High Sensitivity Pressure Sensors Explained
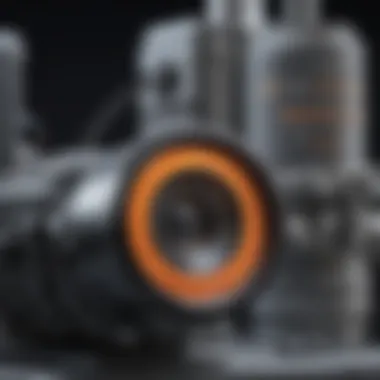
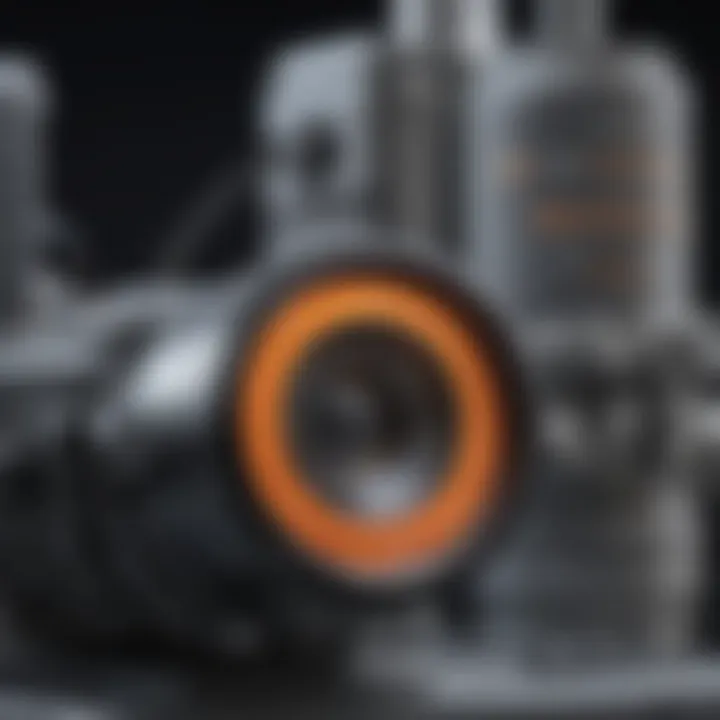
Intro
High sensitivity pressure sensors have emerged as crucial elements in a variety of fields, ranging from aerospace to healthcare. Their role in improving precision in measurements cannot be overlooked. Advances in technology demand that these sensors perform with accuracy and robustness under diverse conditions. This article aims to provide a third-party perspective on the operating principles, types, materials, and applications of high sensitivity pressure sensors, tailored for both experts and new learners in the field.
The significance of this exploration lies in the understanding of how these sensors impact technological development and contribute to various industrial applications. By shedding light on the underlying mechanisms and recent innovations, this narrative aspires to enrich the reader's knowledge and stimulate further inquiry into the potential of high sensitivity pressure sensors.
Research Background
Overview of the Scientific Problem Addressed
The development of high sensitivity pressure sensors addresses a fundamental need in measuring minute changes in pressure with high accuracy. Traditional pressure sensing methods often fall short when it comes to discerning slight variations due to environmental conditions or small-scale phenomena. Thus, high sensitivity pressure sensors fill this gap, enabling more reliable data collection, which is essential for many functional systems.
Historical Context and Previous Studies
The evolution of pressure sensing technology dates back several decades, with early sensors being relatively simple mechanical devices. With rapid advancements in materials science and electronic engineering, the field has transformed significantly. Research has shown that using piezoelectric materials, for instance, can enhance the sensitivity of these sensors. Historical studies have set the foundations for current developments. Notably, papers detailing the evolution of micro-electromechanical systems (MEMS) have paved the way for ultra-compact and efficient pressure sensing solutions.
High sensitivity pressure sensors are often essential in critical applications such as aviation, medical devices, and industrial automation, where precision is paramount.
This historical understanding helps contextualize the modern advancements and highlights the importance of continued research in developing more effective and innovative pressure sensors.
Preface to High Sensitivity Pressure Sensors
High sensitivity pressure sensors play a crucial role in modern technology and industry. Understanding their workings, significance, and applications is essential for professionals and researchers in various fields. This introduction outlines the importance of high sensitivity pressure sensors and sets the stage for the discussion of their key attributes and historical journey.
Definition and Importance
A high sensitivity pressure sensor is a device designed to measure pressure with an enhanced degree of precision. These sensors can detect minute changes in pressure, often in the range of a few pascals. The ability to accurately measure low pressures makes them invaluable in numerous applications, from aerospace to medical devices. The importance of these sensors lies in their ability to improve safety, performance, and reliability in systems where pressure is a critical factor.
Their relevance can be seen in industries such as:
- Aerospace: Monitoring cabin pressure and ensuring flight safety.
- Medical devices: Used in ventilators and infusion pumps to provide precise control.
- Automotive: Enabling advanced functions like tire pressure monitoring systems.
In each case, the enhanced accuracy provided by high sensitivity pressure sensors often translates to better overall system performance and efficiency.
Historical Development
The development of pressure sensors has a rich history, dating back centuries. Initially, pressure measurement was conducted using basic mechanical devices like mercury barometers. However, the introduction of electronic sensing technologies in the mid-20th century marked a major leap forward.
By the 1960s and 1970s, the advent of silicon-based sensors began to change the landscape significantly. These sensors offered improved sensitivity and miniaturization, making them suitable for various applications. Over the decades, continuous advancements in materials and technologies have enhanced the functionality of these sensors.
Today, high sensitivity pressure sensors are built with sophisticated elements such as piezoelectric and capacitive mechanisms, each contributing to enhanced accuracy and reliability. As technology evolves, new materials and designs continue to emerge, ensuring that these sensors remain at the forefront of innovation and industrial practice.
"The evolution of high sensitivity pressure sensors reflects the advancements in technology, leading to more precise and reliable monitoring across multiple disciplines."
Understanding this historical context not only highlights the importance of these sensors but also showcases the innovations that have shaped their current state.
Operating Principles of Pressure Sensors
Understanding the operating principles of pressure sensors is crucial for comprehending their functionality and applications across various fields. This section will explore several key elements. First, the basic mechanisms provide insights into how these sensors transform pressure into electrical signals. Such transformations are fundamental for accurate measurements in technology and research. Second, we will delve into sensitivity factors. Without exploring sensitivity, it is challenging to appreciate the varying performance of different sensors and their applicability in nuanced environments.
Basic Mechanisms
Pressure sensors operate by converting pressure into an electrical signal. The fundamental mechanism often relied upon is the change in resistance, capacitance, or piezoelectric properties when subjected to pressure changes. The most common types utilize either capacitive or resistive technologies.
- Capacitive Sensors: These sensors operate by measuring the change in capacitance caused by a deflection in a diaphragm. When pressure is applied, the diaphragm flexes, altering the distance between two conductive plates. This distance change results in a measurable change in capacitance.
- Resistive Sensors: Resistive pressure sensors utilize resistive strain gauges. These gauges detect stress or deformation in the sensing element when pressure is applied. The deformation results in a change in resistance, which is then translated into an electrical signal.
- Piezoelectric Sensors: Piezoelectric pressure sensors take advantage of materials that generate an electrical charge in response to mechanical stress. Upon pressing, these materials produce a voltage that correlates directly with the applied pressure.
Each of these mechanisms has specific advantages depending on the application. Capacitive sensors tend to offer high precision, while resistive sensors are generally more robust.
Sensitivity Factors
Sensitivity is a critical characteristic of pressure sensors, as it determines the sensor's ability to detect small changes in pressure. Factors influencing sensitivity include:
- Material Properties: The choice of material plays a significant role. For instance, materials with high elasticity tend to offer better sensitivity due to their ability to deform under pressure.
- Geometry of the Sensor: The design and dimensions of the diaphragm or sensing element impact how effectively a sensor responds to changes in pressure. A thinner diaphragm, for example, may deflect more easily, enhancing sensitivity.
- Temperature Effects: Sensitivity can also be affected by temperature. As temperatures change, materials may expand or contract, altering their response to pressure similarly.
- Calibration: Regular calibration is fundamental. A well-calibrated sensor ensures improved accuracy and maintains its sensitivity over time. Sensors can drift, but recalibration helps retain their initial performance levels.
In summary, understanding the operating principles, basic mechanisms, and sensitivity factors of pressure sensors provides foundational knowledge for anyone involved in the integration or advancement of pressure sensing technology.
"The performance of a pressure sensor is inherently linked to its design, materials, and operational environment."
By grasping these essential elements, researchers and professionals can better appreciate the nuanced capabilities of high sensitivity pressure sensors.
Types of High Sensitivity Pressure Sensors
Understanding the types of high sensitivity pressure sensors is critical in appreciating their diverse applications and benefits. Each technology has unique characteristics that make it suitable for specific environments and measurement needs. By examining these sensors closely, we can ensure we select the appropriate type for particular use cases. The choice of pressure sensor can significantly impact precision, reliability, and overall system performance.
Capacitive Sensors
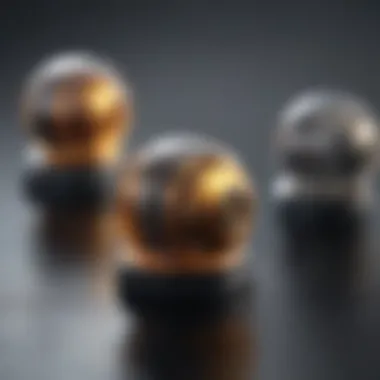
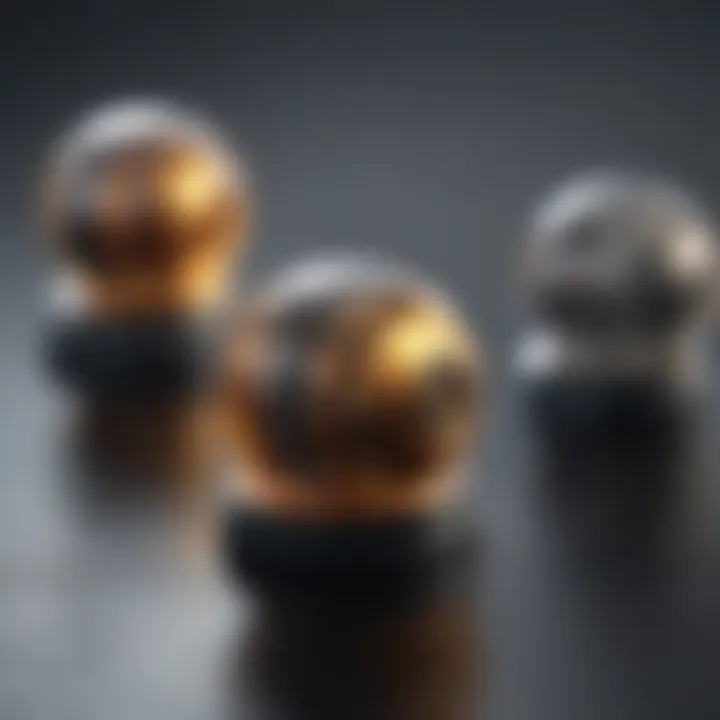
Capacitive sensors operate on the principle of capacitance change caused by pressure variations. They consist of two conductive plates separated by a dielectric material. When pressure is applied, the distance between the plates changes, leading to shifts in capacitance. This type of sensor is favored for its high sensitivity and small size, making it suitable for applications requiring precise measurements in limited spaces.
Some advantages include:
- High Resolution: Capacitance changes in response to minute pressure differences.
- Temperature Stability: These sensors maintain accuracy across a range of temperatures.
- Low Power Consumption: This feature is significant in battery-operated devices.
However, capacitive sensors can be affected by humidity and require careful calibration to ensure accuracy. They are frequently used in consumer electronics, medical devices, and some industrial applications.
Piezoelectric Sensors
Piezoelectric sensors harness the piezoelectric effect, wherein certain materials generate an electric charge in response to mechanical stress. They are robust and can react quickly to dynamic pressure changes, making them ideal for applications that involve fluctuating pressures. Piezoelectric sensors are widely used in measuring vibrations and dynamic pressure in aeronautical and automotive fields.
Key features include:
- High-Speed Response: They can quickly capture rapid changes in pressure.
- Wide Frequency Range: Useful for both low and high-frequency measurements.
- Excellent Linearity: They provide accurate measurements across a range of conditions.
This technology can have reduced sensitivity to static pressures, which might limit some applications. Despite this limitation, piezoelectric sensors are integral to fields such as structural health monitoring and acoustic measurements.
Optical Sensors
Optical sensors are an advanced type of pressure sensor that utilizes light to measure pressure measurements. The sensor employs laser or LED light sources and detects changes in light output in response to pressure variations. These sensors are praised for their high precision and non-invasive measurement capabilities.
Important attributes include:
- Immune to Electromagnetic Interference: They can operate effectively in environments with electromagnetic noise.
- Long Distance Capabilities: Can measure pressure without being in direct contact with the medium, ideal for hostile environments.
- Precision in Harsh Conditions: They can function in conditions unsuitable for other types of sensors.
However, optical sensors can be more expensive than other types and may require complex setups. Industries such as aerospace, medical diagnostics, and research laboratories often employ optical sensors due to their unique benefits.
As pressure sensing technologies advance, a keen understanding of these types allows for optimized applications ensuring efficiency and performance.
Materials Used in Pressure Sensors
Understanding the materials used in pressure sensors is essential for comprehending their operational capabilities and overall performance. High sensitivity pressure sensors rely on specific materials to achieve the required sensitivity, stability, and durability in various environments. Each material comes with its unique properties, which can significantly influence the sensor's effectiveness in different applications.
Silicon-based Materials
Silicon-based materials are among the most common substances used in high sensitivity pressure sensors. They are chosen for their excellent mechanical properties and compatibility with microfabrication techniques. Silicon exhibits high tensile strength and stability under various environmental conditions, making it suitable for demanding applications.
In pressure sensors, silicon is often used for the sensing elements. Its piezoresistive properties allow for the conversion of mechanical stress into an electrical signal, providing high sensitivity and accurate readouts. Moreover, the scalability of silicon fabrication techniques supports the production of small and complex sensors, which is crucial for modern electronic devices.
Metallic Alloys
Metallic alloys play a significant role in the manufacturing of high sensitivity pressure sensors, particularly in applications where robustness and temperature resistance are critical. Alloys such as stainless steel or Inconel are commonly used for housings and diaphragm components. These materials provide high strength and resistance to corrosive environments, ensuring the sensors can operate effectively over long periods.
The use of metallic alloys also allows for the construction of sensors that can withstand high pressures and temperatures, which is vital in industries such as aerospace and automotive. Furthermore, the durability of these materials contributes to the longevity of the sensors, reducing the frequency of replacements and maintenance.
Composite Materials
Composite materials are becoming increasingly popular in pressure sensor technology due to their unique advantages. They combine different materials to achieve desirable properties not found in individual substances. For example, composites can offer high strength-to-weight ratios and excellent thermal stability.
In pressure sensors, composites may be used to enhance mechanical properties while reducing weight. This is particularly important in aerospace applications where minimizing weight is a priority. Additionally, composites can be engineered to meet specific performance requirements, such as increased sensitivity or better environmental resistance.
"The choice of material directly affects not only the performance but also the application range of pressure sensors."
In summary, each type of material — silicon, metallic alloys, and composites — offers distinct advantages that enable high sensitivity pressure sensors to perform effectively across various industries. Their specific applications highlight the importance of selecting appropriate materials to meet performance needs.
Applications in Various Industries
High sensitivity pressure sensors play a critical role across a variety of industries. These sensors are not only central to improving operational efficiency, but also serve to enhance the safety and reliability of systems in which they are implemented. Understanding the applications of these sensors provides insight into their significance and benefits. Whether in aerospace, medical devices, automotive industries, or industrial machinery, the need for precision and reliability is paramount.
Aerospace
In the aerospace sector, high sensitivity pressure sensors are vital for numerous applications. They monitor cabin pressure to ensure passenger comfort and safety during flights. Engine performance is also critically linked to pressure measurements; variations in fuel and air pressure impact engine efficiency and safety. The sensors help detect leaks and other issues in real-time, preventing potentially dangerous situations. Moreover, advancements in sensor technology contribute to lighter and more fuel-efficient aircraft designs, thus helping in environmental sustainability efforts.
Medical Devices
The medical field relies heavily on accurate pressure measurements for patient care. High sensitivity pressure sensors are integral in devices such as ventilators and blood pressure monitors. These instruments require precise measurements to ensure that patients are receiving the correct amount of medication or support. In diagnostic equipment, such sensors enhance the accuracy of readings and improve patient outcomes. Their ability to function in harsh environments, like inside the human body, establishes their importance in medical technology advancement.
Automotive Industry
In the automotive industry, pressure sensors monitor a range of functions from tire pressure to engine performance. Maintaining optimal tire pressure is vital for vehicle safety and fuel efficiency, which directly impacts sustainability. The engine control unit utilizes pressure readings to manage fuel injection and exhaust systems, resulting in better performance and lower emissions. Moreover, sensors play a crucial role in advanced driver assistance systems, enhancing vehicle safety through monitoring various pressure-related parameters.
Industrial Machinery
Industrial machinery also benefits significantly from high sensitivity pressure sensors. In applications such as hydraulic systems, accurate pressure readings ensure machinery functions within safe and efficient parameters. This not only extends equipment life but reduces maintenance costs as well. Moreover, these sensors are crucial in process control and automation, enhancing efficiency and productivity across manufacturing environments.
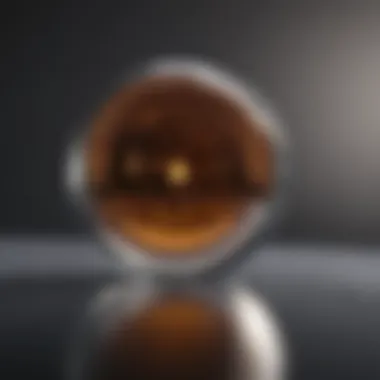
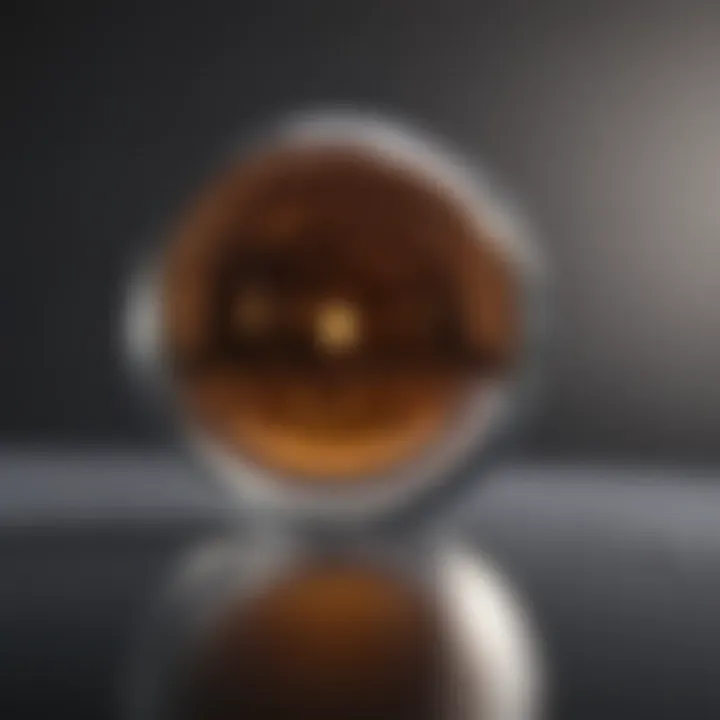
High sensitivity pressure sensors are indispensable across industries, influencing everything from safety protocols to efficiency measures. Their continual evolution suggests an ongoing trend towards even greater innovation and importance in future applications.
"The precision of pressure sensors directly influences the performance and safety of many systems we depend on daily."
Understanding these various applications aids professionals and researchers in appreciating the multifaceted uses of pressure sensors.
Advantages of High Sensitivity Pressure Sensors
High sensitivity pressure sensors bring numerous benefits to industries that rely on precise measurements. Understanding their advantages not only highlights their significance in applications but also informs future developments in sensor technology. This section focuses on three main advantages: enhanced accuracy, increased measurement range, and improved stability. Each of these elements plays a critical role in making high sensitivity pressure sensors indispensable in modern engineering and technology.
Enhanced Accuracy
Accuracy is paramount in measurement systems. High sensitivity pressure sensors achieve a level of precision that is often unmatched by traditional sensors. They operate by detecting minute changes in pressure, allowing for fine-grained data collection. This ability to capture small fluctuations is vital in sectors where safety and performance are critical, such as aerospace and medical devices.
Applications that benefit from enhanced accuracy include:
- Blood pressure monitoring systems
- Altitude sensing in aircraft
- Fuel pressure monitoring in automotive systems
With the ability to deliver detailed and precise readings, these sensors reduce the margin for error, enhancing overall system reliability. Users can trust that the data gathered will support critical decision-making processes, making these sensors valuable assets across various applications.
Increased Measurement Range
Another key advantage is the increased measurement range of high sensitivity pressure sensors. These sensors can operate effectively over a wider range of pressures compared to standard devices. This flexibility is important because different applications may require measurements under varying conditions. For instance, in industrial machinery, the need to measure both extremely low and high pressures is commonplace.
- Factors contributing to this increased range include:
- Advanced sensor designs that accommodate diverse pressure levels
- Utilization of high-quality materials that withstand extreme conditions
- Enhanced signal processing capabilities that improve response time and sensitivity
The capability to measure across such a range ensures that users do not need to invest in multiple sensor types, simplifying operations and reducing costs.
Improved Stability
Stability over time is a crucial characteristic of any sensor. High sensitivity pressure sensors are designed to maintain precision even under varying environmental conditions. Factors such as temperature fluctuations, humidity, and mechanical vibrations often influence sensor performance. High sensitivity designs minimize these impacts, ensuring consistent performance.
Features that enhance stability include:
- Robust housing that protects internal components from external factors
- Advanced algorithms that filter out noise from measurements
- Selection of materials that resist fatigue and wear over time
Reliability is essential for users who need consistent readings over long periods without frequent recalibration. High sensitivity pressure sensors meet this requirement effectively, making them reliable partners in critical systems.
"Investing in high sensitivity pressure sensors leads to improved measurement accuracy, a broader operational range, and greater long-term stability, resulting in enhanced performance across various applications."
Challenges in Pressure Sensor Technology
High sensitivity pressure sensors play an essential role in numerous industries, yet they face specific challenges that can affect their reliability and accuracy. Understanding these challenges provides insight into the current limitations of sensor technology and guides ongoing research towards innovative solutions. Addressing these obstacles not only improves sensor performance but also broadens their application scope.
Environmental Influences
Environmental factors significantly affect the performance of pressure sensors. Variations in temperature, humidity, and atmospheric pressure can lead to measurement inaccuracies. For instance, extreme temperatures can alter the materials used in sensors, changing their mechanical properties and diminishing sensitivity. Additionally, exposure to corrosive substances in industrial environments can degrade sensor materials over time, impacting their longevity and reliability.
To mitigate these influences, manufacturers often employ protective coatings or select materials with enhanced resistance. However, doing so can increase costs and complicate the design process. Understanding the extent of environmental influences is crucial for designers who need to ensure that their devices remain accurate under various conditions.
Calibration Difficulties
Calibration is a critical step in maintaining the accuracy of pressure sensors. However, the calibration process can be fraught with difficulties. In an ideal scenario, pressure sensors should be calibrated in the environment where they will be employed to ensure optimal accuracy. Yet, this is often not feasible, particularly in applications like aerospace or deep-sea exploration.
Moreover, the need for regular recalibration poses challenges. Factors such as sensor drift, changes in reference pressure, or variations in sensor materials can necessitate frequent recalibrations, increasing operational costs and downtime. Therefore, achieving a balance between reliability and ease of calibration is essential—and complex.
As demand for high-sensitivity measurements grows, addressing these calibration difficulties is paramount for future advancements in sensor technology.
"Challenges in pressure sensor technology are pivotal in shaping the future of measurement science."
The ongoing efforts to reduce the impact of environmental influences and streamline calibration processes are foundational to enhancing the reliability of high sensitivity pressure sensors. Continuous research and development can potentially unlock advancements that overcome these hurdles effectively.
Future Directions in Sensor Development
The landscape of high sensitivity pressure sensors continues to evolve, driven by technological advancements and the increasing demand for precision in measurements. Understanding future directions in sensor development is crucial for leveraging potential benefits and addressing issues in various applications. This section covers prominent trends that are reshaping the field, particularly focusing on the integration of Internet of Things (IoT) technologies and advancements in miniaturization. These aspects are vital for improving performance, enhancing user experience, and expanding market reach.
Integrating IoT Technologies
The integration of IoT technologies into pressure sensors is transforming how data is collected and analyzed. IoT sensors can transmit real-time data to centralized systems, facilitating faster decision-making and increasing operational efficiency. With cloud computing, vast amounts of data from pressure sensors can be analyzed to identify patterns, improve accuracy, and even predict failures. This predictive maintenance can significantly reduce downtime in industries such as aerospace and automotive.
Moreover, IoT integration allows for remote monitoring, which can enhance safety in hazardous environments. Sensor networks can be deployed in locations that are difficult to access, and data can be monitored from a distance, ensuring timely responses to anomalies.
- Before implementing IoT technologies, considerations must include:
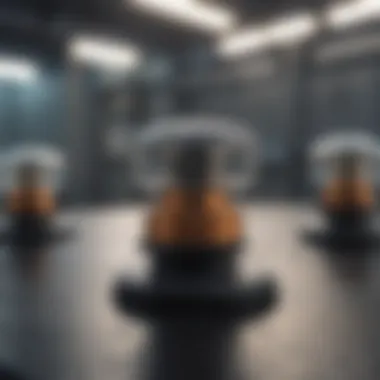
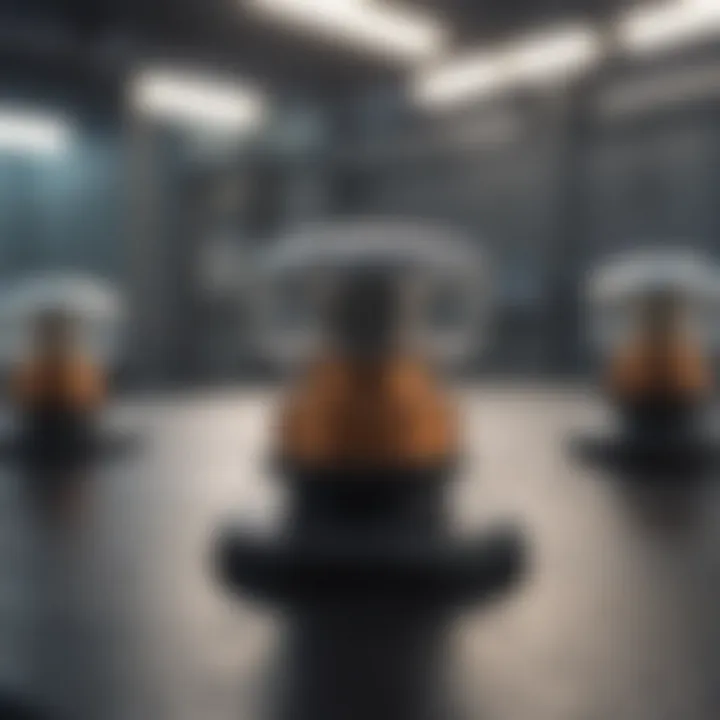
- Data security measures to protect sensitive information.
- Standardization of communication protocols.
- Compatibility with existing infrastructure.
Advancements in Miniaturization
Miniaturization in sensor technology is a notable trend bringing significant advantages. Smaller sensors can be placed in confined spaces or embedded in devices without affecting their functionality. This opens up new applications, particularly in medical devices where size constraints are paramount. Flexible pressure sensors, which can be incorporated into wearable technology, are emerging as a significant area of interest.
The benefits of advancements in miniaturization include:
- Cost Reduction: Smaller sensors often entail lower material costs and streamlined manufacturing processes.
- Increased Versatility: Miniature sensors can be more easily integrated into various technologies and platforms.
- Enhanced Performance: Smaller sensors may react faster to changes in pressure, providing more accurate readings in dynamic environments.
Innovation in fabrication technologies, such as micro-electromechanical systems (MEMS), plays a crucial role in this miniaturization trend. The ability to produce complex sensor structures with high precision allows engineers to design sensors that meet the growing requirements of modern applications.
"As technology progresses, the integration of IoT with miniaturized sensors is set to redefine industry standards, making systems more efficient and responsive."
Comparative Analysis of Pressure Sensors
The comparative analysis of pressure sensors provides critical insights into their performance capabilities. This analysis is important for various stakeholders in the field, including engineers, researchers, and industry practitioners, as it directly influences decision-making processes when selecting the appropriate sensor for specific applications. By evaluating elements like accuracy, cost, and durability, one can discern which sensor type best caters to application needs.
Accuracy and Precision
Accuracy and precision are often intertwined concepts that play a significant role in the functionality of pressure sensors. Accuracy refers to how close a measured value is to the true value, while precision indicates the consistency of repeated measurements. High sensitivity pressure sensors are designed with notable improvements in these areas to meet rigorous industry standards.
Accurate sensors can lead to better system performance as they ensure reliable data collection and are crucial in fields like aerospace and medical devices. For example, in aerospace applications, an accurate pressure sensor can prevent critical failures by offering real-time data on altitude and cabin pressure. This distinction between accuracy and precision is vital; users must understand that a device can be highly precise but not accurate if it is improperly calibrated. Therefore, engineers often seek sensors that provide both features while ensuring minimal drift in readings over time.
Cost Effectiveness
Cost effectiveness is a crucial aspect when selecting pressure sensors. While high sensitivity sensors generally come with higher initial costs compared to standard models, their long-term benefits can outweigh these expenses. For industries where continuous monitoring is paramount, investing in high-quality sensors can yield significant cost savings.
These savings stem from reduced maintenance costs, fewer replacement needs, and improved operational efficiency. The analysis should also consider the total lifecycle cost, which includes installation, calibration, and operational expenses. A detailed cost-benefit analysis can help in making an informed decision that aligns budgetary constraints with performance needs.
Durability and Longevity
Durability and longevity are essential attributes that determine the viability of pressure sensors for long-term usage. In many applications, pressure sensors must withstand harsh environmental conditions, such as extreme temperatures, humidity, and corrosive substances. High sensitivity pressure sensors are often built with resilient materials that enhance their resistance to these factors, ensuring sustained performance despite challenging conditions.
A sensor's longevity reduces the frequency of replacements and the associated costs of downtime. When selecting a pressure sensor, it is crucial to evaluate its mechanical and thermal durability based on the specific operating conditions it will face. To this end, conducting thorough testing and reviewing engineering data can provide valuable insights into a sensor's expected service life.
"Choosing the right pressure sensor relies on understanding the balance between technical performance and economic factors."
In summary, a comparative analysis of pressure sensors highlights important considerations such as accuracy, cost effectiveness, and durability. Understanding these elements allows professionals to make informed choices that enhance system reliability and operational efficiency.
Impact of Research Innovations
Research innovations play a pivotal role in the advancement of high sensitivity pressure sensors. This section emphasizes the substantial impact that continuous research and development have on the enhancement of sensor technology. Innovations can lead to improved accuracy, increased sensitivity, and expanded applications across various industries. As technology evolves, sensors are becoming more integral in diverse fields, where precision measurements are crucial topics.
Recent Breakthroughs
Several recent breakthroughs in sensor technology have caught the attention of researchers and industries alike. One notable innovation is the development of nanostructured materials. These materials have shown an exceptionally high sensitivity to pressure changes, making them ideal for delicate measurement tasks. Some advancements include:
- Microelectromechanical Systems (MEMS): These have been miniaturized successfully, allowing for the creation of compact and high-performance pressure sensors.
- Flexible Sensors: Research has led to the creation of pressure sensors that can be integrated into wearable technology. These provide real-time monitoring of various variables, such as body pressure and environmental conditions.
- Wireless Communication Capabilities: The integration of wireless technology allows for remote monitoring and data acquisition, significantly enhancing the usability of pressure sensors in field applications.
These breakthroughs represent only a fraction of the ongoing research efforts aimed at improving high sensitivity pressure sensors. The field is dynamic and evolving rapidly.
The Role of Multidisciplinary Approaches
To achieve significant advancements in pressure sensor technology, multidisciplinary approaches are essential. Collaborations between physicists, engineers, material scientists, and computer technologists foster innovative solutions that no single discipline could achieve alone. Such collaborations may involve:
- Material Science and Engineering: Understanding the properties of new materials leads to the development of sensors that perform exceptionally well under various conditions.
- Data Science and Machine Learning: These disciplines assist in interpreting sensor data, enabling predictive analytics that enhance overall sensor functionalities.
- Computer Engineering: The integration of software solutions with hardware developments maximizes the usability of the sensors in real-world applications.
"Innovations in pressure sensor technology are often propelled by collaboration across disciplines, resulting in smarter and more efficient devices."
This synergy not only propels the technology forward but also opens avenues for new applications previously deemed unlikely or impossible. Emerging domains and creative environments push researchers to address complex problems, ultimately enhancing the capabilities of high sensitivity pressure sensors.
Culmination
The conclusion is a crucial component of this article as it encapsulates the essence of high sensitivity pressure sensors. This article sheds light on the various aspects, including the operating principles, types, materials, applications, and emerging trends in this field. It serves to remind readers of the relevance of these sensors in modern technology and industry. By reinforcing the key points raised throughout the article, the conclusion provides clarity and emphasizes the benefits these sensors bring to numerous sectors.
Summary of Findings
This section highlights several key insights regarding high sensitivity pressure sensors:
- Defining Characteristics: High sensitivity pressure sensors are defined by their ability to measure small pressure changes accurately.
- Technological Impact: They significantly enhance the precision of measurements in critical applications, especially in aerospace and medical devices.
- Material Variations: The materials used—such as silicon-based materials and composite materials—play a vital role in determining the performance and sensitivity of these sensors.
- Apparent Advantages: These sensors exhibit many advantages, including enhanced accuracy, improved stability, and increased measurement range.
- Challenges Addressed: Despite their benefits, challenges such as environmental influences and calibration difficulties remain critical areas of focus for future developments.
Overall, the findings illustrate the transformative role of high sensitivity pressure sensors across various industries.
Future Research Directions
Looking ahead, several vital research directions merit attention:
- Integration with IoT: There is a growing need for research into integrating high sensitivity pressure sensors with Internet of Things (IoT) technology. This integration could offer real-time data collection and enhanced monitoring capabilities.
- Miniaturization Trends: Future advancements must focus on miniaturizing sensor designs. Smaller sensors can be utilized in more compact and demanding applications, such as wearables and small-scale devices.
- Advanced Materials: Investigating new materials that enhance sensor performance is vital. Development may lead to better reliability and functionality in harsher environments.
- Machine Learning Applications: Utilizing machine learning algorithms can enhance the accuracy of data interpretation from sensors, leading to better predictive analytics.
In summary, the future of high sensitivity pressure sensors looks promising, with significant potential for technological advancements to address existing challenges.