Understanding Industrial Scientific Calibration Gas
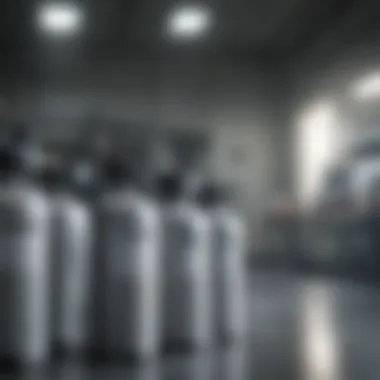
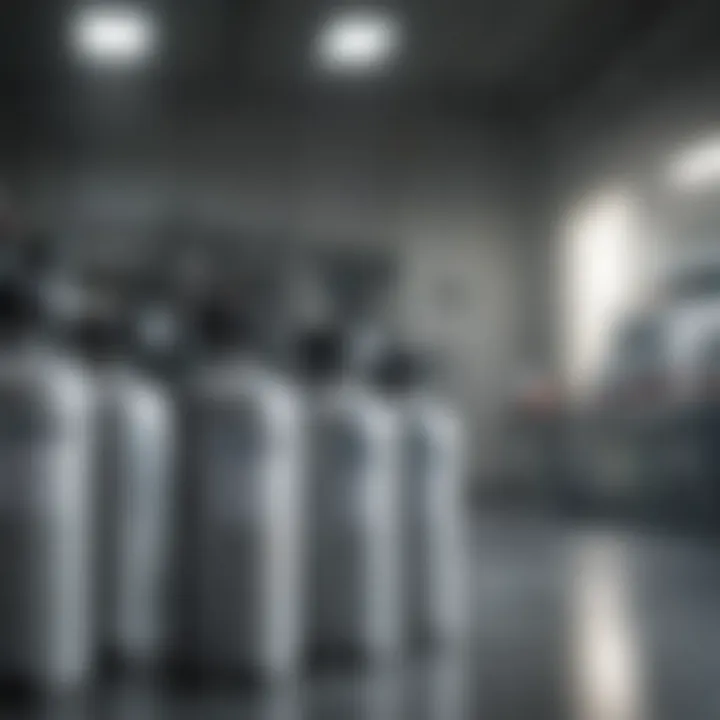
Intro
In the intricate dance of scientific inquiry, calibration gases emerge as unsung heroes, quietly ensuring precision and reliability in an array of applications. The importance of these gases stretches across industries—be it environmental monitoring, laboratory analysis, or even industrial manufacturing. Understanding what calibration gases are, their types, and their multifaceted roles in different contexts fills a crucial knowledge gap.
Calibration gas acts purely as a reference standard, helping to adjust and calibrate instruments and systems for accurate measurements. Without these gases, the very foundation of data-driven conclusions could morph into a quagmire of inaccuracies. In this exploration, we will delve deeper into the significance, types, and best practices surrounding industrial scientific calibration gases, while shining a light on advancements that continue to shape this essential resource.
Intro to Calibration Gas
Calibration gases are indispensable players in the toolkit of various scientific and industrial disciplines. Without them, precision in measurements can be as elusive as a wisp of smoke. The importance of understanding calibration gas cannot be understated; it forms the backbone of accuracy in gas detection and measurement systems.
The central role they perform is simple yet vital—ensuring that instruments that measure airborne contaminants, emissions, or other gas concentrations provide reliable results. A calibration gas serves as a reference, essentially allowing scientists and technicians to check and verify that their instruments are functioning correctly. If these gases didn't exist, the risk of failed experiments and faulty readings would loom large, resulting in potentially catastrophic consequences in fields ranging from environmental science to healthcare.
Definition and Importance
To grasp the essence of calibration gases, it helps to start with a straightforward definition. Calibration gases are specialized mixtures of gases that are used to calibrate analytical instruments. These gases hold specific concentrations of various components, acting as a benchmark for measuring the accuracy of detection devices.
Why are they important? Well, the stakes can be quite high. Accuracy in measurements affects not just experimental data but also compliance with regulations and people’s health in medical contexts. Furthermore, calibration gases are integral to assuring the quality control measures that many industries rely on. The implications stretch across sectors: if emissions testing is inaccurate, industries could severely impact the environment or face legal penalties. Ultimately, calibration gases facilitate scientific integrity and operational effectiveness.
Historical Context
The historical development of calibration gases is as intriguing as it is informative. Back in the day, gas analysis was a rudimentary practice. As industrial activities surged and environmental awareness grew, the demand for accurate gas analysis skyrocketed. The evolution of calibration gases can be traced back to the mid-20th century when more sophisticated analytical tools emerged. Scientists and engineers found themselves facing the growing complexity of emissions and environmental pollutants.
Through a series of innovative breakthroughs, calibration gases began to be standardized. By the 1960s, regulatory bodies recognized the need for specific benchmarks in gas concentrations, paving the way for the production of commercially available calibration gases. This transition was not merely a matter of convenience; it marked a paradigm shift in how industries approached compliance and environmental stewardship.
Now, as we stand on the cusp of technological advancements, calibration gases have come to form the foundation of reliable measurements, playing a crucial role in medical, industrial, and environmental applications that ensure safety and compliance.
"Calibration gases are not just tools; they are the unsung heroes of accurate measurement science."
Types of Calibration Gases
Understanding the different types of calibration gases is essential because they play a pivotal role in various scientific applications. Each category of calibration gas serves specific purposes and meets distinct regulatory needs. The choice between primary, secondary, and custom gases can significantly affect the accuracy and reliability of measurements across several industries.
Primary Calibration Gases
Primary calibration gases are the standard-bearers in the field of gas calibration. These gases come with a high degree of purity, generally at least 99.9%. Their uncompromised quality means they are typically used as reference points to calibrate other gases.
- Characteristics: These gases offer known concentrations, which are critical for ensuring measurement accuracy. They're usually produced and analyzed according to strict protocols, making them reliable benchmarks.
- Usage: For instance, in environmental monitoring, agencies often rely on primary gases to calibrate sensors for air quality measurements. Precision is non-negotiable in these scenarios, as even minor deviations can lead to significant regulatory issues.
- Industries: Primary calibration gases find utility in industries such as aerospace, pharmaceuticals, and research laboratories.
In essence, primary calibration gases act as the accurate reference that other gases aspire to emulate.
Secondary Calibration Gases
Secondary calibration gases serve an important follow-up role after primary gases. These gases typically have a lower purity level compared to primary gases, yet they are vital in practice for calibration purposes.
- Purpose: Secondary gases often replicate specific environmental conditions more closely than primary gases, which allows for a more practical calibration experience across varied technologies.
- Applications: One common usage is in industrial emissions testing, where secondary calibration gases simulate the actual pollutants in an industrial environment. This allows for more relatable and effective calibration of the measuring equipment.
- Cost-effectiveness: Although they might not carry the same level of purity, secondary gases are usually more economical. Therefore, they allow organizations to conduct regular calibration without breaking the bank.
Secondary calibration gases can be seen as the accessible choice for routine calibration tasks, striking a balance between accuracy and affordability.
Custom Calibration Gases
Custom calibration gases are tailored to meet specific needs that might not be adequately addressed by primary or secondary gases. They are created by mixing various components to achieve particular concentrations or conditions.
- Flexibility: This flexibility allows businesses and laboratories to calibrate their equipment based on unique operational requirements. If a facility needs measurements of a specific gas blend, custom calibration allows for that precise composition.
- Industries Utilized: From petrochemical plants to specialized laboratories, custom calibration gases find applications wherever specialized gas compositions are necessary. For instance, labs developing new chemical processes may prefer custom mixtures to suit their research needs.
- Considerations: When creating custom calibration gases, it’s essential to follow industry standards and ensure that the manufacturing process is transparent and reliable.
Custom calibration gases exemplify innovation and adaptability in the field, demonstrating that not all calibration needs can be satisfied with one-size-fits-all solutions.
In summary, understanding the types of calibration gases allows professionals in diverse sectors to select the most suitable options for their specific needs—whether it’s a matter of precision, cost, or customization.
Applications of Calibration Gases
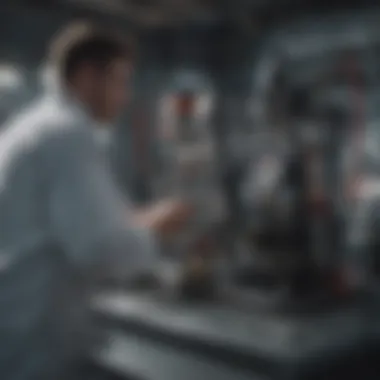
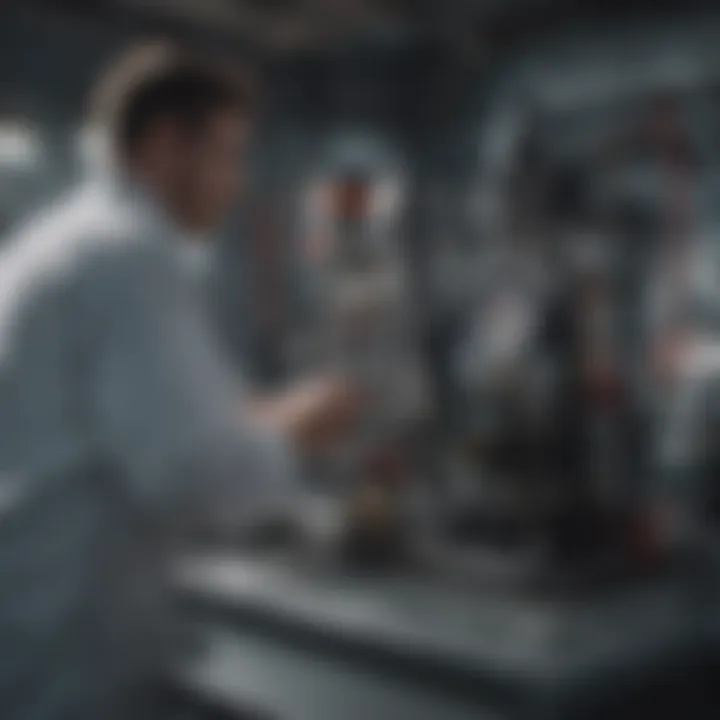
Calibration gases are not just some technical fluke; they play a pivotal role across various industries. These gases are essential in maintaining accuracy and integrity in scientific measurements, ensuring that processes ranging from environmental monitoring to medical equipment calibration are both reliable and safe. In each of these fields, the proper application of calibration gases can make the difference between compliance and chaos.
Environmental Monitoring
When it comes to environmental monitoring, calibration gases are a top priority. They help in obtaining precise measurements of air quality, enabling agencies and organizations to track pollutants and greenhouse gas emissions. For instance, consider a scenario where a team is assessing the levels of carbon dioxide in an urban area. Without accurate calibration, the data collected could skew the perception of local air quality and compromise public health policies.
- Importance: By using precisely formulated calibration gases, researchers can calibrate their instruments to detect even the minutest changes in gas concentrations. This process ensures effective environmental management and adherence to legislation.
- Benefits: Regular calibration with gases such as ozone (O3) or sulfur dioxide (SO2) boosts data accuracy. Moreover, it fosters public trust in scientific findings since decisions affecting public health hinge on reliable data.
Industrial Emissions Testing
Another critical application of calibration gases lies in industrial emissions testing. Here, it becomes vital to ensure that manufacturing processes comply with environmental regulations. Calibration gases serve as benchmarks for assessing emissions from plants, refineries, or any facility that could potentially release harmful substances into the atmosphere.
"A well-calibrated instrument is not just about getting the right number; it's about securing a better future for generations to come."
- Considerations: During emissions testing, calibration must occur under specific conditions, including temperature and pressure adjustments. Using standard reference gases allows for consistent comparisons across different tests.
- Impact: Accurate emissions readings lead to meaningful insights and prompt action regarding pollution control strategies. Compliance with emissions standards not only avoids penalties but can also significantly enhance corporate responsibility.
Medical Equipment Calibration
In the medical field, the stakes are even higher. Calibration gases are crucial in ensuring that diagnostic equipment operates correctly. For instance, in hospitals that rely on blood gas analyzers to determine a patient’s respiratory function, the precision of the gases used during calibration directly affects patient outcomes.
- Clinical Accuracy: Calibration gases can influence the results of tests for conditions like respiratory diseases or cardiovascular issues. If the calibration is off, treatments could be misdirected.
- Safety and Efficacy: Regular use of calibration gases ensures that medical equipment delivers reliable results, safeguarding patient safety. Ultimately, accurate calibrations translate into effective interventions, emphasizing the bond between technology and human health.
Regulatory Framework
The regulatory framework surrounding industrial scientific calibration gas is not just a bureaucratic necessity; it is the backbone ensuring that scientific measurements are reliable and valid across numerous applications. With calibration gases serving as benchmarks for accuracy in varying industrial fields, adherence to regulatory standards and guidelines is of paramount importance.
Ignoring these regulations could have serious ramifications. For instance, using non-compliant gases could lead to inaccurate readings, which in turn may result in faulty products, environmental damage, or even pose dangers to public health. Therefore, understanding the regulatory landscape is crucial for researchers, educators, and industry professionals alike.
Global Standards and Guidelines
Globally, various organizations set stringent standards for the use of calibration gases. The International Organization for Standardization (ISO) plays a significant role, offering guidelines like ISO 6142 and ISO 17025, which focus on the production and testing of calibration gases.
From Europe to North America and beyond, these standards aim to unify practices, ensuring that gases are produced, stored, and utilized in a manner that guarantees precision. Some key aspects of these standards include:
- Traceability: Calibration gases must be traceable to recognized primary standards. This linkage ensures consistency in measurements.
- Purity Levels: Gases should meet specific purity criteria to avoid contamination in sensitive applications.
- Documentation: Comprehensive records of gas preparation and analysis methods are essential, providing transparency in operations.
Adherence to these guidelines not only fosters good practices but also enhances the credibility and reliability of measurements across industries.
Compliance Requirements
Compliance with regulatory requirements extends beyond mere adherence to standards; it involves a systematic approach to ensure that every gas used in calibration meets the established criteria. Organizations must put in place thorough quality management systems, conducting regular audits and assessments to ensure conformance.
Some critical aspects of compliance include:
- Regular Training: Staff should receive continuous education about regulations and best practices. This instills a culture of safety and responsibility.
- Traceable Equipment: All measurement devices must be calibrated and maintained according to regulations. Ensuring that the equipment is fit for purpose can help avoid accidents and ensure accurate results.
- Documentation of Procedures: Every step in the calibration process should be documented. This transparency is essential not just for compliance, but also for training and quality assurance.
As the landscape shifts, it’s vital for stakeholders to stay ahead of changes in regulations. Emerging market trends and scientific advancements often lead to shifts in compliance requirements, so keeping abreast of these changes is essential for ongoing success in the industry.
Compliance is not merely a checkbox; it’s a commitment to accuracy and safety that echoes throughout the industry.
Best Practices for Handling Calibration Gases
When it comes to calibration gases, the importance of adhering to best practices cannot be overstated. These gases are vital in ensuring that measurements taken in various scientific and industrial applications are accurate and reliable. Whether you're monitoring environmental pollutants or calibrating delicate medical instruments, improper handling of calibration gases can lead to significant errors, potentially endangering processes and results. Therefore, understanding the nuances of gas handling is crucial for researchers, educators, and professionals alike.
Storage Guidelines
Proper storage of calibration gases plays a pivotal role in maintaining the integrity of these materials. Ideally, calibration gases should be stored in a clean, dry environment away from direct sunlight and extreme temperatures. Here are some key considerations:
- Temperature Control: Calibration gases should be kept at a stable temperature, usually between 15 °C and 25 °C. Extreme temperatures can affect gas composition.
- Regulatory Compliance: Always follow local and international regulations regarding the storage of hazardous materials. This may include using specific containers designed to withstand pressure.
- Tagging System: Use clear labels on gas cylinders indicating content, concentration, and expiration date. An efficient tagging system helps avoid mixing up gases, which is a common mistake.
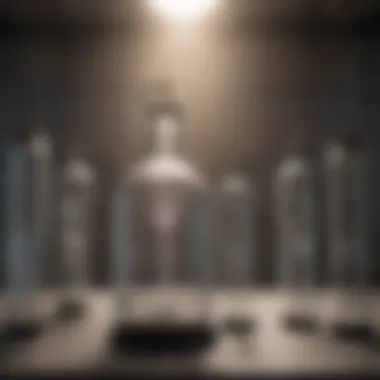
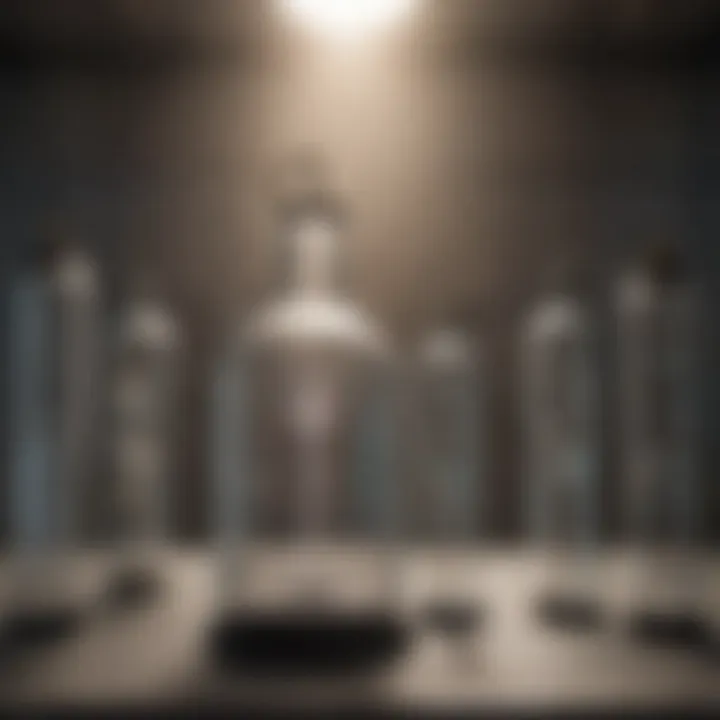
"Proper storage ensures the longevity and accuracy of calibration gases, critical for high-stakes applications."
Transport Protocols
Transporting calibration gases requires meticulous attention to detail. Mishandling during transit can compromise gas integrity. Here are essential protocols to consider:
- Cylinder Securing: Ensure gas cylinders are secured during transport to prevent rolling or tipping. This can be achieved using brackets or tie-downs.
- Use of Approved Containers: Always utilize approved transport containers to guarantee safety and security. This reduces the risk of leaks or spills.
- Documentation: Carry proper documentation detailing gas content, safety data sheets, and transport regulations. This can be crucial in case of inspections or emergencies.
Safety Measures
Safety is paramount when dealing with calibration gases, many of which can be hazardous. Implementing robust safety measures not only protects the handler but also safeguards the environment. Some crucial safety precautions include:
- Personal Protective Equipment (PPE): Use appropriate PPE such as gloves, goggles, and lab coats when handling gases. This minimizes contact with harmful chemicals.
- Ventilation: Ensure that workspaces are well-ventilated. In case of leaks, good air flow is critical in dispersing gases quickly.
- Emergency Protocols: Establish clear emergency procedures in the event of a leak or exposure. Training staff on how to respond can save lives and equipment.
By adopting these best practices, individuals and organizations can significantly minimize risks associated with calibration gases. Keeping in mind that these practices also enhance the accuracy and reliability of readings in various applications makes them all the more important. Ensuring proper handling fosters an environment of safety and precision.
Technological Advancements in Gas Calibration
As the field of industrial scientific calibration gas continues to evolve, technological advancements play a pivotal role in enhancing the accuracy and efficiency of calibration processes. These innovations are not mere bells and whistles; they fundamentally reshape how calibration is conducted, significantly impacting various industries—from environmental monitoring to medical diagnostics. Understanding these advancements is essential for professionals striving for precision and reliability in their work.
Automation in Calibration Procedures
Automation has revolutionized calibration procedures, ensuring consistency and reducing the possibility of human error. With the rise of programmable logic controllers (PLCs) and sophisticated software, calibration processes can be executed with remarkable accuracy. Automated systems not only streamline operations but also enable real-time monitoring of gas levels and calibration standards.
Consider a scenario in a laboratory setting where gas analyzers calibrated automatically instead of relying on manual input. This technology minimizes downtime and boosts productivity, allowing professionals to focus on analysis rather than tedious adjustments. Moreover, automated data collection provides a comprehensive record that can be crucial for audits and regulatory compliance.
For instance, companies that integrate automation into their calibration processes have reported a marked decrease in inconsistencies in measurements. This enhancement not only boosts the credibility of calibration results but ultimately aids in protecting public health and safety.
Innovations in Gas Analysis
Innovations in gas analysis are transforming the landscape of calibration gas usage, offering heightened sensitivity and specificity in detecting various gases. Techniques like photoacoustic spectroscopy and gas chromatography have emerged, enabling analysts to measure trace amounts of gases with unparalleled precision. This is increasingly relevant in fields such as air quality monitoring and pollutant detection, where even minute concentrations of harmful substances can have significant implications for health and safety.
"Innovative gas analysis techniques pave the way for enhanced accuracy and more effective compliance with safety regulations, which is crucial in today’s ever-stringent regulatory environment."
Furthermore, portable gas analyzers and field sampling technologies have unlocked new possibilities for on-site calibration. These advancements allow for immediate responses to environmental changes, enabling industries to adhere to regulations without excessive delays.
With these technological improvements, professionals can ensure that their calibration practices not only meet existing standards but are also adaptable to any future regulatory shifts that may arise. This adaptability is essential for maintaining a competitive edge in the industry.
In summary, the strides made in automation and gas analysis represent a significant leap forward in industrial scientific calibration practices. By embracing these changes, professionals can ensure that they are not just keeping up but leading the charge in achieving accuracy and reliability in calibration procedures.
Challenges in Calibration Gas Use
Calibration gases are undeniably pivotal in maintaining the integrity of scientific measurements across a spectrum of industries. However, their use comes with its set of challenges that can complicate the calibration process and affect outcomes. A closer examination into these challenges reveals their significance in ensuring that calibration processes are both accurate and compliant with regulations. Understanding and mitigating these challenges can significantly enhance the reliability of the data produced, fostering confidence in scientific endeavors.
Accuracy and Precision Issues
One of the foremost challenges in using calibration gases revolves around accuracy and precision. Accuracy refers to how closely a measurement aligns with the true value, while precision denotes the reproducibility of measurements under unchanged conditions. When calibration gases are improperly used or stored, the risk of errors skyrockets.
For instance, when calibration gases drift or degrade over time, the results obtained from within analytical instruments may lead to faulty understandings of the concentration levels of target gases. This situation could arise due to several factors, including:
- Environmental Conditions: High temperatures, humidity, and exposure to contaminants can compromise the integrity of calibration gases.
- Storage Medium: The material and quality of the cylinder holding the gas can impact its performance. For example, metal bottles might leach chemicals into their contents, skewing the results.
Utilizing high-quality, certified calibration gases can mitigate some of these issues, but strict adherence to best practices is also paramount.
Supply Chain Considerations
Another substantial barrier involves the supply chain surrounding calibration gases. The journey from manufacturing to end-use carries numerous risks, which, if not managed, can lead to natural bottlenecks. Factors influencing the supply chain include:
- Regulatory Compliance: Different countries have varying regulations regarding the importation and distribution of calibration gases. Navigating these complexities can lead to significant delays or even supply shortages.
- Vendors' Reliability: Not all suppliers meet the high standards necessary for calibration gases. The reliability and quality of gases can vary wildly, impacting their utility in critical applications.
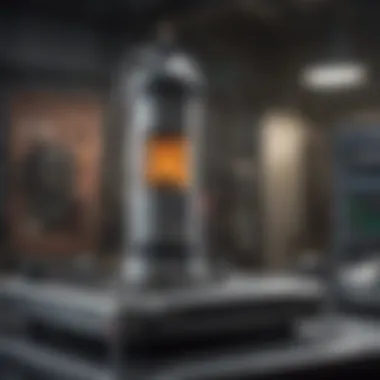
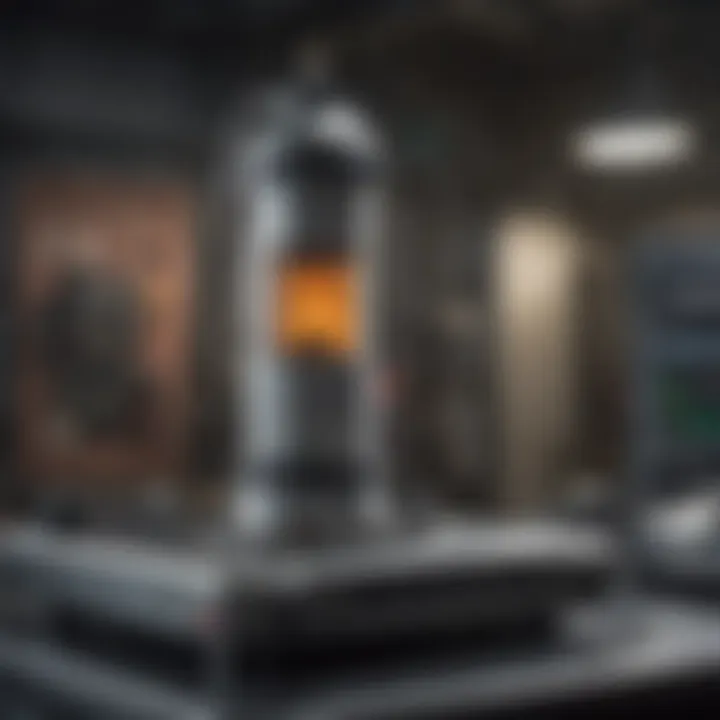
Moreover, transportation presents its own set of challenges. Calibration gases are often transported in high-pressure cylinders, necessitating stringent safety protocols to mitigate risks during transit. An incident during transportation can compromise the entire batch, leading to further implications for laboratories reliant on these gases.
Market Trends and Developments
Understanding the market trends and developments in the field of calibration gases is crucial. It not only mirrors the industry's adaptation to technological advances but also highlights how different sectors respond to growing regulatory demands and evolving user requirements. As industries become more interconnected and technology progresses, the calibration gas market experiences rippling changes that are significant for professionals, researchers, and educators alike.
Emerging Markets for Calibration Gases
Recently, several emerging markets have come to light. Asia-Pacific, for instance, is rapidly expanding its reach due to a rise in manufacturing and industrial activities. Countries like China and India are ramping up production capabilities, which in turn boosts the demand for calibration gases. This trend is not merely a fleeting phenomenon; it's a robust shift driven by increased environmental monitoring and quality assurance standards.
Furthermore, the Middle East is witnessing a similar surge. As oil and gas sectors strive for compliance with international standards, the calibration gas market gains momentum here as well. Companies are increasingly investing in calibration technologies to ensure precision and reliability in their operations. With all these developments, it becomes evident that the landscape of calibration gases is in constant flux, making it an area of keen interest for those in the related fields.
- Increased demand due to industrial growth
- Expansion in environmental regulations
- Higher standards in quality control
Impact of Environmental Regulations
Environmental regulations play a pivotal role in shaping the calibration gas market. As government bodies worldwide bolster laws aimed at ensuring air quality and reducing emissions, the call for precision in measurement grows louder. In many cases, industries are now required to monitor and report atmospheric pollutants, which underscores the need for high-quality calibration gases. This is not just about compliance; it’s about establishing a reputation for responsibility.
"Regulatory pressures serve as catalysts for innovation and performance in gas calibration."
The emphasis on sustainability has led to increased research into greener calibration options. Numerous companies are now exploring alternatives to conventional calibration gases that minimize environmental impact while providing the same level of accuracy. As these regulations tighten, the adoption of sustainable practices within the calibration gas market becomes not just advantageous, but essential for ongoing success.
- Stricter compliance measures encourage technology advancements
- Development of greener calibration gas options
- An increase in collaborative initiatives among industry players to improve practices
Analyzing these trends reveals an interconnected web of market dynamics, highlighting the ever-evolving nature of calibration gases. The direction taken by regulatory frameworks will heavily influence future developments in this field, pushing for innovation and sustainable practices that align with global environmental goals.
Future Directions in Calibration Gas Research
The world of industrial scientific calibration gases is ever-evolving. Understanding the future directions in this field is crucial for researchers, educators, and professionals engaged in environmental monitoring, industrial emissions testing, and more. The ongoing advancements in technology and a growing emphasis on sustainability promise to redefine how calibration gases are created, utilized, and managed. This section dives deep into the pivotal trends that could shape the future of calibration gas research.
Sustainable Gas Options
As environmental concerns take center stage, the push for sustainable gas options is becoming more pronounced in calibration gas research. The shift towards greener practices not only aligns with global efforts to tackle climate change but also addresses regulatory pressures that call for reduced carbon footprints.
Sustainable gas options can include:
- Biogas: Derived from organic materials, biogas can potentially serve as an eco-friendly calibration standard, reducing reliance on fossil fuels.
- Synthetic Gases: The development of synthetic gases designed to mimic natural calibration gases can help in customizing gases for specific applications while minimizing environmental impact.
- Recycling: Innovative methods for recycling calibration gases can reduce waste and promote a circular economy in industrial practices.
Adopting these sustainable options not only benefits the environment but can also lead to cost savings in production and disposal processes.
Advancements in Measurement Techniques
Precision and accuracy in measurement techniques are paramount in calibration processes. The advent of modern technologies is transforming how calibration gases are analyzed and utilized. Here are some notable advancements that are shaping future research in this domain:
- Nanotechnology: With the use of nanomaterials, sensors can measure concentrations of calibration gases with unprecedented sensitivity. This technology can revolutionize industries that rely on minute and accurate gas readings.
- Telematics: Implementing telematics allows for real-time monitoring of calibration gas usage, enhancing efficiency and ensuring compliance with regulatory standards.
- Data Analytics: The integration of big data analytics facilitates deeper insights into calibration gas performance and usage patterns, empowering organizations to make informed decisions.
These advancements not only improve the reliability of calibration processes but also offer a pathway to more integrated and sophisticated systems. Future research will focus on further refining these techniques and exploring new possibilities that arise from a convergence of disciplines.
"As we navigate into the future, the potential for innovation in calibration gas research is enormous, yet it bears the responsibility of fostering sustainability and precision."
In summary, the future of calibration gas research hinges on sustainable practices and technological advancements. By embracing these changes, industries can enhance the integrity of their scientific measurements, ensure compliance, and contribute to a healthier planet.
The End
The conclusion of this article serves as a critical juncture in reconciling the intricate relationship between industrial scientific calibration gases and their unwavering importance across various sectors. Calibration gases are not just mere tools; they play an instrumental role in ensuring that measurements are reliable and that methodologies are sound.
Summary of Key Takeaways
First and foremost, understanding calibration gases is vital for professionals who rely on accuracy in their work. Here are some key takeaways:
- Types of Calibration Gases: Familiarity with primary, secondary, and custom calibration gases aids in choosing the right gas for specific applications. Each type varies in composition and purpose, tailored for unique needs.
- Applications Across Industries: Calibration gases are ubiquitous, serving essential functions in different fields, such as environmental monitoring and medical equipment calibration. This versatility underscores their significant impact.
- Regulatory Compliance: Adhering to global standards ensures the integrity of scientific measurements. Knowledge of the regulatory framework supports compliance and underscores the need for systematic practices.
- Best Practices: Proper handling and storage of calibration gases safeguard accuracy. Emphasizing safety measures not only protects personnel but ensures precise results in testing.
- Technological Advancements: Innovations are shaping the future of calibration gases. Automation and enhanced analysis techniques present opportunities for greater efficiency and accuracy in measurement practices.
Implications for Future Research and Practice
The landscape of calibration gas research is ever-evolving. Given that industries are increasingly pushing for enhanced precision and compliance, future studies must address the development of sustainable gas options. This transition not only reduces the environmental footprint but also ensures the longevity and reliability of calibration practices.
Moreover, refining measurement techniques will be paramount. As methodologies evolve, incorporating the latest technologies provides ample opportunities for improving accuracy.