controls: Modern versions may incorporate digital readouts to facilitate monitoring of specifications.
Achieving high precision not only enhances product quality but also reduces wastage and rework, which are critical factors in achieving cost-effective production.
Efficiency in Production
Efficiency in production is another cornerstone of the Murad lathe's utility. The machine operates rapidly while maintaining accuracy, which is vital for meeting tight production schedules. Time-saving features, such as automatic feed mechanisms, lessen the worker's manual involvement, allowing for longer continuous operation.
- Increased output: Streamlined processes contribute to higher production rates.
- Reduced labor costs: Less manual intervention translates to lower labor expenses.
- Optimized workflow: The ability to conduct various tasks on one machine eliminates downtime associated with setting up different machines.
In a competitive market, the efficiency of the Murad lathe can be a significant advantage for manufacturers striving to enhance their productivity without compromising the quality of their output.
The integration of efficiency and precision with versatility truly makes the Murad lathe an invaluable asset in the machining world.
Challenges in Utilizing the Murad Lathe
The Murad lathe, like many sophisticated tools, presents a variety of challenges for machinists and operators. Understanding these obstacles is vital for maximizing the efficiency and effectiveness of this equipment. Addressing the challenge of maintenance, ensuring skilled operation, and recognizing material limitations are crucial components in the optimal use of the Murad lathe.
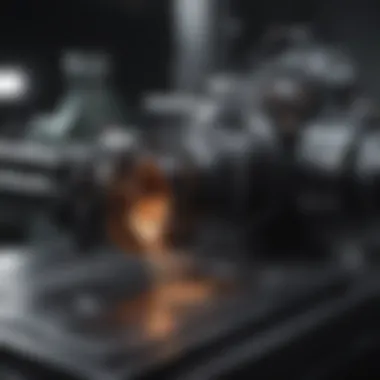
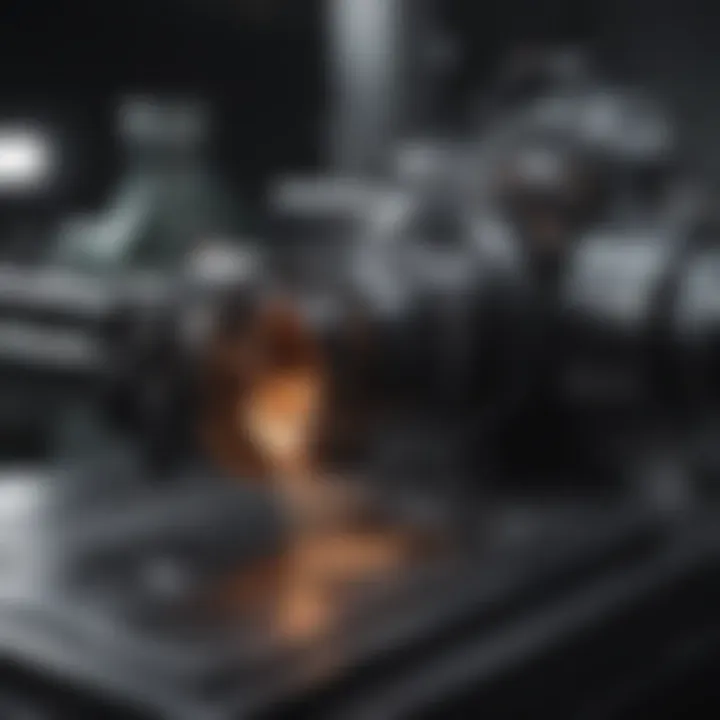
Maintenance and Reliability Issues
Routine maintenance is essential for the longevity and reliability of the Murad lathe. Neglecting maintenance can lead to mechanical failures and operational downtime, which in turn affects productivity and costs. A structured maintenance schedule should include regular checks of critical components such as the spindle, tool holders, and drive systems. Component wear can affect precision, leading in some cases to costly errors. Regular lubrication and cleaning of all moving parts can help prevent excessive wear and maintain a smooth operational flow.
Moreover, users must understand the importance of substitution and repair of worn parts. Sourcing high-quality replacement parts, rather than opting for cheaper alternatives, is often a wise investment to ensure long-term reliability. Failure to do so can cause repetitive issues and hinder the machine's performance.
Skill Requirements for Operators
Operating the Murad lathe requires a specific set of skills and knowledge. Not all technicians can efficiently work with such a complex machine. An experience operator should be well-trained in both manual and CNC functionalities of the lathe. This involves understanding the programming, setup, and troubleshooting procedures that go along with the machine.
Additionally, operators must be adept at reading technical drawings and schematics. Familiarity with cutting speeds, feeds, and tooling selection is necessary for achieving the desired results. Without investment in training, companies risk producing subpar output or damaging the equipment.
Material Limitations
Material limitations play a critical role in the application of the Murad lathe. Not all materials can be machined effectively with this equipment. Hard materials or those highly reactive with the cutting tool might result in premature wear of machine components. Materials such as hardened steel, for instance, may require specialized tooling or slower machining speeds to avoid damaging the lathe.
Moreover, the choice of material affects the overall outcome of the machining process. Operators must select materials that are compatible with the capabilities and limitations of the Murad lathe. Ignoring these factors can lead to inefficiencies and potential hazards in the work process.
Ultimately, identifying and addressing these challenges allows operators and engineers to make the best use of the Murad lathe's capabilities, ensuring not only quality work but also enhancing productivity and safety.
Industry Standards and Regulations
The field of machining, including the utilization of the Murad lathe, operates under strict industry standards and regulations. These guidelines are vital for ensuring safety, enhancing quality, and promoting efficiency in operations. Compliance with these standards is not just a matter of legality; it fosters trust among consumers and promotes sustainability in manufacturing processes.
Safety Protocols
When working with a Murad lathe, safety is paramount. Adhering to established safety protocols minimizes the risk of accidents and injuries. These protocols often include:
- Training for Operators: It is crucial that all operators receive sufficient training, not only in how to operate the lathe but also in understanding potential hazards.
- Personal Protective Equipment (PPE): Operators should wear appropriate gear, such as safety goggles and gloves, to protect against debris and sharp tools.
- Emergency Procedures: Each workplace should have a clear set of emergency procedures to ensure quick and effective responses to accidents.
Implementing and following these safety protocols contributes to a safer work environment and reduces the likelihood of mechanical failures that could lead to accidents. Manufacturers must routinely review and update safety measures based on evolving standards and technology.
Quality Control Measures
Quality control is another essential aspect of utilizing the Murad lathe in machining processes. Effective quality control measures ensure the final product meets desired specifications and maintains consistency. Important elements include:
- Regular Calibration: The lathe should be calibrated regularly to ensure it operates within designated tolerances.
- Inspection Procedures: Parts produced by the lathe should undergo systematic inspection. This may involve visual checks or using precision instruments like micrometers and calipers.
- Documentation of Processes: Keeping detailed records of production processes helps to trace issues back to their source, facilitating continuous improvement.
Incorporating robust quality control measures not only promotes customer satisfaction but also enhances the reputation of manufacturers in a competitive marketplace.
"Industry standards are not just guidelines; they are the backbone of successful machining operations."
Future Trends in Lathe Technology
The evolution of lathe technology is crucial to understanding the future of manufacturing. As industry evolves, so does the necessity for precision tooling solutions like the Murad lathe. The advancement in machining technology ensures that lathes not only maintain their relevance but also enhance productivity and efficiency in varied applications.
Integration of Smart Technology
The integration of smart technology into lathe operations stands at the forefront of modern machining. This trend encompasses a wide array of innovations, namely automation and data analytics. Smart lathes leverage the Internet of Things (IoT) to monitor performance metrics and operational efficiency in real-time. This capability allows for predictive maintenance, minimizing downtime and optimizing production flow.
Operators can experience increased ease of use as smart interfaces often feature intuitive controls. Moreover, machine learning algorithms can identify patterns in cutting performance, helping to fine-tune processes. These advancements increase capability for mass customization without sacrificing speed or precision. Such integration not only aids operators in their daily tasks but cumulates in enhanced overall manufacturing processes.
Sustainability Considerations
Sustainability is another vital aspect shaping the future of lathe technology. The manufacturing sector is increasingly scrutinized for its environmental impact. Murad lathes, adapting to this trend, can implement operations that minimize waste and conserve energy. Techniques such as optimizing tool paths and utilizing energy-efficient motors play a crucial role.
Additionally, the materials used in lathes are evolving. Manufacturers are developing components that reduce the overall carbon footprint. These include recyclable materials and sustainable machining practices such as using biodegradable cutting fluids. Furthermore, a shift towards modular systems allows for easier upgrades, helping to prolong the lifespan of the machines.
Ending
The conclusion serves as a crucial element in any comprehensive discourse about the Murad Lathe. It encapsulates the essence of the prior sections, synthesizing the various facets of the lathe into a cohesive narrative. In this article, we have explored the historical context, design features, diverse types, applications, advantages, challenges, industry regulations, and future trends related to the Murad lathe.