Exploring DLP Printing: Principles and Applications
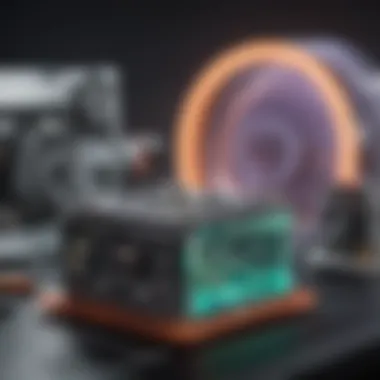
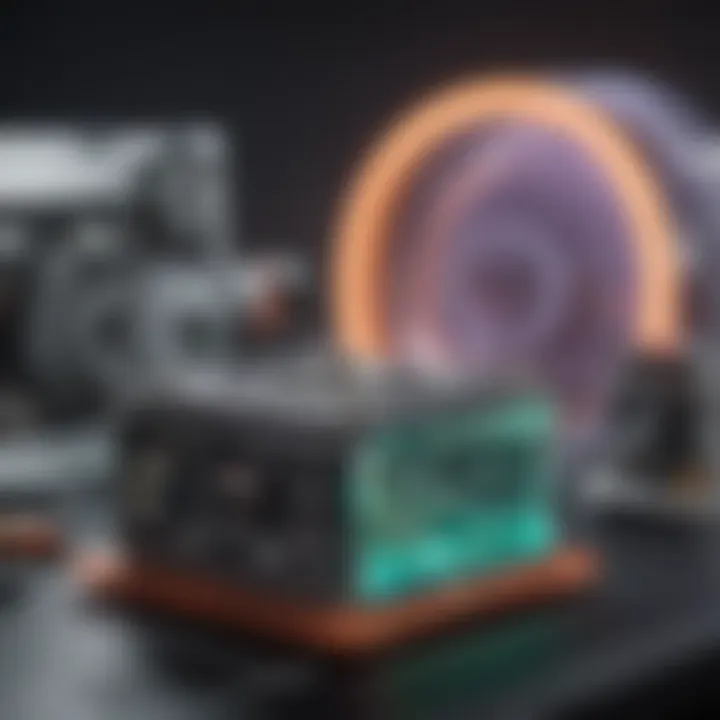
Intro
Digital Light Processing (DLP) printing represents a notable advancement in the field of additive manufacturing. Originally developed for cinema projection, it has found significant relevance in various sectors, particularly in 3D printing. DLP technology operates by projecting light onto a photosensitive resin, solidifying it layer by layer. This article aims to provide a nuanced examination of the principles, applications, and implications of DLP printing across an array of industries.
DLP printing leverages sophisticated optics and digital displays to convert digital images into tangible products. Its efficiency and precision make it a compelling choice in fields such as healthcare, where accuracy is critical, and manufacturing, which increasingly demands rapid prototyping and customization.
In this narrative, we will investigate the fundamental principles that underpin DLP technology, analyze its various applications, articulate its advantages and challenges, and highlight future trends that may shape its evolution. Through this comprehensive exploration, we hope to furnish researchers, educators, and industry professionals with a thorough understanding of DLP printing's landscape.
Foreword to DLP Printing
Digital Light Processing (DLP) printing represents a significant technological advancement in the field of additive manufacturing. Understanding the principles behind this method is vital for various industries looking to adopt innovative manufacturing techniques. This section offers insights into what DLP printing is, its foundational importance, and the impact it has across different sectors. In exploring DLP, one discovers its benefits, limitations, and the evolving nature of the technology amid growing industrial demands.
Definition and Overview
DLP printing is an additive manufacturing technique that utilizes digital light technology to cure photopolymer resins layer by layer. By projecting a digital light image of each layer onto a vat of liquid resin, DLP printers can create highly detailed parts with intricate geometries. The key to DLP's effectiveness lies in its ability to solidify resin quickly using a light source, such as a digital projector. This process not only enhances the speed of production but also improves the overall accuracy of the printed objects compared to traditional methods.
One of the primary advantages of DLP printing is its capacity for producing smooth surface finishes and fine details. It is highly suitable for industries that require precision, such as dental and medical applications. However, understanding its operational parameters, including material types and environmental conditions, is crucial for optimal results.
Brief History of DLP Technology
The concept of Digital Light Processing was first developed by Texas Instruments in the 1980s for projection systems, transforming how visual images were displayed. Initially used in projectors, DLP technology made its way into the realm of 3D printing in the early 2000s. The technology was adapted for rapid prototyping, marking a shift from traditional manufacturing techniques.
Over the years, DLP printing has gained traction and popularity, especially with the advent of affordable desktop models. This has allowed small businesses and individual creators to harness its capabilities for diverse applications, from jewelry design to engineering components. As DLP technology continues to evolve, innovations in materials and processes are expected to expand its applications, making it a crucial component in the future of manufacturing.
Technical Principles of DLP Printing
Understanding the technical principles of Digital Light Processing (DLP) printing is crucial for grasping how this technology effectively produces high-quality 3D objects. This section discusses various aspects, including the underlying mechanisms, materials utilized, and light source technologies. Each element contributes significantly to the overall efficiency and effectiveness of DLP printing in various applications.
Core Mechanisms of DLP
DLP printing relies on a unique process that uses light to cure photopolymer resins. In this process, a digital light projector displays images layer by layer onto a vat filled with resin. As the light selectively polymerizes the liquid, a solid layer forms at the bottom of the vat. This mechanism enables rapid layer-by-layer construction of intricate designs. The precision of the light projection plays a vital role in determining the accuracy and detail of the final product.
Materials Used in DLP Printing
The choice of materials is vital for DLP printing. Primarily, photopolymer resins are used due to their reactivity to UV light. These resins can vary significantly, affecting properties such as strength, flexibility, and finish quality. Some resins are designed for specific applications, such as brittle materials for detailed modeling or tougher compounds for functional prototypes. Moreover, the adaptability of materials allows DLP printing to cater to distinct industry needs extensively, from healthcare to manufacturing.
Light Source Technologies
Light source technology in DLP printing can be categorized primarily into Digital Micromirror Devices and various light source options such as LEDs and lasers. The selection of the light source impacts the speed, resolution, and overall performance of the printing process.
Digital Micromirror Devices
Digital Micromirror Devices (DMDs) are central to the operation of DLP technology. They consist of thousands or even millions of tiny mirrors that tilt to reflect light. The ability to control these mirrors with precision makes DMDs highly effective for projecting detailed images onto the resin. One key characteristic of DMDs is their capacity to achieve high resolutions for printing. This makes them a favored option in industries where detail is paramount. DMDs provide benefits in terms of speed and efficiency due to their digital nature, allowing rapid image processing and minimization of downtime during the print cycle. However, their complexity and associated costs can limit accessibility for smaller operations.
LED vs. Laser Light Sources
When comparing LED and laser light sources, each has unique attributes affecting their suitability for different applications. LEDs are more common in DLP printers due to their availability and cost-effectiveness. They provide adequate light intensity and have a long lifespan. Their major advantage is low operational costs and slower temperature changes, which reduces maintenance requirements.
In contrast, laser light sources offer greater precision and intensity. This results in faster printing times and potentially finer details. However, lasers can create more heat, necessitating additional cooling systems. The higher initial costs associated with laser systems can be a barrier for many users.
In summary, the technical principles of DLP printing are essential for understanding how this technology operates and serves various industries. The interplay between the core mechanisms, materials, and light source technologies creates a robust framework for producing high-quality 3D printed objects efficiently. Through careful selection and optimization, DLP printing continues to advance, unlocking new possibilities in digital fabrication.
Comparative Analysis: DLP vs. Other Printing Technologies
In the landscape of additive manufacturing, it is crucial to understand how Digital Light Processing (DLP) printing stacks up against other printing technologies. This comparison enables industry professionals, researchers, and students to make informed decisions regarding the selection of a printing method based on application, material, and cost considerations.
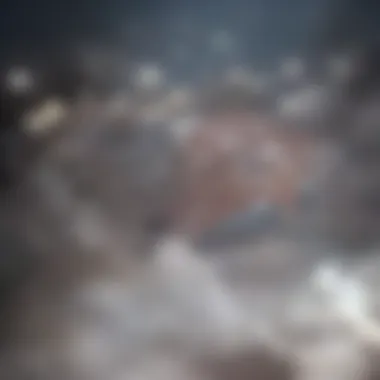
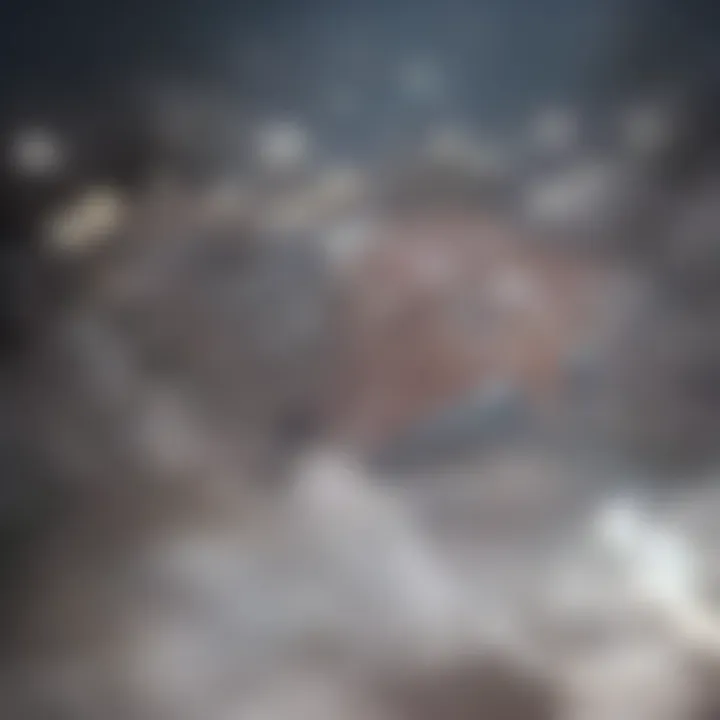
FDM Printing
Fused Deposition Modeling (FDM) is perhaps the most established and widely adopted 3D printing technology. It operates by extruding thermoplastic filament, layer by layer, to create a three-dimensional object.
Key Characteristics of FDM Printing:
- Material Variety: FDM supports a wide range of thermoplastics, including PLA, ABS, and PETG. This versatility makes it suitable for diverse applications.
- Cost-Effectiveness: FDM printers generally have lower initial costs compared to DLP systems. The consumable materials are also affordable, making it a popular choice for prototyping and producing functional parts.
- Speed: While FDM can produce larger parts relatively quickly, it typically takes more time to achieve the same level of detail offered by DLP.
SLA Printing
Stereolithography (SLA) is another prominent additive manufacturing technique. It uses a laser to cure liquid resin, forming solid objects. DLP and SLA are more similar in their light-based curing processes, yet there are distinct differences.
Advantages of SLA Printing:
- Higher Resolution: SLA is known for producing models with superior detail and smooth surface finishes. This is especially beneficial in industries like jewelry and dental.
- Material Properties: SLA resins can provide specific mechanical and aesthetic properties, such as flexibility or transparency, which can be tailored for specific applications.
- Post-Processing Needs: SLA typically requires more intensive post-processing, including washing and curing, to achieve optimal results. This can affect time and labor costs.
SLS Printing
Selective Laser Sintering (SLS) is a powder-based 3D printing method that uses a laser to sinter powdered material into solid structures. This technique is predominantly used with polymers and metals.
Benefits of SLS Printing:
- No Support Structures Required: SLS can produce complex geometries without the need for support materials, which simplifies post-processing and reduces waste.
- Material Range: SLS has a broader scope of materials, including nylon and other thermoplastics, expanding its utility in various industrial applications.
- Mechanical Strength: SLS parts generally exhibit higher strength and durability than those produced through DLP or FDM, making it suitable for functional applications.
Each of these printing technologies serves distinct needs and industries. DLP printing excels in speed and surface quality when compared to FDM, yet it may face challenges concerning material limitations. In contrast, DLP and SLA share a close relationship, but DLP offers faster production rates, while SLA provides finer resolutions. Understanding these distinctions allows industries to harness the full potential of additive manufacturing technologies tailored to their specific requirements.
Applications of DLP Technology
Digital Light Processing (DLP) technology manifests its significance across various sectors, reshaping how industries approach their challenges. The ability of DLP printing to create highly intricate and precise models makes it a valuable tool in diverse fields such as healthcare, manufacturing, and entertainment. This section will explore the various applications of DLP technology, focusing on its unique benefits and considerations that underline its relevance in contemporary practices.
Healthcare Industry
Prototyping Medical Devices
Prototyping medical devices is a vital aspect of healthcare innovation. DLP printing allows for rapid prototyping, which significantly reduces the time it takes to bring concepts to life. The key characteristic of DLP in this context is its ability to produce complex geometries with high accuracy. This precision is essential for testing and validating device designs before mass production. DLPβs layer-by-layer fabrication works well for small, detailed components such as surgical tools or implants.
One unique feature of using DLP in medical prototyping is the range of biocompatible materials available, enhancing safety in medical applications. However, a challenge lies in the limited availability of some specialized materials, potentially restricting design options.
Dental Applications
In the dental field, DLP printing presents significant advancements. The main focus of DLP here is on creating dental models, prosthetics, and aligners. This approach provides a high level of detail, making it a beneficial choice for creating custom solutions for patients.
A noteworthy characteristic of dental DLP applications is the speed at which dental appliances can be produced. Traditional dental manufacturing often involves lengthy processes, whereas DLP allows for quicker turnaround. However, the reliance on specific printing materials can limit flexibility, as not all materials may provide the desired strength or aesthetics for every dental solution.
Manufacturing Sector
Rapid Prototyping
Rapid prototyping within the manufacturing sector serves as a cornerstone for developing new products. DLP technology enables manufacturers to produce prototypes quickly and with high fidelity. This speed is a distinct advantage, allowing for faster iterations during the design process.
The capacity for rapid prototyping fosters innovation, giving companies the ability to test ideas and refine them before committing to full-scale production. Nevertheless, one limitation is the cost of high-quality DLP printers and materials, which may deter smaller firms from utilizing this technology extensively.
Consumer Products
In the realm of consumer products, DLP technology allows for the design of intricate and customized goods, ranging from jewelry to personalized gadgets. The primary benefit is the customization capability, which meets specific consumer demands effectively.

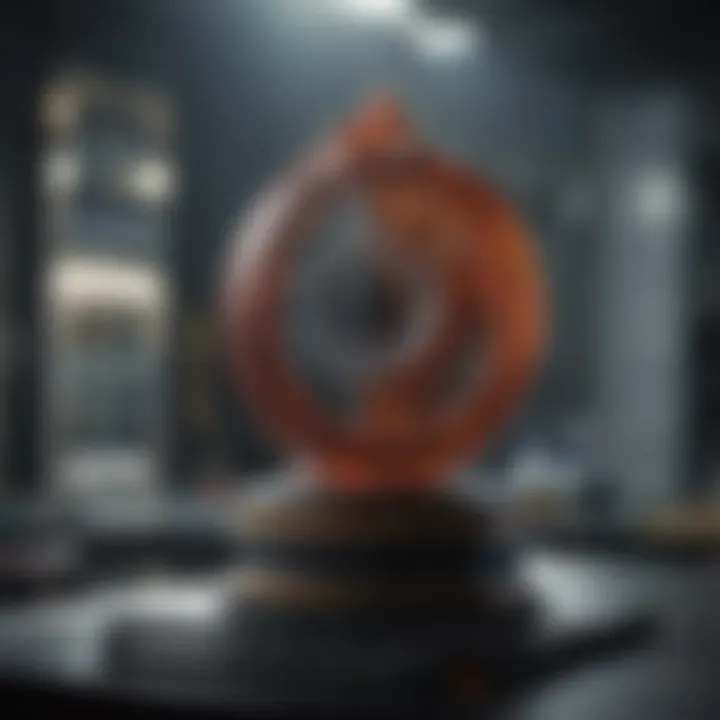
A unique aspect of DLP in consumer product manufacturing is the material versatility. This technology can work with various resin types, allowing designers to create both functional and aesthetically pleasing items. However, the operational costs associated with maintaining DLP printers and sourcing materials may pose challenges for companies aiming to keep production costs low.
Entertainment and Gaming
Model Making
DLP printing has revolutionized model making within the entertainment industry. This technology offers a method to produce highly detailed miniatures that are crucial for visual storytelling. The great precision of DLP ensures that even the smallest details are captured, making it a popular choice for filmmakers and game developers.
A key characteristic of model making with DLP is the ability to produce complex designs rapidly. This efficiency can be crucial when deadlines are tight. However, limitations regarding the size of printed models can require scaling or assembly, which adds complexity to projects.
Character Development
In character development for video games and animations, DLP technology plays a significant role. The accuracy and detail achievable with DLP facilitate the creation of prototypes that help in visualizing character designs. This approach aids creators in communicating concepts more effectively.
A unique feature in character development is the rapid iteration capacity. Teams can evaluate and adjust designs quickly, leading to a refined final product. Nevertheless, challenges include the reliance on specific printing materials that may not meet all design requirements.
The applications of DLP technology showcase its versatility and importance across sectors, highlighting how it can address specific challenges while offering opportunities for innovation.
Advantages of DLP Printing
Digital Light Processing (DLP) printing brings several advantages to the forefront of 3D printing technologies. Understanding these benefits is vital for professionals and researchers who seek to leverage this technology for various applications. DLP printing appeals to multiple sectors due to its unique combination of speed, surface quality, and cost-effectiveness. Each of these elements plays a significant role in how DLP technology is perceived and utilized in real-world scenarios.
Speed and Efficiency
One of the standout features of DLP printing is its remarkable speed. Unlike traditional printing methods which build objects layer by layer, DLP technology cures an entire layer of resin at once. This means that the time taken to produce a model can be significantly reduced. For example, a complex model that would take hours to print using Fused Deposition Modeling (FDM) can often be realized in minutes with DLP.
Efficiency in DLP printing is not limited to speed alone. The entire process is highly automated. After setting up the printer and preparing the design file, minimal human intervention is needed during the printing process. This automation reduces the likelihood of human error, ensuring a more reliable output.
Surface Quality and Detail
In terms of surface quality, DLP printing excels. The resolution of DLP printers allows for fine details that would be challenging to achieve with other methods. The quality of the output is attributable to the high-resolution light sources used, which create sharp and well-defined edges. This level of detail is crucial, particularly in industries like healthcare, where precision is vital for medical devices and dental applications.
Moreover, the smooth surface finish produced by DLP printers often requires less post-processing. This feature can save both time and resources in preparation for final use or further treatment.
Cost-Effectiveness
Cost-effectiveness is an essential consideration in the choice of manufacturing methods. While the initial investment in DLP technology may appear high, the operational costs can be favorable in the long run. The speed and efficiency of DLP printing translate directly into lower labor costs and reduced production times.
Additionally, the use of resins in DLP can be more economical compared to filament materials used in FDM. As a result, projects that require numerous prototypes or iterations may find DLP printing to be a more financially viable option.
Challenges in DLP Printing
Digital Light Processing (DLP) printing presents several challenges that impact its adoption and effectiveness across various industries. Understanding these challenges is crucial for researchers and industry players looking to optimize the technology and address its limitations. By focusing on material limitations, post-processing requirements, and operational costs, we can glean insights that assist in developing strategies for enhancing DLP printing capabilities and efficiency.
Material Limitations
One significant hurdle in DLP printing is the material limitations associated with the resin types available. Unlike other printing technologies, DLP relies heavily on photopolymers that need to cure under UV light. The properties of these resins can affect the mechanical strength, flexibility, and durability of the final printed product.
Some standard resins may not perform well for specific applications, particularly in industries demanding high strength or resistance to fatigue. For example, while standard resins work fine for prototyping, they might fail in end-use applications in aerospace or automotive sectors. Additionally, the limited range of colored materials in DLP compared to other techniques can restrict creativity and variability in design. This limitation necessitates ongoing research and development of new photopolymer blends that offer enhanced properties tailored to specific industrial needs.
Post-Processing Requirements
Post-processing is another notable challenge in DLP printing. Once printing is complete, parts typically require cleaning and curing to achieve desired mechanical properties and finish. This additional step is not only time-consuming but also resource-intensive. Cleaning involves removing excess resin, often needing the use of solvents or specialized machines, which adds complexity to the workflow.
Moreover, improper post-processing can lead to poor surface quality, which can affect the aesthetic appeal and functionality of the printed objects. Some users may overlook this aspect resulting in substandard outputs. The industry needs simplified processes and better solutions to streamline post-processing and improve overall productivity.
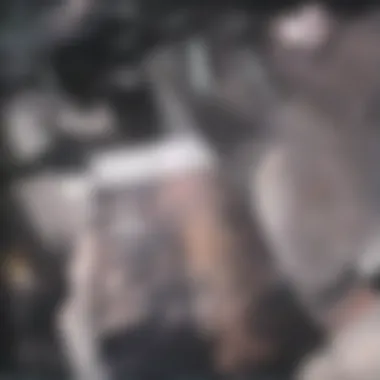
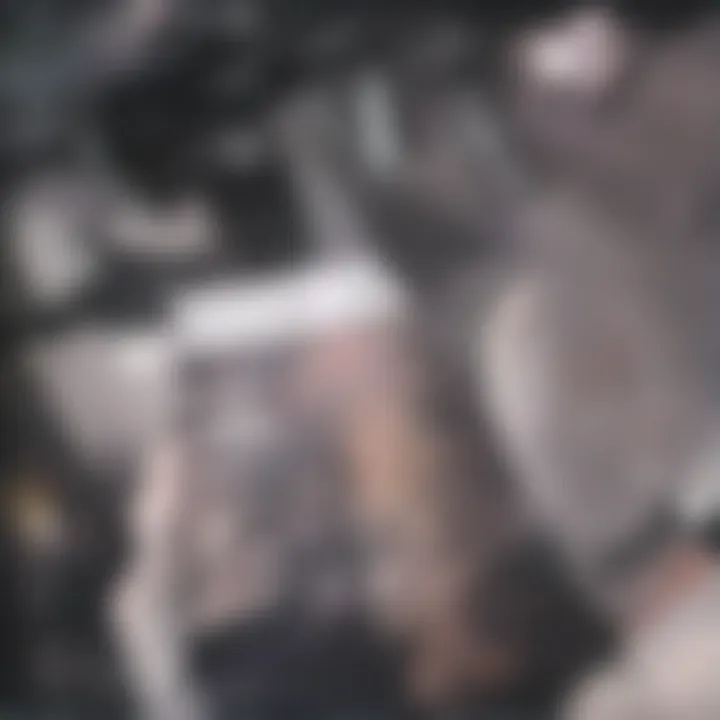
Operational Costs
Operational costs represent an ongoing challenge within the DLP printing landscape. While the initial investment in DLP printers may be lower than that of some other printing technologies, costs can quickly accumulate over time. This expense often arises from material usage and maintenance needs.
Photopolymer resins can be costly, particularly for specialty materials required in specific applications. Additionally, the machinery may incur ongoing operational costs, including maintenance, technical support, and training for personnel.
"Addressing the challenges in DLP printing unlocks its full potential for diverse applications and enhances its competitiveness in the market."
Understanding and tackling these obstacles is pivotal for the industry to fully realize the benefits of DLP printing.
Future Trends in DLP Technology
The exploration of future trends in DLP technology is essential for understanding its trajectory and potential impact on various industries. As Digital Light Processing continues to evolve, new advancements are emerging that expand its capabilities and applications. This section will focus on important elements such as the advancements in material science and the integration of DLP printing with other technologies, particularly hybrid manufacturing and automation. Understanding these trends provides context for why DLP printing remains a relevant and innovative method in digital fabrication.
Advancements in Material Science
Material science plays a crucial role in the effectiveness of DLP printing. Advances in materials used for printing not only enhance the functionalities of printed objects but also broaden the potential applications of DLP technology. For instance, new photopolymer resins are being developed that offer improved mechanical properties, such as greater durability and flexibility. This is particularly significant for sectors like healthcare, where biocompatible materials can lead to breakthroughs in medical device prototyping and custom implants.
Additionally, researchers are exploring new composite materials that combine multiple properties, enabling the production of complex structures that were previously difficult to achieve. This includes materials with embedded electronics or responsive elements, pushing the boundaries of what can be manufactured with DLP technology.
Integration with Other Technologies
Integration plays a vital role in the evolution of DLP printing. By collaborating with other technologies, DLP can enhance productivity and expand its scope of application.
Hybrid Manufacturing
Hybrid manufacturing combines additive and subtractive processes, creating a more versatile approach to production. The integration with DLP printing allows for intricate and detailed builds that can be further refined through traditional machining methods. One key characteristic of hybrid manufacturing is its ability to produce complex geometries that are not feasible with either method alone. It is a beneficial choice because it minimizes material waste and optimizes design freedom.
However, hybrid manufacturing also faces challenges, such as the need for specialized equipment and skilled operators. The unique feature of this approach is its capability to merge the best of both worlds, bolstering efficiency while achieving high-quality output. Different industries can leverage these advantages, particularly in rapid prototyping and low-volume production, where flexibility is essential.
Automation
Automation in DLP printing is another important trend that contributes to overall efficiency and reliability. This involves the use of automated systems to streamline the DLP printing process, from material handling to post-processing tasks. A significant characteristic of automation is its potential to reduce human error and enhance consistency in production.
This technology is beneficial as it increases throughput, allowing for higher production rates without compromising quality. The unique feature of automation is its ability to operate continuous printing processes, providing significant cost savings in the long term. However, the implementation of automation requires upfront investment and appropriate training for personnel to manage more complex systems.
End
The conclusion provides a critical synthesis of the core elements discussed in the article. It serves to encapsulate the foundational principles and the significance of Digital Light Processing (DLP) technology in modern contexts, especially within 3D printing.
Through the exploration of DLPβs mechanics, materials, and applications, the article underscores both its advantages and challenges. The insights offered highlight DLP printing's speed, detail, and cost-effectiveness, showcasing its viability compared to other technologies like FDM and SLA. Moreover, addressing necessary challenges, such as material limitations and post-processing needs, allows for a balanced view.
Engaging with this conclusion brings attention to important considerations for researchers and professionals. Understanding DLP technology is increasingly essential as industries look for more efficient production methods.
"DLP printing has emerged not only as an innovative technology but also as a key player in various sectors, driving changes in production paradigms."
In the rapidly evolving domain of digital fabrication, grasping the implications of these insights offers valuable perspective on how DLP can innovate practices in manufacturing, healthcare, and entertainment.
Summary of Key Insights
The insights accumulated throughout the article reflect the versatility and potential of DLP printing technology. Some key takeaways include:
- Versatility in Applications: DLP printing is applicably diverse, making it suitable for sectors like healthcare, manufacturing, and entertainment.
- Speed and Efficiency: DLP technology stands out due to its rapid layer curing process, facilitating quicker production without compromising quality.
- Surface Detail: The capabilities of DLP printing allow for high-resolution outputs, providing intricate details that are essential for fields such as dental and prototype modeling.
- Cost Considerations: While upfront costs might be present, the efficiencies and material utilization can yield long-term savings.
These insights serve as a guide for informed decision-making in adopting DLP technology within various industries.
Final Thoughts on the Future of DLP Printing
Looking forward, the trajectory of DLP printing promises exciting avenues for development and integration. Advances in material science could lead to novel photopolymers, enhancing the scope of applications. A significant trend is toward hybrid manufacturing methods, where DLP can be integrated with other printing techniques to improve functionality and efficiency.
Automation is another area ripe for exploration. As industries work toward more streamlined operations, integrating automation with DLP processes could enhance productivity and consistency in outputs.
Undoubtedly, the future of DLP holds the potential for groundbreaking transformations in various sectors, prompting continuous investigation and innovation. By staying abreast of emerging technologies and their implications, professionals can harness DLP printing's full potential.