Exploring Magnetic Particle Detectors and Their Applications
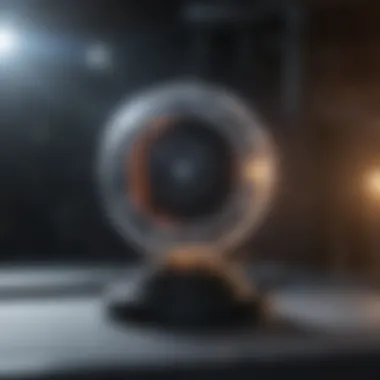
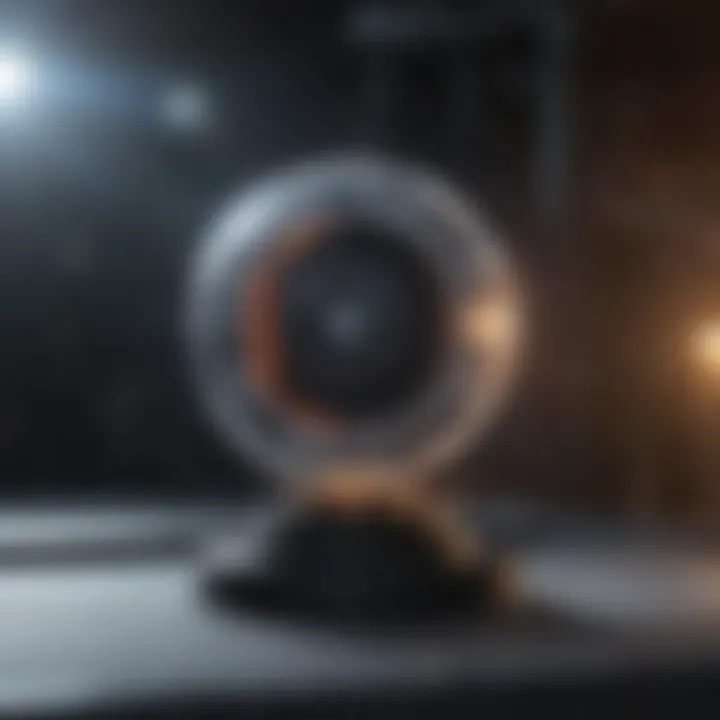
Intro
The field of material science continually evolves, striving for better methods to identify and address defects in various substances. Among these methods, magnetic particle detection stands out for its effectiveness in visualizing flaws, particularly in ferromagnetic materials. This method leverages the principles of magnetism to enhance our understanding of material integrity and safety across multiple industries like aerospace, automotive, and construction.
Utilizing finely powdered iron or similar substances, this detection technique can expose even the minutest crack or surface imperfection. Not only does it play a critical role in quality assurance, but it also serves as a preventive measure, addressing potential failures before they develop into catastrophic issues. With a growing emphasis on safety and efficiency, understanding how these detectors work, their historical context, and where they're headed in the future is vital for industry professionals, researchers, and students alike.
Research Background
Overview of the Scientific Problem Addressed
The challenge of accurately detecting material flaws isn't new. Traditionally, methods like visual inspection or ultrasonic testing have been employed. Yet, these techniques often fall short when faced with complex geometries or inaccessible locations. The scientific problem lies in finding a reliable, efficient, and non-destructive method that can uncover subsurface defects effectively. Magnetic particle detection rises to this occasion, providing a solution that combines simplicity with precision.
Historical Context and Previous Studies
The initial burst of interest in magnetic particle testing dates back to World War II, when the demand for structural integrity became crucial for military equipment. Researchers started to refine techniques focused on magnetism, which led to significant advancements in synthetic powders and the application of magnetic fields. Over the subsequent decades, developments in magnetic particle technology have paralleled innovations in related fields like materials science and electronics.
Numerous studies have explored the variations in magnetic field adaptability and powder formulations. Historical analysis highlights studies like those by H. G. Hoh, who in the late 1950s, presented critical data on effective magnetic field configurations for improved inspection results. Furthermore, investigations into particle sizes and coating materials paved the way for modern practices in detection techniques, ensuring that current methodologies benefit from lessons learned over decades.
Findings and Discussion
Key Results of the Research
Recent advancements in magnetic particle detectors have shown promising improvements in sensitivity and resolution. Testing methods and materials utilized now allow for greater flexibility in application across various industries. Understanding how different formulations of magnetic powders affect visibility under magnetic fields has been pivotal, showing variations in particle performance in detecting superficial versus subsurface defects.
Interpretation of the Findings
The key findings from contemporary research suggest that advancements in magnetic particle detection not only enhance defect detection but also improve operational efficiency. By integrating modern imaging technology with traditional methods, industries can achieve more thorough inspections in less time. The studies indicate a need for continued innovation, particularly in automated systems that can streamline the detection workflow while retaining accuracy.
"As industries push for higher safety standards and lower production costs, the integration of novel technologies with established practices will likely lead to transformative improvements in magnetic particle detection techniques."
In summary, magnetic particle detectors are not just a routine part of material testing but an evolving technology that responds to the ever-increasing demands of various sectors. Understanding its roots, advancements, and future potential serves as a beacon for ongoing research and development in this critical field.
Prelims to Magnetic Particle Detection
Magnetic particle detection is a specialized method used primarily in non-destructive testing to identify surface and slightly subsurface defects in ferromagnetic materials. Understanding this technique is vital for various industries where safety and integrity of components cannot be compromised. Effective detection methods can prevent catastrophic failures, leading to significant savings in repair costs and ensuring safety in operational environments. The exploration into magnetic particle detection goes beyond its utility; it unveils a rich background steeped in scientific discovery and practical application.
Historical Context
To comprehend the significance of magnetic particle detection today, one must traverse back to its origins. The groundwork for this technology can be traced to the early 20th century when researchers began to uncover the properties of magnetism. One pivotal moment was in World War II, when the need for rapid and reliable inspection methods became crucial in manufacturing processes for fighter planes and military vehicles. During this period, magnetic particle inspection was developed as a way to ensure mechanical integrity without damaging the materials.
The simple yet effective principle behind detecting flaws using magnetic fields proved essential. As ferromagnetic materials are magnetized, imperfections in these materials distort the magnetic field, allowing particles to cluster and reveal imperfections. Over the decades, this technique has evolved, integrating advancements in materials science, physics, and engineering practices.
Importance in Non-Destructive Testing
Magnetic particle detection holds a prominent position in the realm of non-destructive testing (NDT). This method excels in its capacity to detect minute cracks, inclusions, and other anomalies that could lead to component failure under stress. The non-invasive nature of this process means that components can be inspected without any damage—an essential requirement for components in vital sectors such as aerospace and automotive industries.
The process is not just about spotting defects; it’s about instilling confidence in the materials used in critical applications. For instance, imagine the repercussions of failing airplane parts or compromised bridges. Magnetic particle detectors help avoid such disasters by providing a reliable line of defense that maintains regulatory standards.
"Investing in methods of non-destructive testing not only saves costs long-term but is a foundational aspect of quality assurance in engineering."
Furthermore, the versatility of magnetic particle detectors makes them widely applicable across various domains—from ensuring the resilience of railway tracks to validating manufacturing quality in automotive parts. As industries lean into aggressive standards for quality and safety, understanding the underlying principles of magnetic particle detection is not merely useful; it is essential for professionals responsible for maintaining the integrity of structures and components.
In essence, the historical development and the profound impact of magnetic particle detection in non-destructive testing underscore its relevance in today’s engineering landscape. The continued scientific progress and the refinement of methods promise to enhance this invaluable tool further, breathing life into sectors where precision and safety cannot be compromised.
Fundamental Concepts of Magnetism
Understanding the fundamental principles of magnetism is a cornerstone for comprehending how magnetic particle detectors function. These concepts not only provide the basis for analyzing materials but also showcase the interplay between magnetic fields and various substances. Grasping these principles empowers professionals in fields such as engineering, quality control, and materials science to leverage magnetic particle detection for flaw identification.
Basic Properties of Magnetic Fields
Magnetic fields are generated by moving electric charges, usually in the form of electric current through a conductor. The strength and direction of these fields are denoted by the magnetic field vector, often represented by symbols like B. This vector is crucial in understanding how magnetic fields interact with ferromagnetic and paramagnetic materials, leading to distinct behaviors in various applications.
Key characteristics of magnetic fields include:
- Field lines: These imaginary lines illustrate the direction of the magnetic force, where denser areas indicate stronger fields.
- Polarity: Every magnet has a north and south pole, and understanding this polarity is essential for manipulating magnetic fields effectively.
- Strength: The strength of a magnetic field diminishes with distance from its source, a principle important in positioning detection equipment closer to the inspection target.
The interaction of magnetic fields with different materials leads to varied applications in magnetic particle inspection. This knowledge not only enhances testing accuracy but also aids in optimizing inspection techniques for different materials.

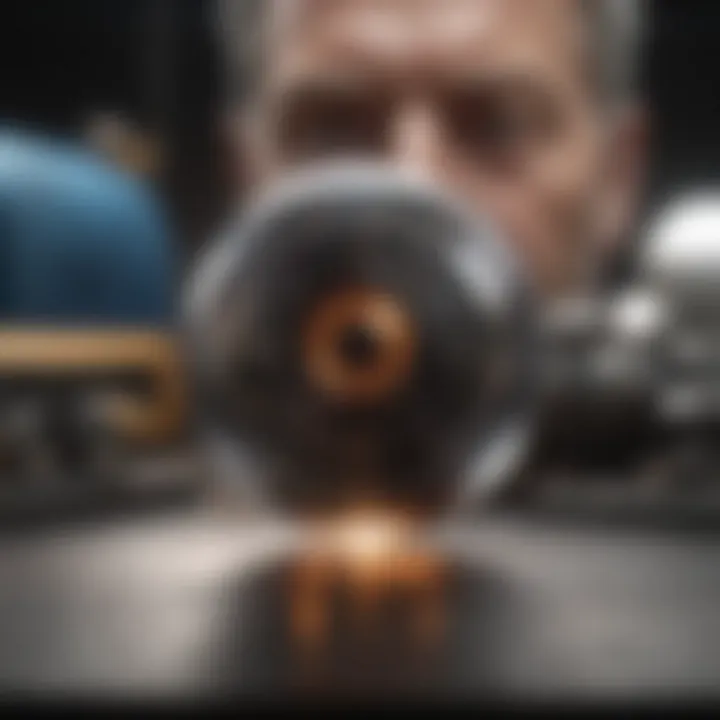
Interaction of Magnetic Fields with Materials
The interaction between magnetic fields and materials is a fascinating area of study, particularly in non-destructive testing methods. Materials like iron and cobalt exhibit strong magnetic properties, meaning they can be magnetized easily and retain their magnetism longer. In contrast, materials classified as paramagnetic, such as aluminum, exhibit a weak response and quickly lose their magnetic properties after the external field is removed.
Here are some crucial points regarding how magnetic fields interact with materials:
- Ferromagnetism: This is a phenomenon observed in materials that can be strongly magnetized. When exposed to an external magnetic field, these materials align their magnetic domains, making them particularly useful in magnetic particle inspection.
- Curie Temperature: Each ferromagnetic material has a Curie temperature at which it loses its magnetic properties. Understanding this temperature is vital for certain applications, especially in high-temperature environments.
- Permeability: This property denotes how easily a material can be magnetized and how well it can conduct magnetic lines of force. Materials with high permeability are preferred in magnetic particle detectors, leading to more efficient flaw detection.
"The world of magnetism is an intricate dance of forces, revealing the hidden flaws in materials that could otherwise lead to catastrophic failures."
The interaction of magnetic fields with various materials builds the foundation for effective magnetic particle detection techniques. Knowledge of these concepts lends itself to superior decision-making in practical applications, fortifying the safety and reliability of structures across diverse industries.
Mechanics of Magnetic Particle Detectors
Understanding the mechanics of magnetic particle detectors is crucial for anyone involved in inspection technologies. These devices are designed to reveal imperfections in materials, making them invaluable across varied industries. They operate on fundamental principles of magnetism, using magnetic fields to attract small particles that either cluster at imperfections or form visible indications of flaws.
The effectiveness of a magnetic particle detector relies heavily on its operating principles, the type of magnetic particles employed, and the overall system design. By grasping these aspects, one gains insight into how best to implement this technology for maximum efficiency and reliability.
Operating Principles
At the heart of magnetic particle detection lies a straightforward yet powerful operating principle: the interaction between applied magnetic fields and ferromagnetic or paramagnetic particles. When a magnetic field is introduced to a test specimen, the field interacts with any discrepancies in material integrity, generating invisible or visible indicators of flaws.
This principle typically unfolds in these step-wise scenarios:
- Magnetization: The first step is to magnetize the test item. This can be achieved using yokes, coils, or other magnetizing equipment. The method depends on the material type and the environmental conditions.
- Application of Magnetic Particles: Once magnetized, magnetic particles – either fluorescent or non-fluorescent – are applied over the surface. These particles are usually suspended in a liquid, allowing even coverage.
- Detection of Indications: Any cracks or surface discontinuities will create a leakage field that attracts particles. In fluorescent systems, ultraviolet light illuminates these accumulations, making them visible for further evaluation.
Through these steps, defects that could lead to catastrophic failures or major safety issues can be identified.
Types of Magnetic Particles Used
In the realm of magnetic particle detectors, there are essentially two primary categories of particles, each serving distinct roles based on their properties: ferromagnetic and paramagnetic particles.
Ferromagnetic Particles
Ferromagnetic particles are often the go-to choice in magnetic particle inspection. Their key characteristic lies in their ability to become strongly magnetized in the presence of an external magnetic field. This leads to their effective accumulation near surface defects, enhancing the likelihood of identification.
These particles possess a magical affinity for forming distinctive signals that raise the alarm on any cracks or voids. A noteworthy feature of ferromagnetic particles is that they can be utilized in either dry or wet methods, providing flexibility based on the inspection environment. However, they do come with some disadvantages – for instance, they can potentially be difficult to clean up once the inspection is complete, which can result in contamination or batching issues.
Paramagnetic Particles
On the other hand, paramagnetic particles, while less frequently used, play a significant role in specialized applications. Their notable trait is their ability to be weakly attracted to magnetic fields. While they do not cluster as strongly as ferromagnetic particles, their unique behavior enables them to be employed where minimal magnetic influence is required.
This characteristic makes paramagnetic particles useful in cases where ferromagnetic particles might interfere with the analysis or change the magnetic landscape of the specimen being inspected. Yet, their utilization is often viewed as more niche, as the visual indicators created may not be as pronounced, limiting their effectiveness in broader applications.
Understanding the different particle types helps in crafting effective inspection plans tailored to the specific requirements of an industry. Thus, comprehending the mechanics behind these detectors allows engineers and technicians to make informed decisions, resulting in better safety outcomes.
Techniques of Magnetic Particle Inspection
Understanding techniques of magnetic particle inspection is crucial for anyone involved in non-destructive testing. These techniques not only enhance the efficiency of detecting flaws in materials but also ensure the safety and reliability of a variety of structures, ranging from bridges to aircraft components. Selection of the proper technique is often dictated by the specific requirements of the inspection task and the characteristics of the materials being examined.
Fluorescent vs. Non-Fluorescent Techniques
When it comes to magnetic particle inspection, a key distinction lies between fluorescent and non-fluorescent techniques. Fluorescent magnetic particles, when exposed to ultraviolet light, fluoresce bright yellow-green, allowing for enhanced visibility of defects. This method is especially useful under low-light conditions, where traditional methods might miss smaller cracks or surface inconsistencies. In contrast, non-fluorescent methods may use colored particles which do not require UV light, making them suitable for larger areas or when UV equipment isn’t available.
Both types of techniques offer distinct advantages:
- Fluorescent Techniques:
- Non-Fluorescent Techniques:
- Higher sensitivity to surface defects.
- Clear visibility during inspection under UV light.
- Allows for inspections in low-light environments.
- Easier to handle and often requires less specialized equipment.
- Can be used for larger inspections where fine detail isn’t the main concern.
"The choice between fluorescent and non-fluorescent methods often depends on the specific situation at hand, ranging from the nature of the material to the inspection environment."
Wet vs. Dry Methods
Another critical aspect of magnetic particle inspection involves the wet vs. dry methods. Wet methods utilize magnetic particles suspended in a liquid carrier, actively coating the surface of the material being tested. This approach allows for better coverage and greater sensitivity in detecting flaws. It’s particularly useful in inspecting complex shapes or large surfaces. The specific liquid being used is also engineered to help in the magnetization process and improve the flow of the magnetic particles, making this method quite efficient.

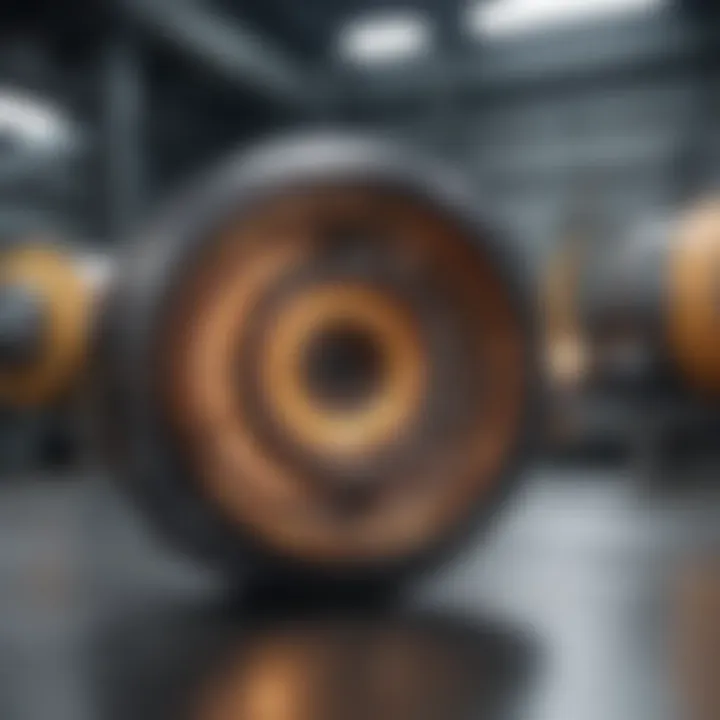
On the other hand, dry methods involve applying magnetic particles in powder form directly to the magnetic field or surface of the component. This method can be less messy and is often easier to clean up after the inspection is complete. However, it might not provide as thorough coverage on rough or irregular surfaces, possibly leading to some defects being overlooked.
Advantages of Wet and Dry Methods:
- Wet Methods:
- Dry Methods:
- Enhanced sensitivity and coverage.
- Suitable for intricate shapes or components.
- Particles can flow easily into cracks.
- Less cleanup required post-inspection.
- Simplicity and ease of use in some contexts.
- Lower risk of loss of particles compared to wet methods.
Equipment Used in Magnetic Particle Detection
In the realm of non-destructive testing, the equipment used in magnetic particle detection plays a pivotal role in ensuring the accuracy and effectiveness of this inspection technique. Without suitable tools, the reliability of fault detection diminishes, potentially leading to serious safety concerns, especially in critical industries like aerospace or automotive manufacturing. Each piece of equipment adds a layer of precision necessary for identifying surface and near-surface flaws in ferromagnetic materials.
Magnetic Yokes and Prods
Magnetic yokes are fundamental pieces of equipment in the magnetic particle detection process. These devices generate a magnetic field that is essential for detecting defects.
- Portability: One of the strong suits of magnetic yokes is their portability. Technicians can easily carry them to various job sites, making inspections straightforward.
- Versatility: Magnetic yokes can be used in a variety of orientations and on multiple materials, proving their adaptability in diverse scenarios.
- Power Supply: Many yokes operate on battery, which enhances their usability in locations where access to electrical outlets is limited.
Moreover, prods are likewise used to create a magnetic field at a specific area of the material being inspected. They are particularly beneficial for areas that might be difficult to reach with larger equipment. These tools are crucial not just for their effectiveness, but for the speed with which they can deliver results in real-world scenarios.
Magnetizing Equipment
The process of magnetization itself is crucial. This equipment ensures the creation of a strong and stable magnetic field necessary for magnetizing the test object effectively. There are various types of magnetizing equipment:
- AC Magnetizers: Typically used for detecting surface defects, these create an alternating magnetic field that is practical for lighter materials.
- DC Magnetizers: Offering steadiness and a stronger field, DC magnetizers are more suited for detecting deeper flaws. This equipment must be chosen based on the material's characteristics to maximize detection efficiency.
- Coil Magnetizers: These generate a strong field through coils wrapped around the item, ensuring a uniform magnetic field distribution, vital for thorough inspections.
Ultimately, the selection of magnetizing equipment directly influences the results of magnetic particle inspections. Proper setup and operation can make or break an inspection.
Development of Automated Systems
As industries continue to evolve, so do the technologies employed within them. Automated systems in magnetic particle detection have emerged as game-changers. These systems provide several benefits:
- Consistency: Automated setups offer consistent results, regardless of operator skill level. Automation reduces human error, leading to more reliable inspections and fewer false positives or negatives.
- Efficiency: Time savings can be monumental; automated systems can perform the magnetizing and inspection process far quicker than manual methods.
- Data Integration: Modern systems often include software that tracks defects, generating reports effortlessly. This data is invaluable for quality control and can be integrated into existing production data systems for comprehensive analysis.
Noteworthy advancements include robotic arms equipped with magnetic particle detection capabilities. These systems can navigate complex geometries often faced in industrial components, making it easier to ensure thorough inspections. It's evident that as the technology progresses, so too does the efficacy of magnetic particle detection techniques.
"The introduction of automated magnetic particle systems signifies a leap into the future of non-destructive testing by marrying technology with precision."
In short, the equipment used in magnetic particle detection is layered, each piece adding its own value. From the fundamental magnetic yokes and prods to sophisticated automated systems, the advancements in this field underscore the importance of precise, efficient, and reliable detection methods.
Practical Applications of Magnetic Particle Detectors
Magnetic particle detectors play a pivotal role in various industries, ensuring the integrity and safety of materials. Their practical applications are not only significant but fundamental to maintaining high standards in manufacturing and quality assurance processes. Using these detectors allows for the identification of surface and near-surface discontinuities in conductive materials, which can lead to catastrophic failures if not addressed. In essence, magnetic particle inspection acts as a robust first line of defense against potential flaws that may jeopardize structures and systems.
Aerospace Industry
Within the aerospace industry, the stakes are particularly high. Components in aircraft and spacecraft are subjected to immense stresses and must operate reliably under extreme conditions. Magnetic particle inspection is invaluable here for several reasons:
- Safety First: The safety of passengers and crew relies on the structural integrity of aircraft. Regular inspections using magnetic particle detectors help identify cracks and other defects that could compromise safety.
- Material Diversity: Aerospace components may be made from a variety of materials, including aluminum and titanium alloys, which are often challenging to inspect due to coatings and surface treatments. Magnetic particles can penetrate these superficial layers, uncovering hidden flaws.
- Regulatory Compliance: Aerospace is a heavily regulated industry. Maintaining compliance with safety standards is critical, and the use of magnetic particle detection assists in meeting these rigorous requirements.
Automotive Manufacturing
In automotive manufacturing, the pressure to produce reliable and efficient vehicles has never been greater. Here are the critical areas where magnetic particle detectors shine:
- Quality Assurance: In a world where recalls can be pricey and damaging to a brand’s reputation, magnetic particle inspection serves as a fundamental tool in quality assurance processes, identifying defects in engine components and chassis.
- Material Reliability: Automotive parts often undergo extensive stress, especially in high-performance or high-demand vehicles. Identifying flaws early prevents failures that could lead to accidents or costly repairs.
- Cost-Effectiveness: Compared to other inspection methods, magnetic particle detection is often more cost-effective, saving manufacturers money while ensuring they do not compromise on quality.
Other Industrial Applications
Beyond the aerospace and automotive sectors, magnetic particle detectors are indispensable across numerous other industries:
- Energy Sector: In the energy sector, particularly in nuclear and geothermal power plants, magnetic particle inspection helps ensure the integrity of critical components such as pressure vessels and pipelines. Any small defect here can lead to severe consequences.
- Railway Maintenance: Rail systems rely heavily on magnetic particle detection to find issues in track components, ensuring that no cracks or defects go unnoticed that could endanger the safety of trains and their passengers.
- Manufacturing: From heavy machinery to consumer products, manufacturers use magnetic particle inspection to safeguard against defects in metals and alloys, ensuring a high level of quality control in their production lines.
"The use of magnetic particle detectors manifests a proactive approach toward quality control, emphasizing prevention rather than remediation."
In summary, the practical applications of magnetic particle detectors span a vast range of industries, acting as a bulwark against defective materials that could jeopardize safety and performance. By investing in reliable inspection technologies, businesses can enhance their operational efficacies while upholding their commitment to safety and quality.
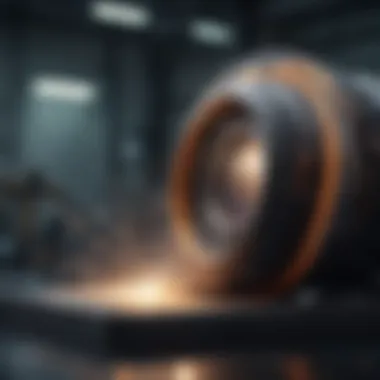
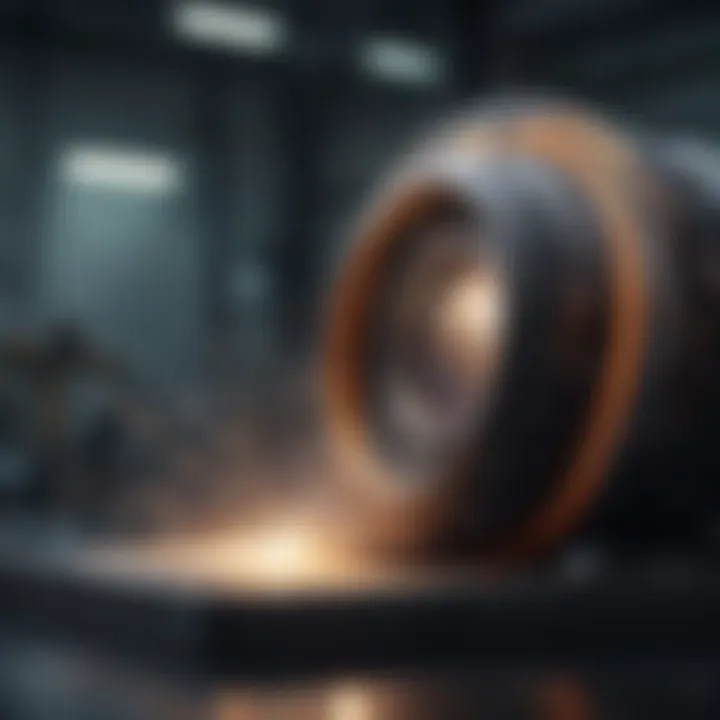
Challenges in Magnetic Particle Detection
When it comes to the functionality of magnetic particle detectors, understanding the challenges involved is crucially important. These detectors play a significant role in non-destructive testing, ensuring material integrity and safety across numerous industries. However, working with magnetic particles presents its own set of obstacles that can influence the effectiveness and accuracy of inspections. Addressing these challenges not only enhances the performance of detection methods but also safeguards against potential failures in critical applications.
Detection Limits and Material Conditions
One of the primary challenges in magnetic particle detection is the detection limits, which refer to the smallest defect size that can be effectively identified. The ability to detect fine cracks or fissures is heavily affected by the material conditions of the item being inspected. Different types of metals and alloys respond variably to magnetic fields, which can complicate the detection process. For instance, ferromagnetic materials exhibit strong magnetization, while non-ferromagnetic materials offer less detectable signals.
Furthermore, the skin depth—how deep the magnetic field will effectively penetrate—can vary depending on the frequency of the magnetic field applied, which might limit detection efficacy. This means that the geometry, shape, and surface conditions can significantly impact outcomes. If surface contaminants are present, such as oil or paint, they can mask indications of defects, making it all the more challenging to achieve reliable results. Therefore, preparatory measures are critical before inspection, ensuring surfaces are clean and well-suited for the process.
"Consistent surface preparation is often the unsung hero in ensuring reliable non-destructive test results, especially when using magnetic particle detection methods."
Safety and Environmental Concerns
Another layer of complexity arises from safety and environmental concerns related to magnetic particle inspection. The chemicals used in the magnetic particle testing processes can pose health risks, including skin irritation or potential respiratory issues when aerosols are generated. Many magnetic particle suspensions contain solvents that can be hazardous to both users and the environment.
It is paramount for industries to adhere to safety regulations and implement proper protective measures, such as personal protective equipment (PPE) and adequate ventilation systems. Furthermore, as regulatory bodies grow stringent regarding environmental standards, manufacturers are urged to explore eco-friendly alternatives. This shift involves investigating water-based magnetic suspensions that maintain effectiveness while reducing environmental impact.
In summary, tackling these challenges in magnetic particle detection requires a multifaceted approach. Recognizing detection limits according to material conditions and addressing safety and environmental concerns are essential for advancing magnetic particle detection technology. Clearly, ongoing research and innovations are pivotal to overcome these hurdles, ensuring that magnetic particle detectors continue to meet the demands of modern industrial applications.
Advancements in Magnetic Particle Detection Technology
The realm of magnetic particle detection technology is not stagnant; it is an evolving field that has seen significant advancements in recent years. These developments not only amplify the capabilities of existing systems but also open new avenues for solving complex challenges in various industries. Understanding these technological innovations is crucial for the stakeholders across sectors, as they enhance detection efficacy and broaden application scopes.
Innovations in Detection Methods
Recent strides in detection methods deserve attention for how they impact the accuracy and speed of defect detection. Innovative approaches include the development of advanced magnetic particle formulations that exhibit enhanced visibility, allowing for finer evaluations of surface defects.
- Ultra-fine Ferromagnetic Particles: These are engineered for improved sensitivity, enabling detection of hairline fractures that previous systems might miss.
- Dual-mode Detection: Some systems can switch between fluorescent and non-fluorescent techniques based on the inspection requirements, offering flexibility while minimizing the need for extensive equipment changes.
- Automated Systems: The automation of the inspection process with robotics ensures a consistent application of magnetic particles, reducing the risk of human error and improving reproducibility of results.
These innovations pave the way for advanced inspections across critical industries such as aerospace and automotive, highlighting the significance of precision in safety-critical environments.
Integration with Digital Technologies
The synergy between magnetic particle detection and digital technologies has been a game changer. Using digital capabilities brings forth several pivotal advantages such as data management and analysis. With enhanced connectivity, real-time monitoring becomes possible, allowing for immediate corrective actions if abnormalities are detected.
- Data Analytics: Integration of AI-driven analytics tools enables predictive maintenance by analyzing patterns from historical inspection data. This can lead to not only timely interventions but also reduced downtime.
- Cloud Solutions: Storing inspection data in cloud systems allows stakeholders to access and analyze data from anywhere, facilitating collaboration among teams and fostering quicker decision-making processes.
- Software Development: Advanced software solutions equipped with machine learning algorithms can process vast data quickly and create comprehensive reports, highlighting defects and suggesting corrective actions with remarkable accuracy.
This interplay between magnetic particle detection and digital tools cultivates an environment where precision meets efficiency, setting new industry standards and improving the overall safety landscape.
In summary, advancements in magnetic particle detection technology, highlighted by innovations in detection methods and their integration with digital technologies, illustrate a forward momentum in the field. It aids not only in addressing current challenges but also in preemptively tackling issues through enhanced capabilities and efficiency.
Future Trends in Magnetic Particle Detection
The exploration of future trends in magnetic particle detection is more than just a casual glance ahead; it fundamentally shapes how industries will approach non-destructive testing in the coming years. Understanding these trends not only equips professionals with insights into potential advancements but also highlights the evolving nature of technology in this field. Alongside technological evolution, the industry is witnessing transformative shifts in the integration of artificial intelligence and machine learning, which promote greater efficiency and accuracy. It is crucial for stakeholders in various sectors to stay abreast of these developments, as they can lead to marked improvements in safety measures and operational capabilities.
Emerging Research Directions
The realm of magnetic particle detection is ripe for innovative research that can drastically alter its landscape. Researchers are focused on a few key areas:
- Advanced Materials: Experimentation with new types of magnetic particles, like nano-sized ferromagnetic compounds, could lead to greater sensitivity in detecting fine flaws or defects. This improvement can greatly benefit industries like aerospace and automotive, where detection standards are exceedingly high.
- Improved Algorithms: The development of smarter algorithms geared towards better interpretation of inspection data is gaining ground. These algorithms focus on enhancing the accuracy of defect recognition, which not only speeds up the inspection process but also reduces the chances of false positives.
- Hybrid Techniques: Combining techniques from magnetic particle detection with methods such as ultrasonics or eddy current testing is a promising path. Such integration could enhance detection capabilities, resulting in a broader spectrum of flaws being identified, subsequently leading to better material safety practices.
Engagement in these research avenues is key, as they provide the tools to redefine and enhance the efficacy of magnetic particle detectors in practical scenarios.
Potential for Standardization
As industries increasingly adopt magnetic particle detection technologies, there lies a pressing need for standardization across different sectors. The following points illustrate the importance of establishing uniform guidelines:
- Consistency in Quality: Standardization can ensure all magnetic particle detection methods adhere to regulatory requirements, thus providing a baseline for quality assurance. Without these standards, discrepancies in detection methods can lead to unsafe practices and detrimental outcomes.
- Training and Education: Unified standards allow for more effective training protocols for technicians and inspectors. When everyone operates under the same guidelines, it guarantees a level of competency and consistency in results.
- Cross-Industry Collaboration: Standardization cultivates a common language among professionals from various sectors. This collaborative environment fosters sharing of best practices and innovations, ultimately pushing the boundaries of what magnetic particle detection can achieve.
In summary, the prospects for magnetic particle detection are encouraging, with emerging research and the potential for standardization promising to elevate industry practices, providing safer environments and minimizing loss from material failures.
Culmination
In this article, the focus on magnetic particle detection signifies more than just a technical assessment; it illustrates the pivotal role these detectors play across various industries. From aerospace to automotive, the ability to effectively spot imperfections in materials can not only save time but also safeguard against catastrophic failures. Ensuring that equipment operates under optimal conditions requires robust and reliable methods of inspection, which magnetic particle detectors provide.
Summary of Key Points
- Historical Relevance: Magnetic particle detection has evolved significantly, rooted in a rich historical context that sheds light on its ongoing significance in modern materials inspection.
- Fundamentals of Magnetism: Understanding the core principles of magnetism is crucial for grasping how these detectors function. From the basic properties of magnetic fields to their interaction with different materials, grasping these details is key.
- Mechanics and Techniques: The operational principles and various techniques—from fluorescent vs. non-fluorescent to wet vs. dry methods—outline the flexibility and adaptability of magnetic particle detectors in diverse situations.
- Equipment Varieties: The discussion on various equipment illustrates the array of tools available to inspectors, from simple magnetic yokes to sophisticated automated systems, which cater to specific inspection needs.
- Practical Applications: By examining real-world applications in several industries, it becomes evident how these detection methods enhance quality control processes and ensure structural integrity.
- Challenges and Advancements: Recognizing the challenges faced—like material conditions and safety concerns—as well as the recent advancements in technology, provides insight into both the obstacles and solutions in the industry today.
- Future Trends: Emerging research directions inspire optimism regarding the future capabilities of magnetic particle detection, potentially leading to standardization and enhanced effectiveness in inspections.
Final Thoughts on Magnetic Particle Detection
In closing, magnetic particle detection stands as a cornerstone in non-destructive testing methodologies. The continuous evolution and exploration in this field not only reinforce its relevance but also highlight the importance of investing in research and technology. As industries continue to seek better inspection methods, the significance of magnetic particle detectors is likely to grow, proving invaluable in promoting safety and reliability. Understanding the nuances of this technique equips professionals with the knowledge needed to implement effective and efficient testing strategies, ultimately leading to safer operational practices in numerous sectors.