Exploring the Sintering Process in Material Science
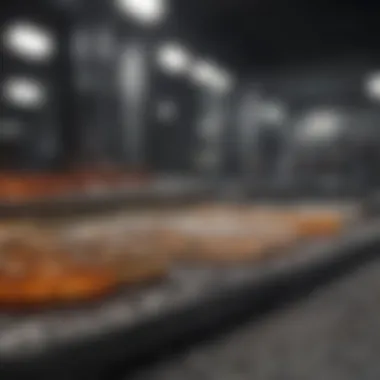

Intro
Sintering is a critical process within material science, acting as the bridge between raw powdered materials and dense, functional objects that serve a multitude of applications. A process that might seem simple at first glance, sintering is layered with complex mechanisms that govern how powders behave when subjected to heat and pressure. Understanding the full scope of this process not only sheds light on the materials themselves but also contributes significantly to innovations across industries ranging from aerospace to electronics.
In recent years, the sintering process has taken on fresh importance as advancements in technology and manufacturing techniques have opened new avenues for exploration. Researchers and practitioners are invested in optimizing sintering to enhance product quality and performance—thus ensuring that materials can meet the growing demands of modern engineering.
The exploration of sintering reveals a rich tapestry formed by various methods and principles that dictate how materials are processed. This article makes a focused attempt to unravel all essential aspects of sintering, leading the reader into both fundamental theories and practical applications. From examining how sintering influences mechanical properties to spotlighting key techniques that drive efficiency, the intention is to provide readers with the insightful information they need to understand this intricate process in a tangible way.
This piece not only marks a pivotal examination of the current state of sintering but also looks ahead. It dives into existing challenges, potential solutions, and the implications these might have on the future of material science. Each section aims to empower students, researchers, educators, and industry professionals with context and clarity that will be valuable in their endeavors.
Looking forward, the narrative will flow through the important subtopics outlined ahead, ensuring that readers emerge with a comprehensive grasp of not only the mechanics of sintering but also its far-reaching significance.
Preamble to the Sintering Process
The sintering process is an often-overlooked yet crucial technique in material science, particularly when it comes to the creation of powdered metals and ceramics. Understanding this process is not only of academic interest but also holds practical significance across various industry sectors. By piecing together the fundamentals of sintering, one can appreciate its strategic role in determining the final quality and performance of materials.
Sintering refers to the method of utilizing heat and sometimes pressure to fuse small particles into a solid mass without melting them entirely. This process has several pivotal implications: it enhances mechanical properties, increases density, and can even improve the surface finish of materials. The significance of studying sintering lies in several key elements:
- Materials Efficiency: The technique allows for the recycling of metal powders, improving resource efficiency and reducing waste.
- Economic Impact: Sintering techniques can lead to lower production costs in comparison to some traditional manufacturing methods.
- Customization: With sintering, it’s possible to engineer specific microstructures in materials, allowing tailored properties for various applications.
As technology advances and the demand for high-performance materials increases, the need to master the intricate details of sintering has never been clearer. The process not only serves as a stepping stone in manufacturing but also presents challenges that require innovative solutions. Understanding these nuances makes it invaluable for students, researchers, and industry professionals alike who aspire to contribute meaningfully to material technology.
Definition and Importance of Sintering
Sintering is defined as the thermal treatment of powdered materials to transform them into a cohesive solid. This transformation occurs below the melting point of the materials involved. It bridges the gap between the powder state and the completed product, serving as a critical step in various material processing workflows.
The importance of sintering can largely be categorized into several frameworks:
- Structural Integrity: Proper sintering leads to improved mechanical properties such as toughness, strength, and wear resistance. These attributes are fundamentally important for many engineering applications.
- Microstructural Control: The sintering process allows for the adjustment of grain sizes and distributions, which directly affect the material's performance and durability. A well-managed sintering process can result in fine grain structures that yield superior characteristics.
- Variety of Applications: From the automotive to the aerospace industry, sintered products find broad applicability. For instance, sintered metal components are often found in machinery where precision and durability are key. Similarly, ceramics produced through sintering play vital roles in electronics, medicine, and numerous other fields.
"Sintering is where the magic happens--it enables raw material potential to be realized, crafting ordinary powders into advanced materials."
Historical Context of Sintering
Understanding the historical context of sintering is pivotal for appreciating its current applications and future potential. Sintering, a process that transforms powdered materials into solid substances through heat and pressure, has a long-standing history that intertwines with the evolution of material science itself. Each phase in its development reflects advances in technology, understanding, and requirements in various industries. It's a bit like tracing the roots of a massive tree, where each branch represents different techniques and discoveries.
Evolution of Sintering Techniques
Sintering techniques have evolved dramatically since their inception. In ancient times, artisans unknowingly practiced rudimentary forms of sintering when they would heat clay or metal powders to create pottery and tools. This not only demonstrates the primitive understanding of material properties but also highlights the essential nature of heat in achieving desired outcomes.
As centuries passed, the methods advanced due to scientific inquiry and the demand for more efficient production techniques. The introduction of the Industrial Revolution marked a significant turning point. New technologies led to the emergence of modern sintering, where more controlled conditions could be maintained. By the early 20th century, the advent of techniques such as oil sintering became prominent, allowing engineers to produce more consistent and high-quality materials.
Furthermore, the development of carbide tools and various ceramic compositions during the mid-20th century pushed the boundaries of sintering. Researchers began incorporating additives and controlling atmospheres to enhance properties of sintered products, paving the way for today's advanced methods.
"The progress in sintering over the years is not merely about techniques but represents mankind's quest for better materials, embodying both innovation and necessity."
Key Milestones in Sintering Development
Several milestones have shaped the course of sintering. They stand as landmarks in the timeline of material science, showcasing an array of innovations:
- 1839 - The first documented use of sintering processes for creating ceramics.
- 1940s - 1950s - The introduction of powder metallurgy processes, establishing a framework for developing metal parts through sintering.
- 1970s - The advent of computer modeling techniques, which allowed for predicting sintering behavior.
- 1990s - The emergence of Spark Plasma Sintering, a modern method gaining traction for its ability to process materials at lower temperatures.
These milestones illustrate not just technical advancements but also the shifts in industry needs and scientific research. Today, sintering is integral to the production of a vast array of materials, from advanced ceramics used in electronics to metal components in aerospace.
Fundamental Principles of Sintering
Understanding the fundamental principles of sintering is crucial for anyone involved in material science. It provides the necessary foundation for exploring how powdered materials can be transformed into solid structures. Sintering isn’t just a process; it's a fascinating interplay of physics and chemistry that leads to significant improvements in material properties. Recognizing how these principles work can help researchers and practitioners refine their methods and enhance product quality, thereby pushing the boundaries of technology.
Basic Mechanisms of Sintering
The basic mechanisms at play during sintering involve complex interactions at a microscopic level. At its core, sintering is about bringing particles together to form a cohesive solid. This occurs primarily through thermal activation. As powders are heated, they undergo three main mechanisms: surface diffusion, volume diffusion, and grain boundary diffusion. These mechanisms happen simultaneously and contribute to changes in microstructure, which ultimately increase the density and strength of the material.
Surface diffusion is when atoms migrate along particle surfaces, smoothing out irregularities. Volume diffusion involves the movement of atoms through the interior of solid particles, while grain boundary diffusion allows atoms to move around the borders of grains. In effect, this collective dance of atoms leads to inter-particle bonding. The finer details of these processes can significantly impact the final properties of the sintered product.
Role of Temperature and Pressure
Temperature and pressure are two critical variables that greatly influence the outcomes of the sintering process. As people often say, "heat is the magic ingredient." Elevated temperatures help facilitate diffusion, creating conditions for particles to bond efficiently. It’s worth mentioning that each material has its own sintering temperature, typically a fraction of its melting point.
"Finding the right temperature is like baking a cake; too hot or too cold will ruin your effort."
Pressure also plays a crucial role. In certain sintering techniques, applying pressure can help mold the particles more effectively. The amount of pressure influences both the compactibility of the powders and the final density of the sintered body. Understanding the intricacies of these parameters essentially helps in tailoring the sintering process to achieve desired properties in materials.
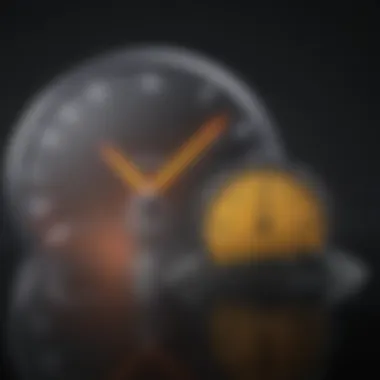
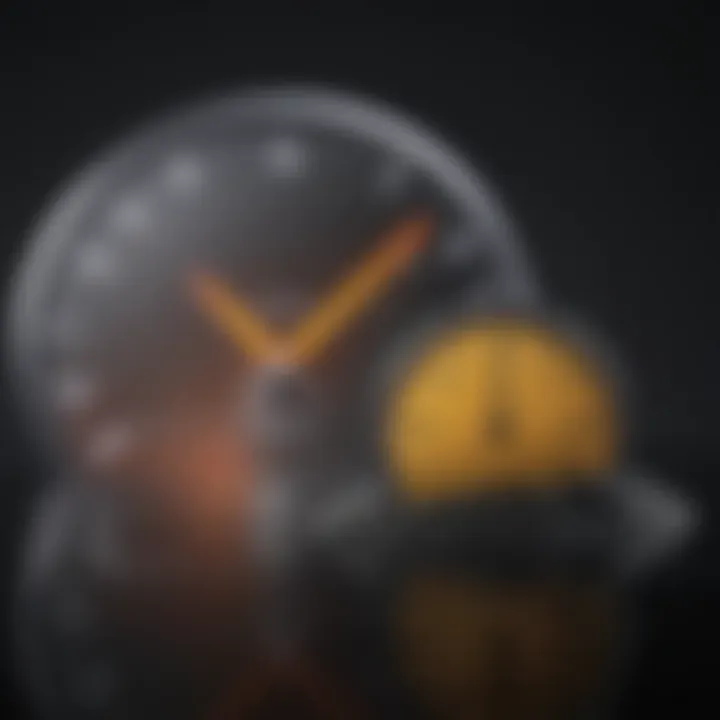
Influence of Particle Size and Distribution
Particle size and distribution are perhaps some of the most overlooked aspects in sintering. These factors significantly affect how well particles interconnect during the process. Generally, smaller particles have a larger surface area, which enhances potential bonding. However, there is a trade-off; too fine a powder can lead to issues of flow and packing. Particle distribution refers to the variation in size within a batch. An optimal mix can ensure that smaller particles fill the gaps between larger ones, providing a well-packed matrix that promotes more effective sintering.
In practice, achieving the right balance can be challenging. Conducting these assessments can save time and resources. A well-considered distribution can lead to improved mechanical properties and performance of the final product, making this a key factor in any sintering endeavor.
Types of Sintering Processes
Understanding the different types of sintering processes is crucial as these methodologies fundamentally affect the properties and performance of the final products. Each sintering technique comes with its unique advantages and challenges, which can tailor the outcomes to specific applications. Knowing how these processes operate can help researchers and industry practitioners make informed decisions regarding material selection and processing routes.
Solid-State Sintering
Solid-state sintering is a widely utilized method where particles bond together without the presence of liquid phase. This process relies heavily on solid-state diffusion, and is particularly effective for materials that require high structural integrity. During solid-state sintering, temperature plays a pivotal role. The process typically begins with the heating of very fine powders, which are then compacted under pressure.
One of the notable advantages of this technique includes the ability to maintain the original shape and dimension of the compact, which is essential for precision components. Furthermore, solid-state sintering tends to produce denser materials with improved mechanical properties. However, it often demands longer processing time and higher temperatures than other types, which can impact energy consumption and costs.
Liquid-Phase Sintering
In liquid-phase sintering, a portion of the material is melted during the heating cycle, allowing it to form a liquid phase that aids in bonding the solid particles. This technique is particularly effective in reducing sintering temperatures while still achieving significant densification. The presence of a liquid phase facilitates the movement of solid particles, helping them to rearrange and pack more efficiently.
This form of sintering can lead to notable improvements in grain growth and phase transformation. Generally, it’s advantageous for producing complex shapes with uniform density. On the flip side, it also comes with risks of excessive grain growth or defects related to the liquid phase, which could compromise mechanical properties.
Flash Sintering
Flash sintering is a relatively modern technique, where an electric field is applied alongside heat. Within an incredibly short time frame, this method can achieve significant densification, often in mere minutes. The phenomenon occurs at relatively low temperatures, which helps in saving energy and minimizing thermal stresses in the materials.
Despite its promise, flash sintering is still under exploration. Understanding the mechanisms at play remains a topic of research. Applications range from advanced ceramics to certain metal matrices. Researchers must carefully consider the parameters, as improper settings could lead to material failures or inconsistencies.
Induction Sintering
Induction sintering leverages electromagnetic induction to heat materials, resulting in vastly quicker processes compared to traditional methods. By directly heating the particles through eddy currents, this technique allows for precise control over the heating rate and distribution. Because it is fast, the risk of oxidation or unwanted reactions during the sintering process is reduced significantly.
A critical advantage of this method is the ability to sinter materials that have high melting points or possess significant thermal conductivity differences. However, one must also consider that the induction process can be expensive due to the equipment involved, and care must be taken to manage cost implications during large-scale applications.
"Choosing the right sintering process is essential, as it can significantly impact the properties of the materials, influencing everything from strength to thermal stability."
In summary, the landscape of sintering methods is rich and nuanced, each with its relevance and application in modern material science. A clear grip on these techniques can facilitate better material designs and innovations, ultimately pushing the boundaries in industries reliant on advanced sintered components.
Sintering Materials and Their Applications
Understanding sintering materials and their applications is vital to grasping how this process transforms raw components into advanced products. Sintering significantly influences optimizations in performance, durability, and cost-effectiveness in the manufacturing world. The combination of particles under heat causes them to bond at points of contact, giving rise to materials that exhibit improved mechanical properties and resistance to wear and corrosion. The implications for industries ranging from aerospace to medical devices are profound, putting a spotlight on the materials themselves.
Metals and Alloys
Metals and alloys are perhaps the most traditional materials used in the sintering process. This category encompasses a wide variety of elements, each contributing unique characteristics to the final product. Notably, materials such as titanium, nickel, and cobalt are frequently employed for their impressive strength-to-weight ratios and resistance to extreme conditions.
Benefits of using metal powders in sintering include:
- Enhanced Mechanical Properties: Operations often produce sintered metals that exhibit remarkable tensile strength and toughness compared to their cast counterparts.
- Complex Shapes: The sintering process allows for intricate designs which can be difficult to achieve by other methods like machining.
- Efficient Material Use: Near-net shaping minimizes waste, making processes financially viable while benefitting the environment by reducing leftover material.
Alloy compositions, especially those tailored for specific applications, can significantly optimize performance. For instance, stainless steel alloys commonly sintered in components for the automotive and construction industries, demonstrate both resilience and resistance to corrosion, making them suitable for varied environments.
Ceramics and Composite Materials
In contrast, ceramics and composite materials present a different narrative within the context of sintering. Ceramics are highly favored for their hardness and thermal stability, critical in applications like electronics, aerospace, and cutting tools. Common options include alumina, zirconia, and silicon nitride, known for their excellent performance under high-temperature conditions.
Some quick benefits from sintering ceramics are:
- High Wear Resistance: Products endure extreme wear and tear, which is essential in fields that require long-lasting materials.
- Electrical Insulation: Ceramics serve as perfect insulators, making them instrumental in electronic applications.
- Tailored Properties: In composite materials, sintering allows for the integration of different types of materials, combining their best features to suit specific application needs.
The fusion of ceramics with metals in composite materials exemplifies innovation in sintering. This hybrid approach can yield products that retain the rigidity of ceramics while gaining the ductility of metals, creating alternatives to conventional materials that can often outshine them in terms of performance.
"Through sintering, each material evolves to meet the eclectic demands of modern engineering. It’s all about striking that delicate balance between functionality and performance."
In summary, the overarching theme in sintering materials and their applications is the adaptability and evolution of materials that arise from this process. Whether it's metals, alloys, or ceramics, each segment uniquely contributes to advancements in technology. As industries quest for enhanced performance and efficiency, continued research on sintering materials will undoubtedly lead to further groundbreaking applications.
Factors Affecting the Sintering Process
The sintering process is intricate, requiring careful consideration of various factors that can significantly alter the quality and properties of the final product. Understanding these factors is not merely an academic exercise; it is essential for achieving desired material characteristics and optimizing production techniques. The nuances involved in sintering can make the difference between a successful application and a complete failure, impacting everything from mechanical strength to thermal conductivity.
Chemical Composition of Materials
The chemical composition of the raw materials used in sintering is foundational to the outcome of the process. Different elements impart unique properties to the final product, influencing everything from its microstructure to its expected durability. For example, sintering metal powders that contain copper often results in different characteristics compared to those made predominantly of iron. This is largely due to variations in melting points and the sintering kinetics of the elemental powders.
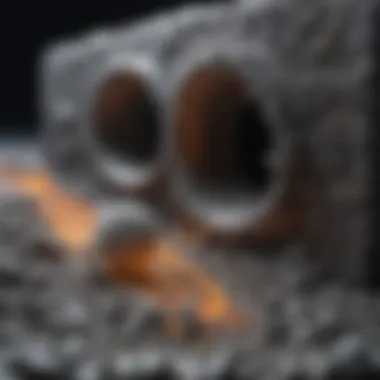
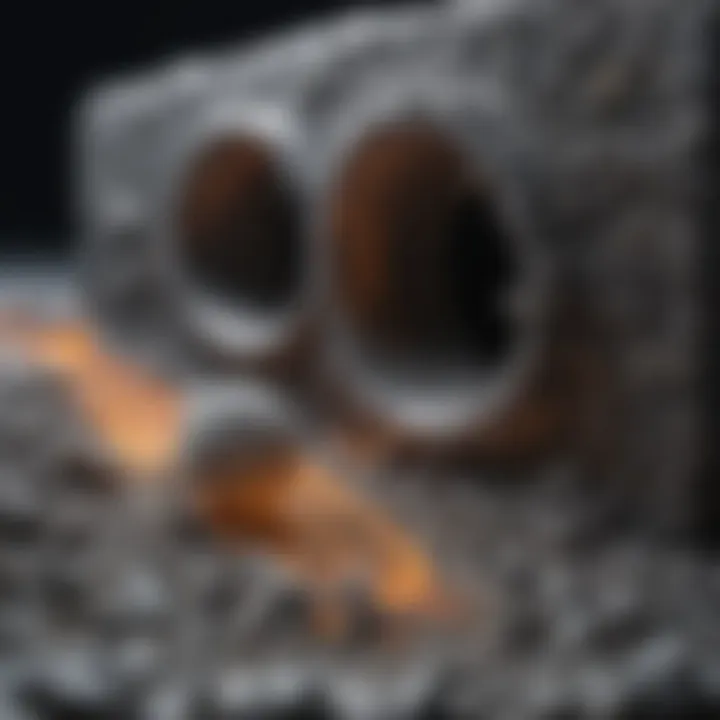
It’s not just the main components that matter; the presence of additives and impurities can dramatically shift outcomes. Additives are sometimes used to improve flowability or accelerate the sintering process itself. However, if impurities infiltrate the mix, they can lead to defects in the sintered material, such as poor bonding or unwanted phases. Thus, meticulous attention to chemical composition is critical, not just for the performance of the final product but also for longevity in applications such as aerospace or biomedical devices.
Atmosphere Control During Sintering
The atmosphere in which sintering occurs is another critical factor. Whether the environment is oxidizing, reducing, or inert can play a decisive role in how materials behave during the sintering process. For instance, a reducing atmosphere may facilitate better densification of metal powders that are prone to oxidation at high temperatures. Conversely, sintering ceramics in an oxidizing atmosphere often leads to undesired phase changes, affecting the material’s properties.
Control systems must be finely tuned to maintain the desired atmosphere throughout the sintering cycle. Variations in gas flow or temperature can lead to inconsistencies that tarnish the final quality of the products. Regular monitoring of the sintering environment can prevent costly mistakes, ensuring that the produced materials dominate in their intended application areas.
"The atmosphere control is like the unshakable foundation of a house; without a solid ground, no structure can withstand the test of time."
Sintering Time and Its Influence
Finally, the duration of the sintering process is a factor that merits careful examination. The length of time powders are subjected to high temperatures directly influences particle bonding and densification. While it might be tempting to think that longer sintering times always yield better results, this is not necessarily the case. Overdoing it can lead to grain growth and reduced mechanical properties, making the material brittle rather than tough and resilient.
An ideal sintering time must strike a balance between achieving maximum densification and maintaining microstructural integrity. This can be tricky; empirical data often guides researchers in determining optimal times for specific material types. Factors such as powder characteristics and intended end-use applications play a role in staking out this balance.
In summary, mastering these factors will enhance the performance and quality of sintered materials, ultimately pushing the boundaries of what is possible in advanced material applications.
Characterization Techniques for Sintered Products
Understanding the intricacies of sintering materials doesn’t end with the methods of production or the materials employed. It delves deeper into what happens post-production. Characterization techniques for sintered products are vital for ensuring that the resulting materials meet specific performance criteria and can be applied effectively in real-world applications. These techniques shed light on the mechanical properties and the microstructure of sintered materials, allowing researchers and manufacturers to crawl through details that directly influence the quality and usability of the final products.
Moreover, the importance of characterization cannot be overstated. By assessing the properties of sintered products, one can determine how well these materials stand up to various stressors when put into use. The relationships between the sintering process and the attributes of the final products also become clearer. Thus, an in-depth understanding of these techniques not only aids in refining the sintering process itself but also in advancing material design and application.
Mechanical Property Assessment
Mechanical property assessment serves as a cornerstone for evaluating sintered products. It involves testing specific qualities such as tensile strength, hardness, and toughness to make sure the materials can withstand certain operational stresses. Each of these properties plays a crucial role across different applications, whether in manufacturing tools, components of machinery, or even in the biomedical field.
Key methods for mechanical property assessment include:
- Tensile Testing: Measures how much stretch an object can handle before breaking. This helps to determine the overall ductility and strength.
- Hardness Testing: Such as Rockwell or Vickers, gauges the resistance of a material against deformation. A harder material usually signifies higher performance in applications.
- Impact Testing: Examines how materials absorb energy during sudden events, necessary for components that undergo dynamic loading.
Important to note, obtaining consistent results from these assessments requires meticulous preparation of the samples, including surface finishing, which can slightly alter material properties. Hence, understanding the intricacies involved in sample preparation cannot be brushed aside.
"Mechanical assessments provide a clear outcome of how a material behaves under stress, guiding engineers in making informed choices in design and application."
Microstructural Analysis
When we talk about microstructural analysis, we’re diving into the very essence of sintered materials. The microstructure provides visual insights into how particles bond and interact on a microscopic level. This analysis reveals grain sizes, pore structures, and phase distributions, which are paramount in determining the performance characteristics of sintered products.
Among the prominent techniques used in microstructural analysis are:
- Scanning Electron Microscopy (SEM): Offers high-resolution images of surfaces, allowing researchers to see the granularity of particles and defects.
- Transmission Electron Microscopy (TEM): Delves deeper, allowing researchers to view the internal structure at the atomic level, which is crucial for understanding the behavior of materials under various conditions.
- X-ray Diffraction (XRD): Used to identify the phases present in the sintered material by analyzing the patterns produced when X-rays hit the crystalline structures.
These techniques not only propel understanding of how materials were engineered but also highlight how future enhancements can be achieved by tweaking sintering conditions. Seeing everything up close opens avenues for innovations in material science that meet the demands of ever-evolving technology.
Advanced Sintering Techniques
The arena of sintering has seen rapid evolution, particularly with the advent of advanced techniques that have expanded the horizons of material processing. These methods not only enhance efficiency but also improve the functionality of the resultant products. In particular, Spark Plasma Sintering and Pressure-Assisted Sintering stand out. They usher in a future where finer control over microstructures and properties of materials is possible, ultimately leading to higher performance materials.
Spark Plasma Sintering
Spark Plasma Sintering (SPS), sometimes referred to simply as pulsed electric current sintering, is about more than just joining particles; it’s a concerted dance of heat and force that transforms powders into solid forms. This technique takes advantage of electric discharges that heat the materials, enabling sintering at lower temperatures and shorter times.
The beauty of SPS lies in its ability to preserve the unique characteristics of materials while also minimizing grain growth, which often hinders performance. It allows for a finer control over the microstructure, resulting in enhanced mechanical properties. Higher densities can be achieved with less energy, making it a potentially eco-friendly option. Researchers across the globe have recognized its potential in both academia and industry, tapping into its capabilities for creating advanced ceramics and composites, thus pushing the boundaries of what’s achievable in materials science.
Some notable benefits of Spark Plasma Sintering include:
- Reduced Processing Time: Because it achieves higher densification rates quickly, manufacturers can roll out products faster, reducing time-to-market.
- Uniform Heat Distribution: The pulsed nature oft the process results in less thermal gradient problems, promoting more homogenous material properties.
- Versatility: Applicable to a wide range of materials from metals to ceramics, SPS offers broad utility.
Pressure-Assisted Sintering
Pressure-Assisted Sintering involves applying external pressure during the sintering phase, contributing to improve density and mechanical properties of the end products. This method often involves techniques such as Hot Isostatic Pressing or Hot Pressing, which apply pressure concurrently with heat to densify the powders.
This approach can catalyze effective bonding between particles, promoting better mechanical integrity and durability. When done correctly, it can produce materials that are significantly stronger and tougher than those processed under conventional sintering conditions. Pressure-Assisted Sintering is gaining traction as a feasible method for producing demanding components especially in aerospace and automotive industries where performance cannot be compromised.
Advantages of this technique include:
- Enhanced Material Properties: Better strength and toughness, crucial for applications that involve high stress and strain.
- Controlled Microstructure: Provides an avenue to manipulate grain size, which plays a critical role in the mechanical performance of materials.
- Efficiency of Material Use: Better utilization of raw materials and reduction in waste, making it a more sustainable option.
"Advanced sintering techniques like SPS and Pressure-Assisted Sintering not only enhance performance but also pave the way for more sustainable manufacturing methods."
Challenges in the Sintering Process
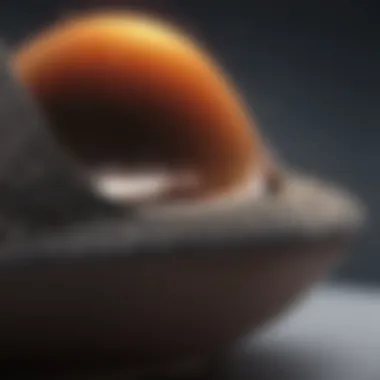
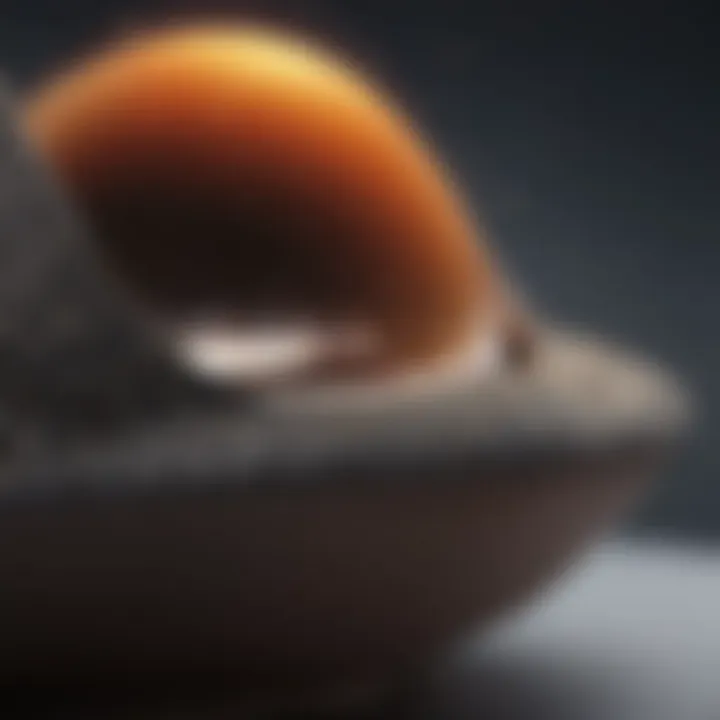
The field of material science has long honored the practice of sintering owing to its significant contributions in creating robust metal and ceramic products. However, navigating this process isn't all sunshine and rainbows. The challenges that manifest during sintering can derail the entire operation, leading not only to defective products but also to unwanted costs. Being attuned to these challenges is crucial for researchers and professionals alike. With that in mind, let’s take a closer look at two specific aspects that often trip up even seasoned experts.
Defects in Sintered Products
Defects in sintered materials are like dark clouds looming over an otherwise promising landscape. These defects can range from porosity to cracking, and their occurrence can severely impact the utility and longevity of the final product. Understanding these complications sheds light on not just the “what” but also the “how” of the sintering process.
- Porosity: High levels of porosity can result from insufficient sintering temperatures or inadequate time during the process. This can weaken the material's structure, making it less suitable for load-bearing applications.
- Cracking: Often attributed to uneven temperature distribution or rapid cooling, cracks in sintered products can render them unusable.
- Inhomogeneity: Variability in the microstructure can lead to inconsistent mechanical properties, limiting material reliability.
Addressing defects isn't merely about quality control; it's also about improving processes. Continuous advancements in characterization techniques foster a better understanding of how these defects arise and how to mitigate them. By implementing modifications in the sintering parameters, industries can achieve higher yields and better performance in their materials.
Cost Implications of Advanced Sintering
As we zoom into the financial aspect, the dialogue about sintering quickly shifts towards cost implications. Advanced techniques, while offering enhanced properties and performance, sometimes come with hefty price tags.
- Initial Investment: Adoption of state-of-the-art sintering technologies often requires significant upfront investment in equipment and infrastructure. For many smaller companies, this can prove to be a considerable hurdle.
- Operational Costs: Advanced sintering techniques, such as spark plasma sintering, can demand more energy or specialized materials, which pile on additional costs during production.
- Defect Management: Dealing with defects often involves reworking or discarding materials, further straining financial resources.
Thus, while the allure of advanced sintering processes is evident, it is essential that companies conduct a thorough cost-benefit analysis. A balanced approach allows for optimization while keeping an eye on the bottom line.
"Understanding the challenges involved in the sintering process isn't just an academic exercise; it paves the way for practical solutions that enhance both material performance and financial viability."
By delving into these challenges, the wider implications for future research and industrial efforts become evident. The journey to improve sintering processes hinges on addressing these hurdles directly head-on.
Future Trends in Sintering Research
As the world of material science continues to evolve, so too does the field of sintering. This section delves into the future trends in sintering research, emphasizing the critical innovations and sustainability efforts shaping the direction of this vital process. Understanding these emerging trends is not only essential for researchers but also for industries relying on advanced materials.
Innovations in Materials Science
The ongoing advancements in materials science are redefining traditional boundaries in sintering techniques. New materials and composites are being explored, which promise enhanced performance and versatility. One noteworthy trend is the integration of nanotechnology, where the manipulation of materials at a molecular level allows for improved properties in sintered products.
A significant benefit of these innovations is the potential for producing lighter and stronger materials. For instance, the use of nano-sized ceramics in sintering can lead to products that withstand higher pressures and temperatures compared to conventional counterparts.
Here are several innovations currently making waves in the field:
- Metal Matrix Composites (MMCs): These materials combine metals with particulate reinforcements, leading to improved mechanical properties. Sintering these composites requires careful control of the process to ensure uniformity in strength and durability.
- Functionally Graded Materials (FGMs): These have varying compositions and properties across their volume. Research focuses on how sintering can be tailored for FGMs, enhancing their applications in fields like aerospace and biomedical devices.
- Additive Manufacturing Integration: Blending sintering with additive manufacturing techniques opens the door for producing complex shapes that traditional methods simply cannot achieve.
"The future of sintering lies in embracing flexibility and innovation in material development."
Sustainability in Sintering Processes
With rising environmental consciousness, sustainability practices are becoming increasingly integrated into the sintering process. Research is focusing on reducing energy consumption and waste generation during sintering. For example, improving process efficiencies can significantly minimize the carbon footprint associated with traditional sintering methods.
Some ways that sustainability is finding its place in sintering include:
- Use of Renewable Resources: Many researchers are investigating the viability of using biodegradable polymers or bio-based materials in the sintering process. This can lead to reduced reliance on fossil fuels and lower toxicity in the final products.
- Energy-Efficient Sintering: Techniques such as microwave or flash sintering are gaining traction as they require significantly less energy than conventional sintering methods.
- Waste Reutilization: Innovators are also exploring ways to recycle sintering byproducts, turning potential waste into valuable resources for new materials.
Achieving sustainability is not merely a reaction to regulatory pressures; it’s becoming a competitive advantage. Companies that embrace these methodologies may experience increased customer loyalty and improved market positioning, given the growing importance of environmentally responsible practices in consumer choices.
In summary, integrating innovations in materials science and focusing on sustainability is essential for advancing sintering research. As these trends continue to develop, they will reshape not only the methods used in sintering but will also impact the entire materials industry. This makes it crucial for researchers and professionals to keep abreast of these developments, ensuring that they remain at the forefront of this pivotal field.
Finale and Implications of Sintering
The sintering process, essential in material science, stands at the crossroads of innovation and application. By merging powdered materials through heat and sometimes pressure, it creates solid structures vital for the manufacturing of various substance, especially metals and ceramics. The implications of sintering reach far beyond mere production; they impact efficiency, sustainability, and the overall performance of end products. The understanding and mastery of sintering can significantly influence industrial practices and material advancements.
Summary of Key Findings
Throughout this discussion, several key findings underscore the significance of sintering.
- Importance of Process Parameters: The temperature, pressure, and particle characteristics all determine the efficacy of sintering; a slight alteration can lead to vastly different product qualities.
- Role of Sintering Techniques: Different techniques cater to diverse materials and applications. For instance, while solid-state sintering excels in metals, liquid-phase sintering finds its strengths in ceramics and composites.
- Challenges and Innovations: Despite its advantages, the sintering process is not without hurdles. Defects can arise, affecting economic viability and product reliability. Continued research into advanced techniques is crucial for mitigating these issues.
The examination of these findings reveals not just intricacies of sintering, but also the role it plays in fostering advancements in material science.
Impact on Future Material Development
The ongoing evolution of sintering is poised to reshape material development in exciting ways. As industries lean towards lightweight materials that offer strength without heft, sintering methods will likely adapt, leading to the development of more efficient materials.
Several factors contributing to this transformation include:
- Innovative Material Use: New powders and blends are emerging, offering enhanced properties tailored to specific applications, which sintering processes can optimize effectively.
- Sustainability Focus: With growing environmental concerns, the emphasis may shift towards sintering practices that minimize waste and energy consumption. Research into greener methods could redefine standards in manufacturing.
- Customization and Precision: Advances in technology, such as 3D printing, have the potential to blend with sintering processes for bespoke material solutions, pushing the boundaries of what these methods can achieve.
In summary, sintering encapsulates a fundamental process, holding the keys to future advancements in material science. It combines heritage with innovation, paving the way for new applications that can meet the challenges of tomorrow's engineering and technological demands.
"Sintering is more than just a processing technique; it's a bridge connecting materials science to practical applications.
This understanding is not merely academic; it carries practical implications that touch industries worldwide, from aerospace to electronics. As research intensifies and challenges are met, the path forward looks promising for both professionals and the materials they create."