Exploring Advances in Generative Topology Optimization
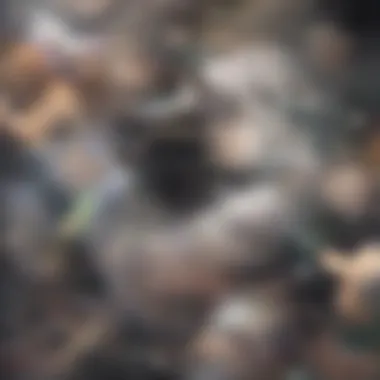
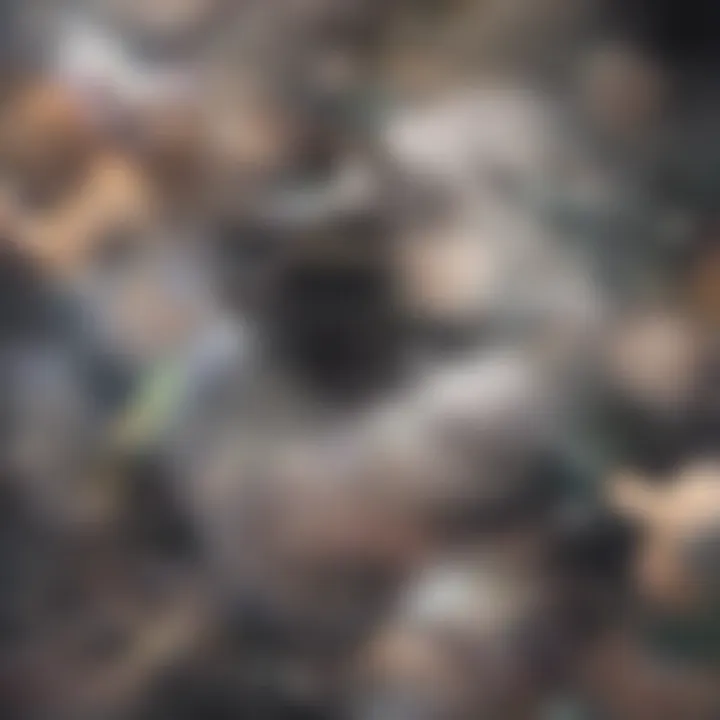
Intro
Generative topology optimization is a rapidly evolving area that has transformed how we approach structural design and engineering. The fundamental principle behind this approach involves using sophisticated algorithms to improve the efficiency and functionality of structures. By integrating various constraints and design objectives, practitioners can derive shapes and forms that may not be easily conceived through traditional methods. This article seeks to provide a thorough examination of the methodologies and applications that are now becoming common in various industries.
Research Background
Overview of the scientific problem addressed
The primary challenge that generative topology optimization addresses is the inefficiency often found in conventional design practices. Traditional methods tend to rely heavily on iterative testing and manual adjustments, which can be both time-consuming and resource-intensive. As projects grow in complexity and demands for lighter yet stronger materials increase, designers and engineers search for more efficient approaches. Generative topology optimization offers a solution by leveraging algorithms that can analyze a wide range of variables and constraints to minimize material usage while maximizing structural performance.
Historical context and previous studies
The roots of topology optimization can be traced back to the late 20th century. As computational technologies advanced, researchers began to explore mathematical and computational models that could inform design processes. Early studies focused on simple geometries and limitations in computing power often restricted the application of these techniques. However, the advent of more powerful computing systems and sophisticated algorithms has spurred significant advancements. Key contributions in the field include methodologies by researchers such as Bendse and Sigmund, who laid the groundwork for modern approaches to topology optimization.
Findings and Discussion
Key results of the research
Recent advancements in generative topology optimization reveal a myriad of benefits across different sectors. Industries ranging from aerospace to automotive are embracing these technologies to create components that are not only lighter but also more robust and efficient. Several case studies, such as those from Airbus and BMW, showcase how generative techniques can yield designs with far lower material usage compared to traditional methods.
Interpretation of the findings
The implications of these findings extend beyond mere material savings. By employing generative topology optimization, organizations can reduce manufacturing costs and enhance product sustainability. Moreover, the ability to quickly iterate designs based on targeted parameters allows for greater innovation. This level of efficiency, however, does carry challenges. One notable aspect is the need for designers to adapt to a more algorithmic approach to design, moving away from the conventional art of engineering to a more data-driven methodology.
This brief overview of the advancements and applications in generative topology optimization provides insight into both its potential and limitations. Further sections will explore mathematical foundations, practical applications, and the ongoing advancements in more detail.
Understanding Generative Topology Optimization
Generative topology optimization is an essential aspect of modern engineering and design practices. This approach focuses on enhancing the efficiency of structures while minimizing resources, such as material and time. Its significance lies in the ability to create optimized designs that meet specific performance criteria without compromising aesthetics or functionality.
In this section, we will outline key elements that define generative topology optimization, including its benefits and relevant considerations. Understanding these aspects can help students, researchers, and professionals appreciate its impact across various industries.
Definition and Conceptual Framework
Generative topology optimization refers to a computational design method that explores and evaluates various structural configurations. This is done through advanced algorithms and mathematical models, allowing engineers to identify optimal layouts based on defined performance objectives. The primary goal is to optimize a given design for load-bearing capacity while reducing weight and material usage.
A distinct feature of this technique is its generative nature. It works by generating multiple solutions to a design problem, rather than solely adjusting existing designs. It uses the principles of physics and engineering to assess how forces interact with a structure, resulting in configurations that may not be immediately intuitive to a designer. By embracing complex shapes and unconventional designs, generative topology optimization encourages innovation in engineering.
Historical Context and Evolution
The journey of generative topology optimization can be traced back to the 20th century when the need for more efficient designs began to gain prominence. Early computer-aided design (CAD) tools provided engineers with more capabilities, but they still relied heavily on traditional design practices. The shift towards optimization began to gain traction with the introduction of finite element analysis (FEA), which allowed for more in-depth analysis of mechanical structures.
In the late 20th and early 21st centuries, as computational power increased, so did the complexity of algorithms used for optimization. Various industries, including aerospace, automotive, and architecture, began to adopt these methods more broadly, pushing the boundaries of what was previously achievable in design. The integration of machine learning in recent years has further transformed the landscape, allowing for faster and more accurate optimization processes.
Generative topology optimization continues to evolve, with ongoing research focusing on improving algorithms, reducing computational costs, and expanding its application scope. The historical journey of this discipline illustrates its significance in contemporary design and engineering practices.
Mathematical Foundations
Understanding the mathematical foundations of generative topology optimization is essential for deciphering how these advanced techniques work. These principles dictate how design parameters can be manipulated and optimized to reach superior outcomes in structural engineering and design.
Effective topology optimization relies on rigorous mathematics to formulate problems in a way that they can be solved using computational methods. Key elements include functions that measure performance criteria, constraints which define valid designs, and optimization algorithms that search for the most efficient solutions. Recognizing these building blocks helps in appreciably advancing the design process, allowing engineers and researchers to make informed decisions.
Optimization Algorithms Overview
Optimization algorithms are the backbone of generative topology optimization. These mathematical procedures identify the best solution from a set of feasible options. Various algorithms are employed, each with its strengths and weaknesses. Popular choices include gradient-based methods, genetic algorithms, and particle swarm optimization.
- Gradient-based methods are effective for smooth, continuous problems. They utilize gradients to find local minima, but they can struggle with complex geometries.
- Genetic algorithms simulate natural selection, working well with non-continuous and complicated problems. They explore a broader solution space but can be computationally intensive.
- Particle swarm optimization mimics social behavior patterns to search for optimal solutions. It is known for its efficiency in large search spaces and ease of implementation.
In practice, combining these algorithms often provides enhanced results, leveraging the strengths of each method.
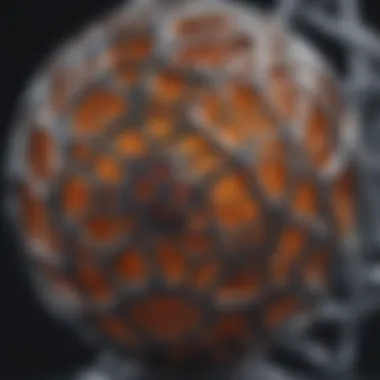
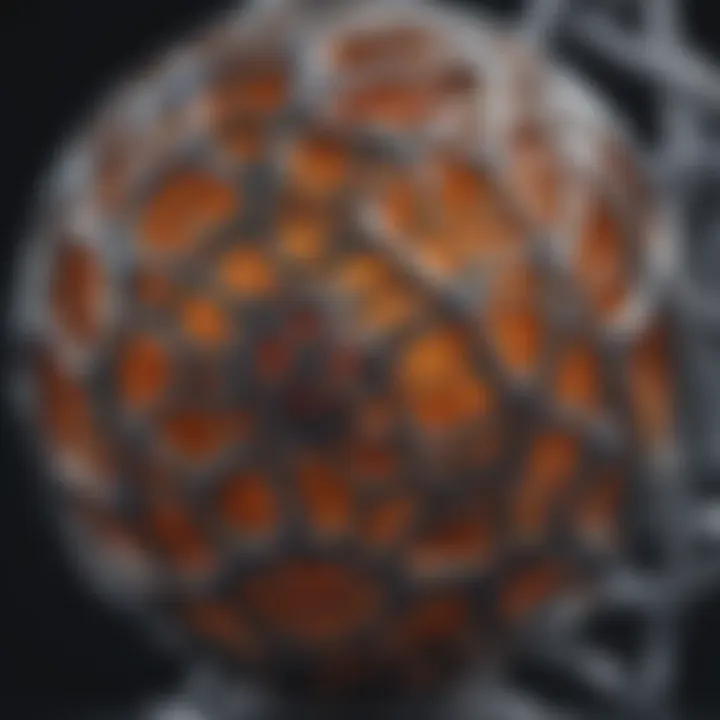
Mathematical Models in Topology Optimization
Mathematical models bring structure to the concept of topology optimization. These models define the relationship between design variables and the performance of the structure. They can incorporate considerations such as material properties, geometrical constraints, and loading conditions.
A common approach involves using the finite element method (FEM) to assess how different designs respond under various loads. The model typically includes:
- Design Variables: Parameters that can change in design, e.g., material distribution.
- Objective Function: A mathematical expression that needs to be minimized or maximized, such as weight or compliance.
- Constraints: Limitations that the design must satisfy, such as displacement or stress limits.
Mathematical models facilitate iterative design processes, guiding modifications based on quantitative feedback.
"Effective implementation of mathematical foundations in generative topology optimization not only improves the design quality but also enhances efficiency in the engineering process."
In summary, the mathematical foundations of generative topology optimization are pivotal for developing advanced designs. They provide the necessary framework to optimize performance, ensuring that engineered structures meet their intended objectives efficiently.
Key Technologies in Generative Topology Optimization
Generative topology optimization relies on several key technologies that enhance its effectiveness and adoption across different fields. Understanding these technologies is essential for grasping how generative topology optimization applies to real-world problems. This section focuses on the role of Finite Element Analysis and Machine Learning Integration, highlighting the specific elements, benefits, and considerations associated with each.
Finite Element Analysis (FEA)
Finite Element Analysis, or FEA, is a critical component in generative topology optimization. This computational method allows engineers and designers to simulate how a product will react to real-world forces, vibration, heat, and other physical effects. The power of FEA lies in its ability to decompose complex geometries into manageable finite elements, simplifying analysis and providing detailed insights into structural behavior.
The integration of FEA in generative topology optimization offers several advantages:
- Detailed Evaluation: FEA enables precise modeling of stress, strain, and displacement under various loading conditions. This granularity helps in understanding the performance of designs before they are manufactured.
- Iterative Design Process: The iterative nature of topology optimization, in conjunction with FEA, allows for continuous refinement of designs. Designers can tweak parameters and analyze results, leading to optimized structures that save material without compromising performance.
- Multi-Physics Capabilities: FEA supports multi-physics simulations, meaning it can evaluate structures under different physical conditions simultaneously. This feature is particularly valuable in complex engineering applications where thermal, fluid, and structural dynamics interact.
Utilizing advanced FEA software tools provides designers the capability to explore a variety of solutions, weighing the pros and cons of each one in a virtual environment. This capacity to identify manufacturing constraints and operational behaviors is crucial for validating topology-optimized designs.
Machine Learning Integration
The integration of Machine Learning into generative topology optimization is a transformative advancement that significantly enhances design capabilities. Machine Learning allows for the automation of design processes, leading to faster and more efficient outcomes.
Several important elements characterize the role of Machine Learning in this field:
- Predictive Analytics: Machine Learning algorithms can analyze vast amounts of data from past designs and performance metrics. By finding patterns, these systems can predict how new design choices might perform, leading to better-informed decision-making.
- Generative Design: The use of Machine Learning enables generative design methods, where the software creates numerous design alternatives based on predefined constraints and goals. This can lead to innovative solutions that human designers might overlook due to cognitive biases.
- Improved Efficiency: Machine Learning can streamline the overall design process. By automating repetitive tasks, it reduces the time and effort required for manual analyses, allowing engineers to focus on more strategic aspects of design.
However, integrating Machine Learning is not without challenges. Ensuring high-quality data for training models is critical, as poor data can lead to inaccurate predictions. Moreover, there is a learning curve associated with adopting these technologies, necessitating investment in training and resources.
"The convergence of Machine Learning with traditional engineering practices brings unprecedented opportunities for innovation in design."
Application Areas
Generative topology optimization finds extensive usage across various industries. This applicability demonstrates its potential to transform design practices, enhance product performance, and drive innovation. The adaptability of this optimization technique allows engineers and designers to tackle specific challenges unique to each field. By understanding its significance in diverse areas, professionals can harness its capabilities more effectively, leading to improved outcomes.
Aerospace Engineering
Aerospace engineering hugely benefits from generative topology optimization due to the critical need for weight reduction and structural efficiency. Components like aircraft wings and fuselage sections face tremendous load demands while requiring minimal weight. Traditional design approaches often do not yield the best results, making advanced technologies necessary. By using generative topology optimization, engineers can explore a range of complex geometries that meet performance specifications while reducing overall material usage. This efficiency also translates into enhanced fuel efficiency, which is crucial in an industry focused on sustainability.
Automotive Industry
In the automotive industry, generative topology optimization aids in meeting both performance and safety standards. Cars require parts that can withstand significant stress while being as light as possible. Here, optimization techniques allow for innovative designs that improve the strength-to-weight ratio. For instance, components such as chassis and suspension systems can be designed to enhance both safety and fuel economy. As electric vehicles gain momentum, optimizing components for weight reduction directly impacts range and efficiency. Furthermore, the automotive industry emphasizes fast production cycles, and generative topology optimization often streamlines the design and prototyping processes.
Civil Engineering
The field of civil engineering also finds value in generative topology optimization. Structural elements in buildings, bridges, and infrastructures must meet stringent regulatory standards while being cost-effective. This optimization helps architects and engineers create efficient designs that utilize materials judiciously without compromising safety. The impact of using optimized designs extends to reducing construction costs and time. For instance, optimized formworks and reinforcements can enhance the longevity of structures while minimizing environmental impacts associated with material production and transportation.
Biomedical Devices
In biomedical applications, generative topology optimization excels in developing devices that are tailored to the specific requirements of patient care. Custom implants and prosthetics benefit from unique geometries that match anatomical features for superior fit and function. This precise tailoring enhances user comfort and device efficacy. Furthermore, optimization can facilitate the development of lighter, more durable tools and instruments in surgical procedures, leading to better outcomes. As the healthcare industry continues to embrace technology, the role of topology optimization will likely grow, pushing the boundaries of how devices are designed and used.
Generative topology optimization represents not just a method, but a paradigm shift across multiple domains. Its principles reduce material waste and enhance performance while encouraging innovation and sustainability.
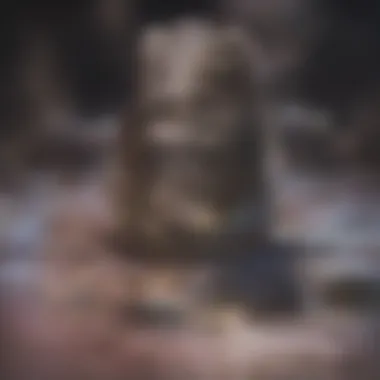
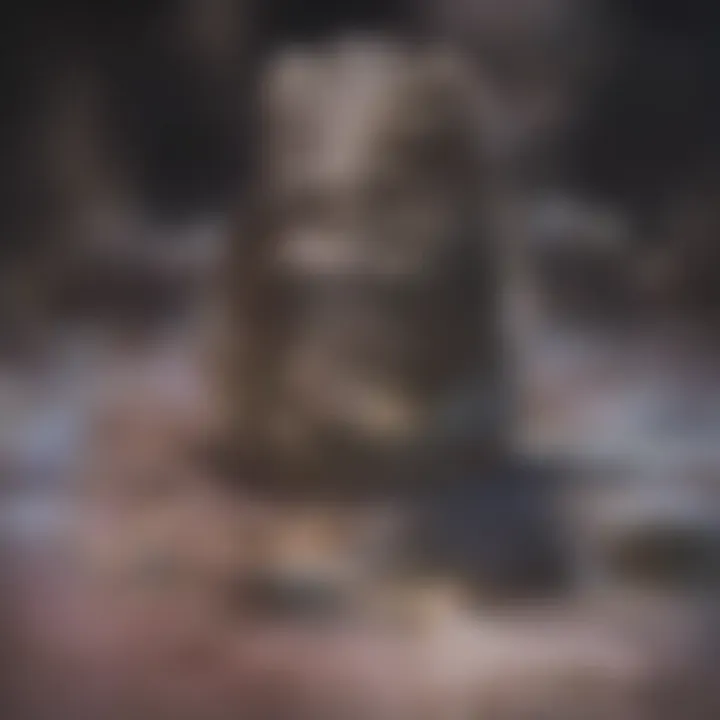
Benefits of Generative Topology Optimization
Generative topology optimization is a transformative approach in engineering design, significantly affecting material usage, structural weight, and overall performance. The importance of this topic lies in its capacity to redefine traditional methods, bringing forth a more robust and flexible framework for innovation. By utilizing advanced computational techniques, this optimization process allows for better resource management and a more sustainable approach to design.
Material Efficiency
Generative topology optimization enhances material efficiency by systematically reducing unnecessary material within a structure. The algorithms identify areas where material is either redundant or underutilized, allowing engineers to conserve resources without compromising structural integrity. The outcomes of this optimization approach lead not only to cost savings but also to a lower environmental impact associated with material production.
- Evaluation of loads: The process begins with understanding the load conditions that the structure must withstand.
- Stress distribution: By analyzing stress distribution, the software can suggest designs that maintain strength while minimizing material usage.
- Iterative refinement: The design is iteratively refined, ensuring it fulfills performance requirements while being as resource-efficient as possible.
Weight Reduction
A crucial benefit of generative topology optimization is weight reduction. Lighter structures enhance performance and efficiency for various applications. For example, in aerospace or automotive industries, weight savings can directly translate to fuel efficiency and increased payload capacity. By redistributing material only to areas of need, structures become aerodynamically advantageous and easier to handle.
Key aspects of weight reduction through this optimization include:
- Selective material allocation: Emphasizes minimal material placement where high strength is necessary.
- Structural integrity: Ensures that weight reduction does not compromise the integrity and durability of the component.
- Performance optimization: Facilitates superior performance characteristics leading to faster and more efficient operations.
Improved Performance
The enhanced performance of structures optimized through generative techniques is evident across various fields. Performance indicators such as stability, durability, and efficiency see notable improvements thanks to targeted material distribution and engineering insights.
The ways in which performance is improved include:
- Enhanced load-bearing capabilities: Through precise material distribution, structures can better withstand applied forces.
- Increased lifespan: Optimized materials tend to have longer service lives due to reduced stress concentrations and weaknesses.
- Greater adaptability: Structures designed with optimization in mind can adapt to varying load scenarios, leading to innovations in design flexibility.
With each of these benefits, generative topology optimization demonstrates its potential to revolutionize engineering design by fostering innovations that prioritize efficiency, sustainability, and performance.
Challenges and Limitations
Generative topology optimization has transformed the way engineers approach design. However, it is not without its challenges and limitations. Understanding these elements is crucial in assessing the practical application of this technology. This section will explore the two primary challenges: computational complexity and design constraints.
Computational Complexity
Computational complexity in generative topology optimization arises from the intricate algorithms required to perform the optimization processes. These algorithms often involve solving large-scale mathematical models that can be computationally intensive. As a result, significant computational resources are needed.
The iterative nature of optimization means that multiple design iterations must be evaluated to reach the optimal solution. Each iteration generates a new mesh or topology, requiring further analysis.
High-performance computing is often necessary to handle the vast amount of data produced during these processes. As optimization problems increase in size and complexity, they can exhibit non-linear behaviors that are hard to predict. This can lead to longer processing times and the need for more powerful hardware, which may not always be feasible for all organizations.
Also, as the algorithms evolve and incorporate more variables, the necessary computational effort tends to increase. Companies or individuals lacking advanced computational facilities may find it challenging to implement generative topology optimization effectively. Therefore, managing computational demands while maintaining efficiency becomes a significant constraint in practice.
Design Constraints
Design constraints present another significant limitations in the realm of generative topology optimization. While the aim is to innovate and create optimal structures, real-world applications often require adherence to specific standards and regulations. These constraints can significantly influence the optimization process.
For example, factors such as material properties, manufacturing methods, and safety regulations must be integrated into the design process. Ignoring these aspects may lead to designs that are theoretically efficient but impractical in production.
Furthermore, physical limitations such as the maximum allowable loads or environmental conditions can restrict the optimization process. It is critical for engineers to incorporate these practical elements in their models to derive realistic and applicable designs.
In many cases, the freedom to explore various topologies might be curtailed due to the necessity of conforming to existing frameworks or systems within an industry. This can limit the extent to which innovations can be realized, pushing designers to navigate a fine balance between optimal performance and practical feasibility.
Ultimately, understanding the challenges associated with computational complexity and design constraints is essential for effectively leveraging generative topology optimization in real-world applications.
Future Trends in Generative Topology Optimization
The landscape of generative topology optimization is rapidly evolving. In this section, we will explore future trends that are likely to shape the field. Understanding these trends is crucial for researchers, practitioners, and educators who seek to stay ahead in this dynamic area of engineering and design. The integration of advanced algorithms with emerging technologies will profoundly impact various industries. This segment highlights key elements, benefits, and considerations for the future of generative topology optimization.
Advancements in Algorithms
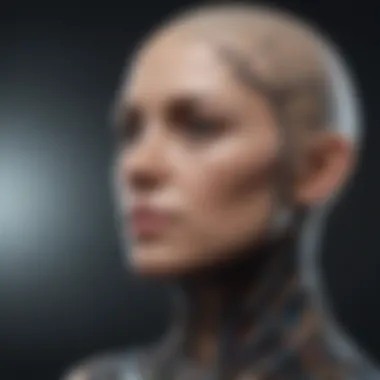
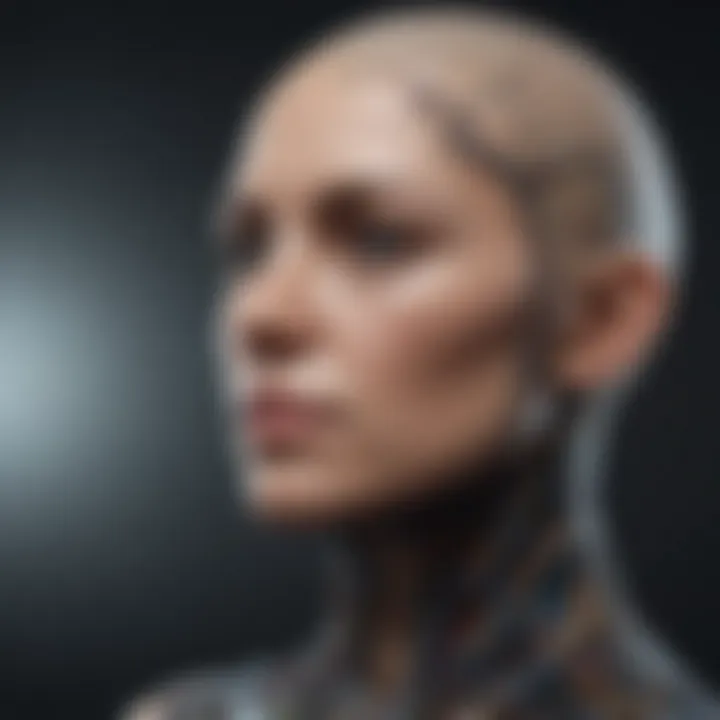
One of the most significant trends in generative topology optimization is the continuous development of optimization algorithms. With a focus on enhancing computational efficiency, researchers are working tirelessly to create algorithms that can handle more complex design problems. These advancements often involve the use of machine learning and artificial intelligence to optimize processes further. Some of the emerging algorithms include:
- Multilevel Optimization: This method allows for handling different levels of detail within the design simultaneously, enhancing efficiency.
- Genetic Algorithms: By mimicking natural selection, these algorithms can explore a wide range of designs, often leading to innovative solutions.
- Gradient-Based Methods: These techniques take advantage of derivatives to guide the optimization process, resulting in faster convergence.
As algorithms become more sophisticated, they will enable designers to tackle larger and more intricate structures. This opens the door for applications that were previously unfeasible. The adaptability of these algorithms to various materials and constraints makes them indispensable in today's engineering landscape.
Integration with Additive Manufacturing
Another promising trend is the integration of generative topology optimization with additive manufacturing processes. Additive manufacturing, or 3D printing, has changed the way products are designed and fabricated. It allows for the creation of complex geometries that traditional manufacturing methods cannot achieve.
This convergence leads to multiple advantages:
- Design Freedom: Designers can create shapes that are optimized for performance while also being manufacturable using additive techniques.
- Material Savings: Optimized designs often lead to less material usage, which makes production more sustainable and cost-effective.
- Shorter Production Times: The streamlined process from design to fabrication can reduce lead times significantly.
Considerations also arise with this integration. The necessity for close collaboration between the design and manufacturing teams becomes more critical. Moreover, understanding the material behavior during the additive process is vital for ensuring the final product meets performance criteria.
The synergy between generative topology optimization and additive manufacturing is more than just a trend; it represents a revolutionary shift in how we conceptualize and produce engineered products.
In summary, advancements in algorithms and the integration with additive manufacturing are setting the stage for the next phase of generative topology optimization. As these trends continue to evolve, they promise to drive innovation and efficiency across various industries. Keeping abreast of these developments is essential for anyone involved in the field.
Case Studies
Case studies are vital in showcasing the practical applications and effectiveness of generative topology optimization. They offer real-world examples that illustrate how theoretical principles translate into beneficial outcomes in various industries. Through examining notable projects and industrial implementations, readers gain insights into the innovative potential and tangible results of applying these optimization techniques.
Case studies also serve several important purposes:
- Demonstration of Effectiveness: They provide proof of the viability and success of generative topology optimization in solving complex design challenges.
- Learning Opportunities: Each case presents a unique set of circumstances and solutions, from which other practitioners can learn and adapt to their contexts.
- Innovation Tracking: Keeping an eye on case studies allows professionals to identify emerging trends, technologies, and methodologies that can influence future designs.
By analyzing case studies, one engages with both the theoretical and practical dimensions of generative topology optimization, thus offering a well-rounded understanding of its significance.
Notable Research Projects
Research projects in the field of generative topology optimization have pushed the boundaries of design and engineering. One noteworthy project involved the aerospace sector, where a team utilized advanced algorithms to enhance the structural integrity of an aircraft wing. Researchers at the Massachusetts Institute of Technology developed a topology optimization method that resulted in a 20% weight reduction while maintaining performance standards. This project highlighted the potential of optimization to improve efficiency without compromising safety.
Another significant research undertaking, undertaken by Stanford University, focused on optimizing components for electric vehicles. By employing generative design tools, engineers were able to create intricate components that reduced material usage and enhanced performance. The results underscored the capacity for generative geometry to foster sustainability in the automotive industry.
These research endeavors not only validate the methodologies employed but also encourage further inquiry into the adaptability of generative topology optimization in other sectors.
Industrial Implementations
In industry, the applications of generative topology optimization are numerous and impactful. Companies such as Airbus and General Electric have effectively integrated these techniques into their design processes.
Airbus, for instance, implemented topology optimization in the design of complex aircraft components. This approach helped reduce manufacturing costs and improve functionality by creating components that are lighter and yet structurally sound. Furthermore, General Electric applies generative design principles in the production of jet engine parts, leading to enhanced performance and reduced environmental impact.
Benefits of these industrial implementations include:
- Sustainability: Companies are able to use fewer resources, leading to more eco-friendly products.
- Reduced Lead Time: Enhanced design processes result in shorter timelines from conception to production.
- Increased Competitive Advantage: The ability to produce innovative products keeps companies at the forefront of their industries.
Epilogue and Outlook
The exploration of generative topology optimization presents an invaluable perspective on the future of design and engineering across various industries. This article emphasizes the integral role that generative topology optimization plays in enhancing structural efficiency and innovation. The synthesis of complex algorithms with real-world applications exemplifies the advancement of modern engineering methodologies. From aerospace to civil engineering, the implications of these techniques are far-reaching.
Moving forward, it is crucial to consider how advancements in generative topology optimization can contribute to ongoing challenges and innovations in design practices. The ability to produce optimized structures that utilize materials efficiently not only benefits individual industries but also supports broader sustainability goals.
Summarizing Key Insights
- Definition and Importance: Generative topology optimization represents a paradigm shift in design paradigms, allowing for a more efficient use of materials and resources.
- Mathematical Foundations: The underlying mathematical models and algorithms provide a structured approach to solving complex design problems, making optimization a systematic process.
- Technological Integration: The integration of technologies such as finite element analysis and machine learning enhances the capability of such optimization methods, leading to superior results.
- Practical Applications: The application of generative topology optimization spans multiple sectors, illustrating its versatility and effectiveness in real-world scenarios.
- Future Potential: As new algorithms emerge and become more sophisticated, the potential applications will continue to expand, especially in the realm of additive manufacturing.
In summary, the advancements made through generative topology optimization provide significant benefits in design efficiency and material use.
Implications for Future Research
The future of generative topology optimization is ripe with opportunities for further study and application. Key areas of focus include:
- Algorithm Development: Continued research into more advanced algorithms can enhance the capabilities of topology optimization, allowing for complex geometries and new material applications.
- Interdisciplinary Approaches: Collaboration between fields such as materials science, artificial intelligence, and structural engineering can lead to groundbreaking innovations.
- Sustainability Considerations: Emphasizing sustainable design and construction will become more vital as industries move toward environmentally friendly practices.
- Real-World Case Studies: Documenting successful implementations will pave the way for broader acceptance and understanding of generative topology optimization in various industries.
The synthesis of these insights not only concludes the current discussion but also sets the stage for future research directions. By understanding generative topology optimization's role today, we can better anticipate its applications tomorrow.